Introduction to Ultrasonic Defoaming Technology
As an engineer with a keen interest in the beverage industry, I’m excited to talk about a game-changer: ultrasonic defoaming technology. Bubble-Tech, at the forefront of this innovation, is changing beverage production efficiency and quality. This technology, with proven success in the beer industry, is now demonstrating its versatility in non-alcoholic beverages. I’ll guide you through four detailed case studies that showcase its significant impact.
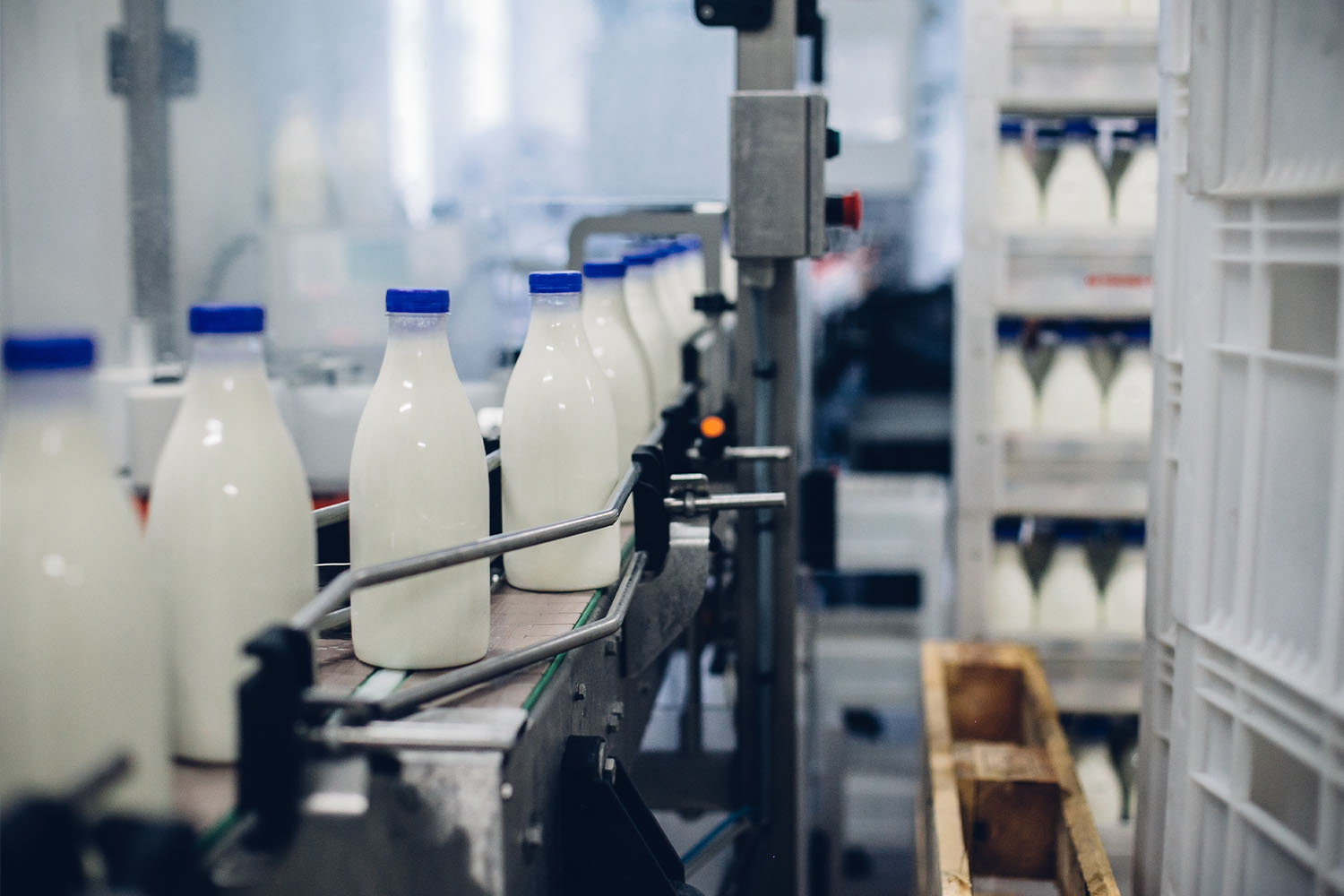
Case Study 1: Dairy Bottling Line’s Resurgence
Consider a dairy company whose production line was hindered by 25% due to persistent foaming, a common challenge exacerbated by a variety of flavored products. Previous attempts to mitigate the issue had been unsuccessful, resulting in not just efficiency loss but also increased contamination risks, as over-foaming bottles left behind residue, complicating hygiene standards.
