The High Stakes of Investment
Building a modern mineral processing plant is a huge investment, often costing millions. During the design phase, it’s tempting to cut costs wherever possible. Unfortunately, sampling and measurement equipment often become easy targets for these cuts. But this can lead to some serious long-term problems.
Learning from Hard Experience
This advice comes from years of hands-on experience at hundreds of sites around the world. Skipping on sampling and measurement might seem like a quick win, but it usually turns out to be a big mistake. Accurate measurement is essential for optimizing plant performance.
The False Economy of Cutting Corners
Imagine opening a corner store without a cash register. It’s the same as running a plant without proper sampling and measurement tools. You won’t have the data you need to see what’s really happening, leading to inefficiencies and even losses. Accurate measurement is crucial for maintaining control and efficiency.
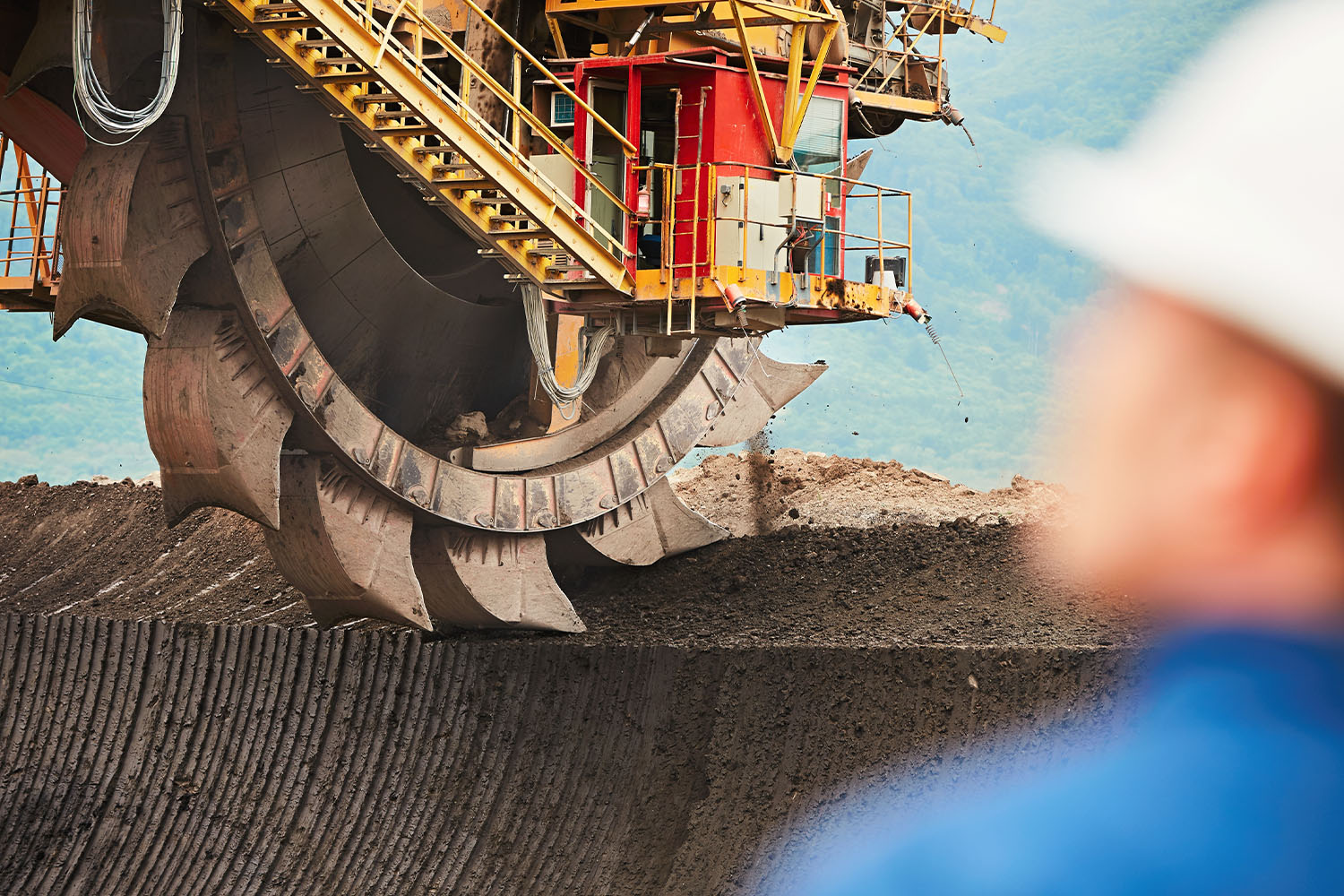
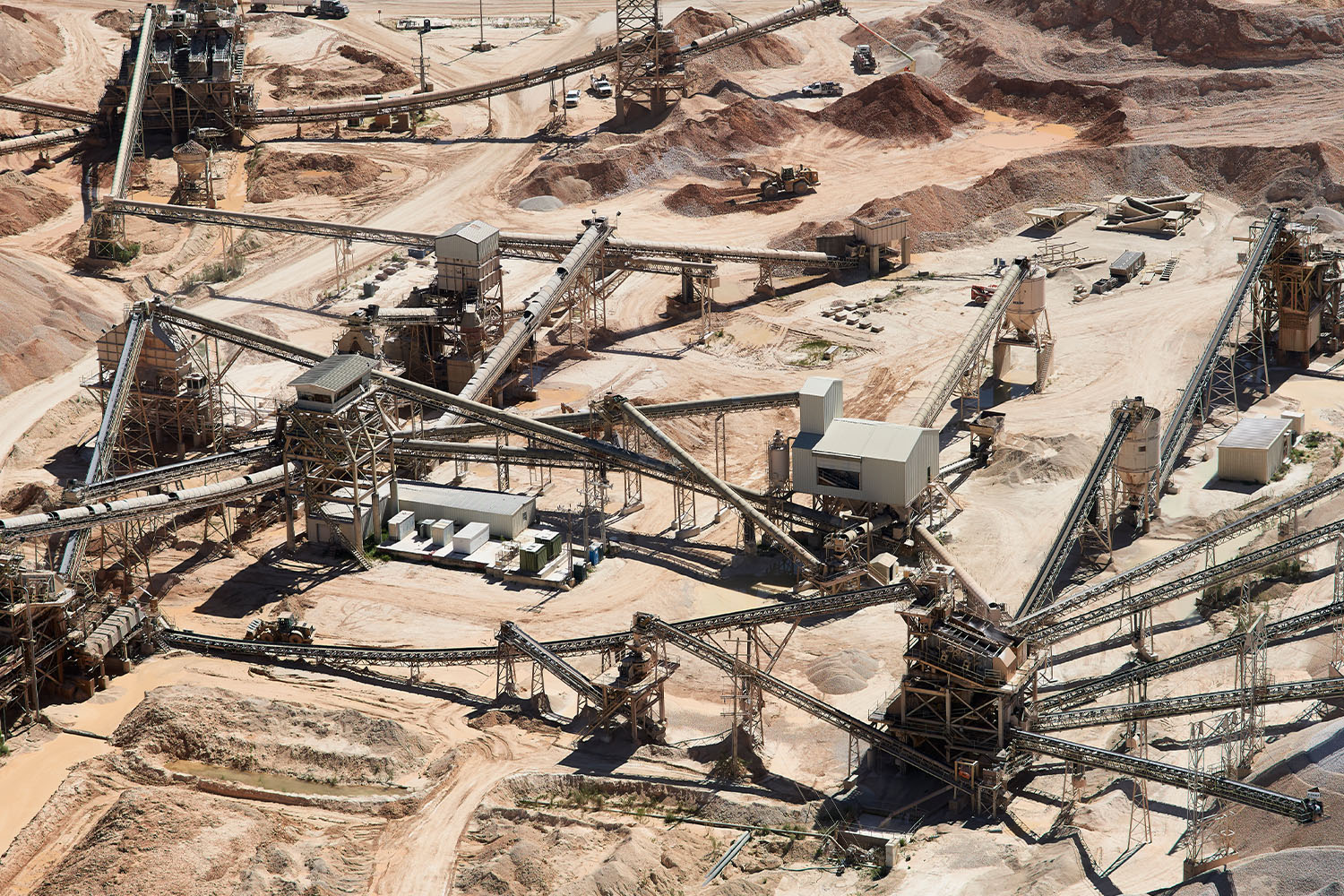
The Foundation of Optimisation
Without good sampling and measurement, how can you really know if your plant is running optimally? Investing in these tools during the design phase is not just smart but essential. Accurate data makes decision-making easier and more effective, boosting the plant’s profitability.
Small Gains Add Up
If a mineral processing plant, for example sees a small improvement in throughput while still keeping the particle size at target, it adds up to thousands of tons per year. With current ore prices this is huge savings annually. Small, consistent improvements can make a huge difference over time. Skipping on sampling is like throwing money away.
The Real Cost of Ignoring Measurement
The importance of accurate sampling which provides measurement data cannot be overstated, it allows the plant to monitor or optimize processes effectively, helping boost efficiencies and lowering costs. If plant managers, operators and engineers have data they can improve the plant, without it they are blind.Building a Strong
Measurement Culture