Innovative Ultrasonic Solution In this scenario
The Bubble-Tech S-300 unit emerged as the hero. Engineered for handling up to 32,000 bottles per hour, this unit was adept at tackling high foam levels. Its swift and efficient installation was key, causing minimal disruption to ongoing operations. Once operational, the unit significantly enhanced the line’s speed and dramatically reduced contamination risks.
Enhanced Results and Economic Impact
The deployment of the S-300 unit increased filling speeds from 24,000 to 32,000 bottles per hour, marking a substantial efficiency improvement. This increase in productivity led to a 50% reduction in cleaning time and associated costs. Impressively, the financial benefits of this technological intervention were evident within just a few months, signifying a rapid return on investment.
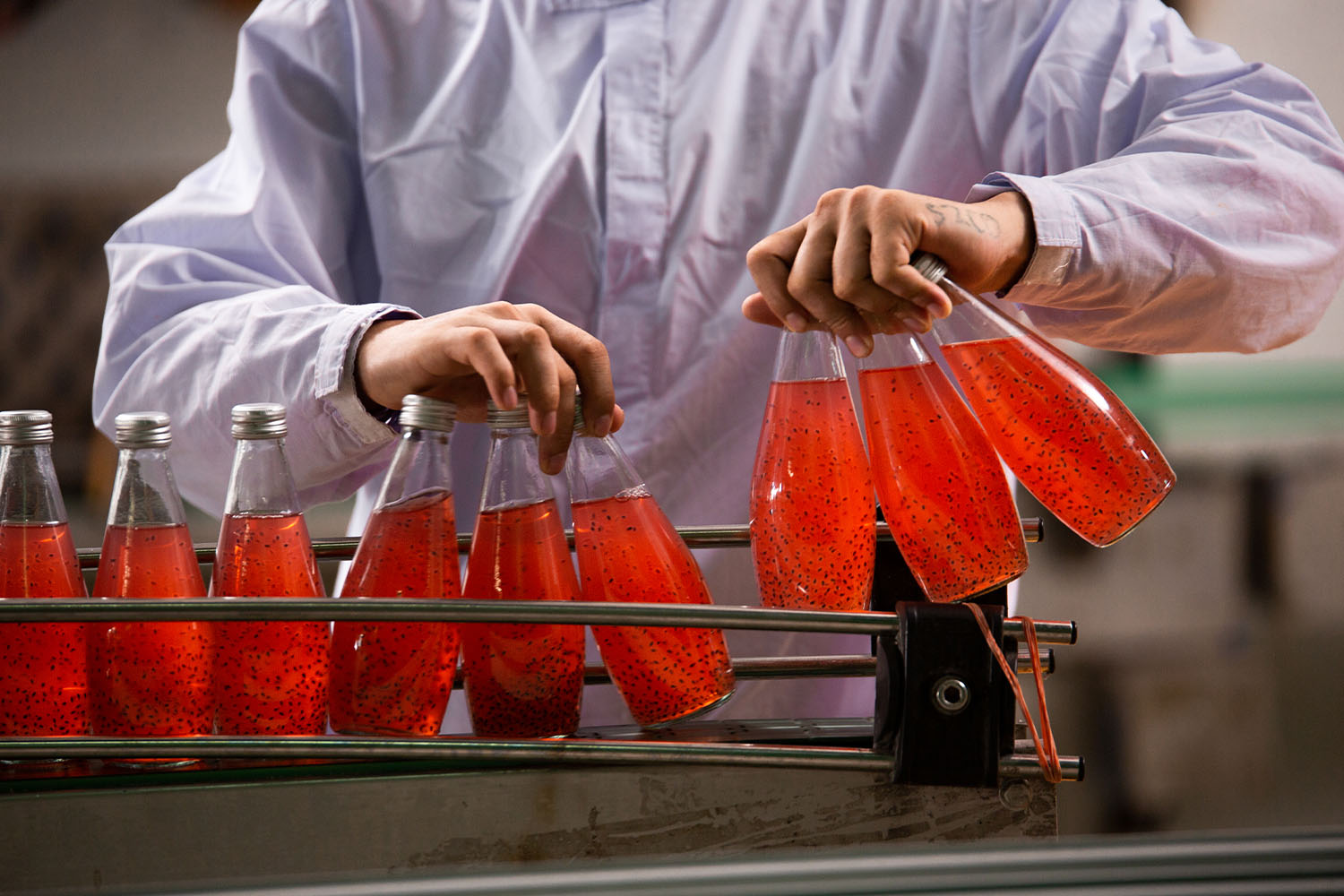
Case Study 2: Addressing Challenges in Multinational Beverage Bottling
Another success story comes from a multinational beverage company plagued with over-foaming issues, resulting in a loss of 2.5ml per 330ml bottle. This was not just about product loss; it was also impacting their operational bottom line due to a 0.5% reject rate from under-filled bottles.
Efficiency with Bubble-Tech’s S300
Here, the S-300 unit again indispensable. Its efficient integration into the bottle line led to a drastic reduction in foam loss and decreased the reject rate from 0.5% to 0.2%. These improvements translated into considerable savings across various operational fronts, including reduced beverage loss, waste treatment savings, and decreased reject rates. The company achieved a return on their investment in under six months, illustrating the unit’s effectiveness in enhancing production efficiency and reducing wastage.
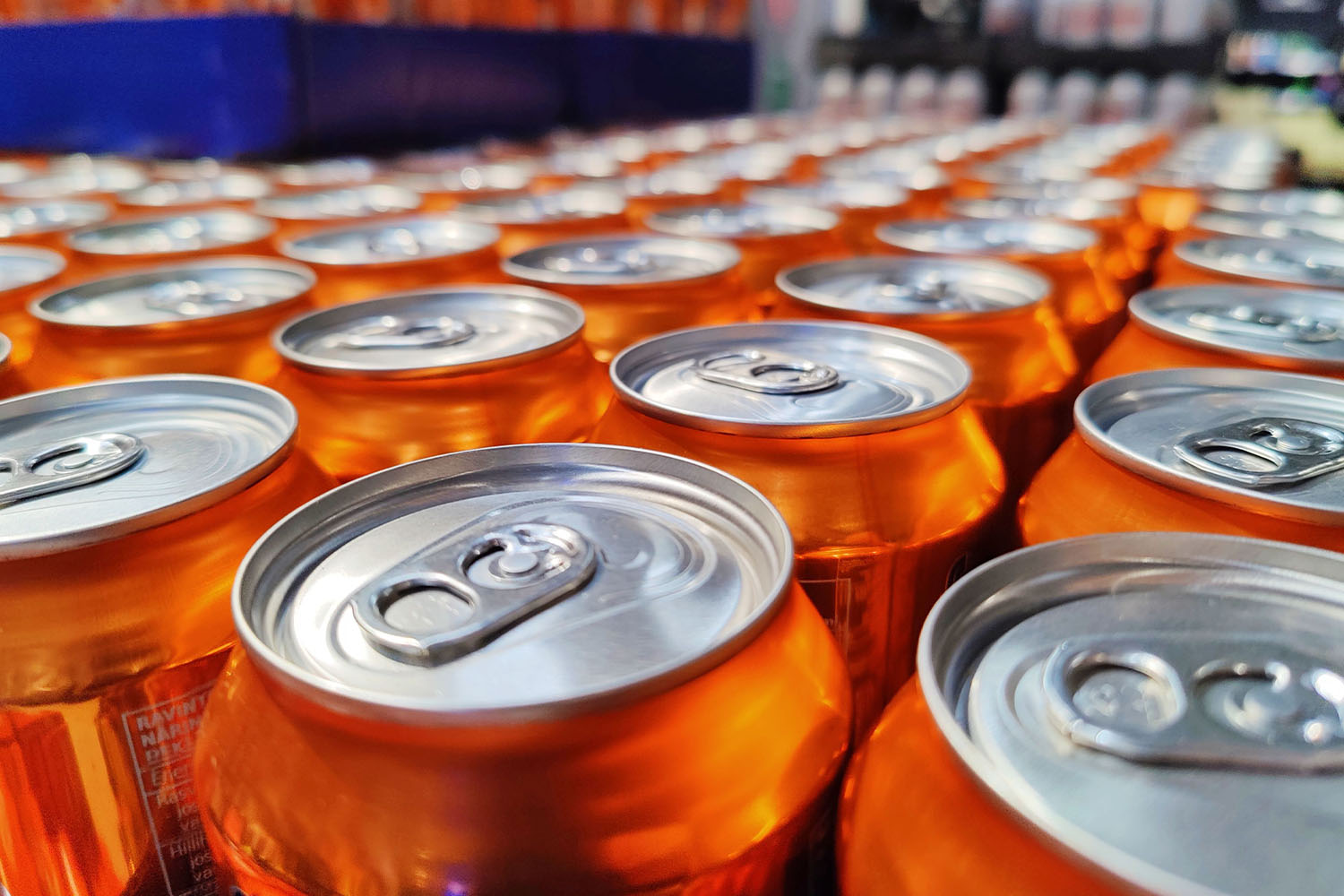
Case Study 3: Revolutionizing Can Filling Processes in Soft Drink Manufacturing
Our final case study focuses on a soft drink manufacturer filling 330ml cans at an impressive rate of 100,000 cans per hour. The challenge? Maintaining optimal filling temperatures for both regular and diet beverages without inducing excessive foaming. Previously, this required chilling the beverages to an inefficient 4°C, leading to increased energy consumption and costs.
S-500: A Tailored Solution for High-Speed Lines
In this context, the S-500 unit from Bubble-Tech, designed for higher throughput, was the solution. It enabled the maintenance of a filling temperature of 10°C, effectively eliminating the need for excessive chilling. This adjustment led to significant savings in both chiller energy costs and re-warming energy costs, as well as avoiding the expenditure on a new chiller. The return on investment for this technology was realized in just 8 months.
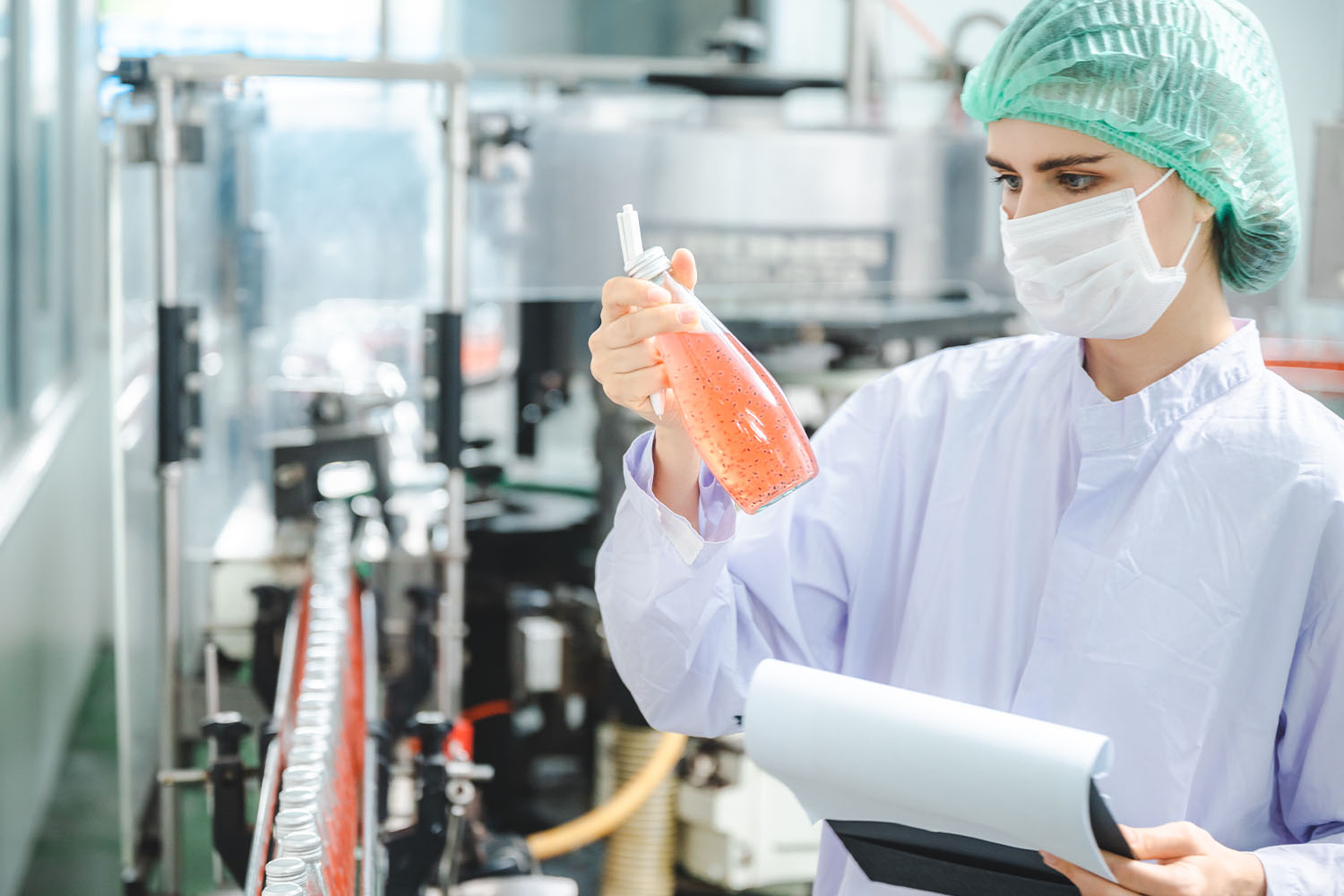