If you’re designing a plant, watch out for cost cutters—they’re usually profit cutters in disguise. Skipping on sampling and measurement equipment sacrifices functionality. It’s much cheaper, more straightforward with a better sampling outcome to include these systems during the design phase than to add them later. Retrofitting samplers into an established process is possible but compromises typically need to be made.
Leveraging Expertise
Designing your own samplers is a bad idea. Good samplers and measurement tools aren’t cheap, but trying to develop them yourself in an operating plant is even more expensive. Stick with established suppliers and learn from their existing customers’ experiences.
Ensuring Safe Access
Using established suppliers to design your samplers means they are designed with safety in mind. This is a very important point as sample collection can be a hazardous business in any process but bulk materials travelling at speed are particularly challenging. Good safe access to material flows lets operators spot problems and take samples easily. Designing for safe and easy access during the planning stage costs little but pays off big in the long run.
Incorporating Sampling Regimes In Plant Design
Developing a strong measurement culture from day one is important; it’s hard to add later.
It is also recommended to provide sampling access to every new stream and monitor the flow rates. Adjust equipment placement to allow for sampling points and design slurries and pulps to pass in channels for accurate sampling. Justifying sampling as part of the plant design is crucial so samplers are part of the plan.
Measurement for Success
Investing in sampling and measurement equipment comes at a cost but it’s a necessity for a successful plant. These tools ensure you have the data needed to control, optimise, and maintain high-quality output. Cutting corners here is a false economy that can jeopardise the entire project. JWII are available to help and with the completion of sampler projects over the last 40 years have a knowledge base to draw upon to advise our clients on the right solution from the design phase of the plant. Please feel free to contact us and speak to one of our sampling experts who will gladly guide you through the selection process.