Case Study 4: Enhancing Productivity in PET Bottle Filling
Challenges in High-Speed PET Bottle Filling
Imagine a production line in a bustling beverage factory, where a Sidel PET bottle filler is the heart of the operation. Here, a significant challenge presented itself: foaming issues necessitated a reduction in filling speed from 60,000 bottles per hour (bphr) to 40,000 bphr. This 33% decrease in productivity was a major concern, as it directly impacted the factory’s output and efficiency. The need for a solution was urgent, not only to restore the original filling speed but also to ensure the quality and consistency of the beverage.
Ultrasonic Defoaming offered a solution
In this critical situation, Bubble-Tech’s S-500 was installed. Designed to handle high-volume production lines, the S-500 was tasked with tackling the persistent foaming problem. Its non intrusive installation bringing about a significant change without disrupting the existing workflow.
Revolutionizing the Filling Process
The introduction of the S-500 unit had an immediate and transformative impact. The foaming issue was effectively addressed, allowing the filling speed to ramp back up to the initial 60,000 bphr. This increase not only restored the line’s efficiency but also marked a substantial productivity improvement of 20,000 bphr. In a high-demand production environment, this kind of efficiency gain is invaluable, translating into increased output, better resource utilization, and enhanced profitability.
Rapid Financial Return
The financial aspect of this intervention was equally impressive. The capital expenditure (capex) investment in the S-500 unit yielded a payback in less than four weeks. This rapid return on investment is a testament to the efficiency and effectiveness of the ultrasonic defoaming technology in a high-speed production setting. It underscores the potential for such technologies to provide swift financial benefits while solving long standing operational challenges.
Broader Implications in the Beverage Industry
These case studies exemplify how ultrasonic defoaming technology is not merely a solution for reducing foam; it’s a comprehensive approach to enhancing overall production efficiency, reducing costs, and promoting sustainability in the beverage industry. A Key tool for any producer with simple and easy installation with minimal to no line disruption and fast ROI to help with the bottom line.
Embracing Technological Progress in Beverage Production
As we continue to explore innovative solutions in the beverage industry, technologies like Bubble-Tech’s ultrasonic defoaming units stand out as significant advancements. They address longstanding production challenges and signal a new era of efficiency and sustainability. For engineers and industry professionals, this is an exciting time to be in the field, anticipating and participating in the wave of technological advancements shaping the future of beverage production.
JWII are here to help
If you have a particular beverage challenge and would like to discuss Bubble-tech or any of the other exciting technologies from JWII please feel free to contact one of our friendly staff who would be more than willing to help.