The cement industry, a backbone of infrastructure development, is constantly evolving with technology. Integral to ensuring the quality and consistency of cement, sampling is now on the cusp of a technological revolution, thanks to automated equipment. Let’s explore the facets of this advancement through the following key aspects.
The Imperative of Sampling
Sampling is the unsung hero of cement quality assurance. Companies like Sentry Equipment supply an array of robust cross-cut and point samplers which are precision-manufactured to handle cement sampling during various stages of the production process. Cement can be an abrasive material, so the samplers are designed using suitable hard waring materials of specific coatings.
Automated Sampling Technology
Automation has brought about a sea change in sampling technologies. Sentry’s pneumatic-powered systems, managed by electronic controllers, illustrate the industry’s movement towards more controlled, accurate, and reliable sampling processes. This automation allows the user to obtain precise and accurate point or composite samples of the material. The automatic sampler can be configured to take a sample over a set period of production, sampling a small amount of material each time to build a real picture of the product over a batch, day, week for example.
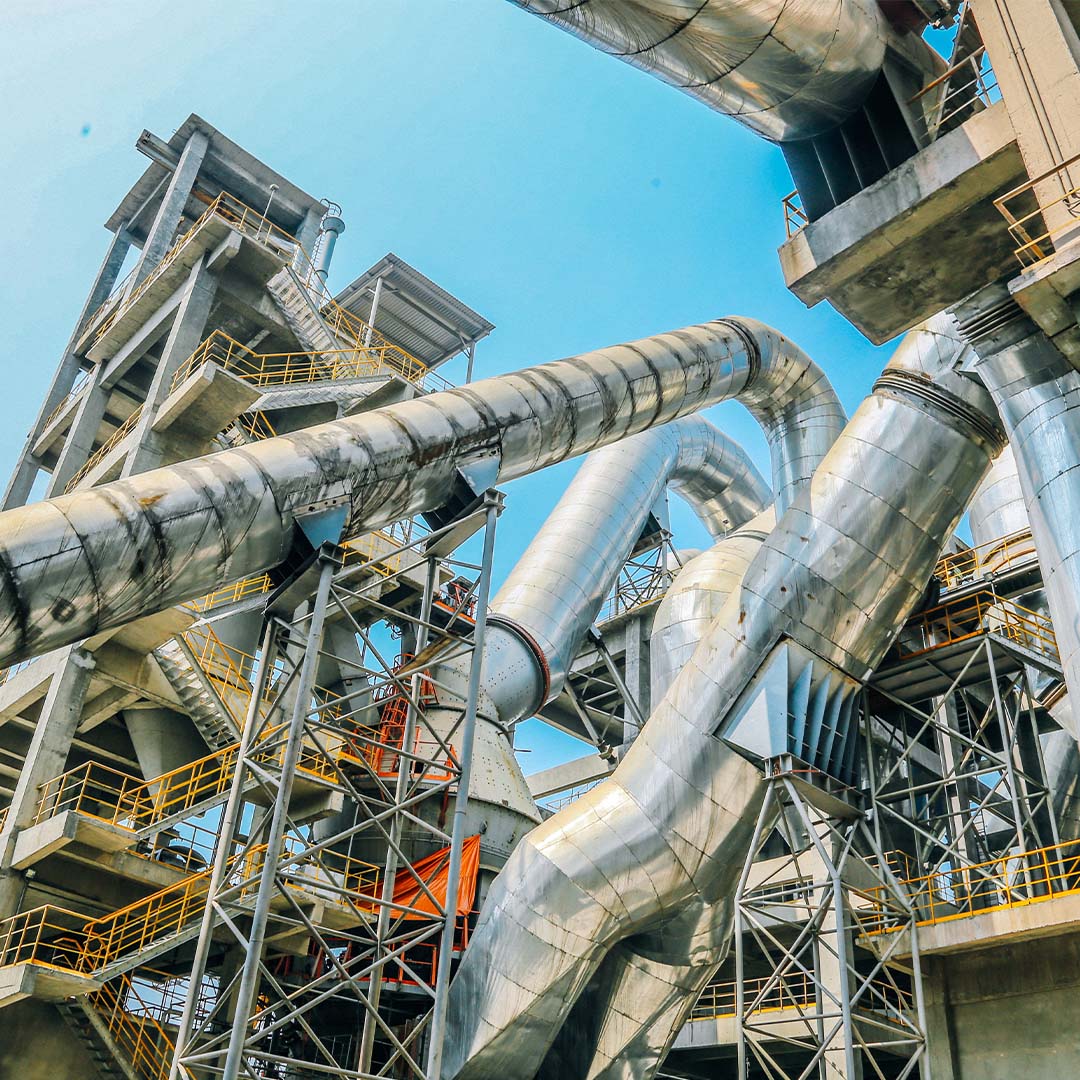
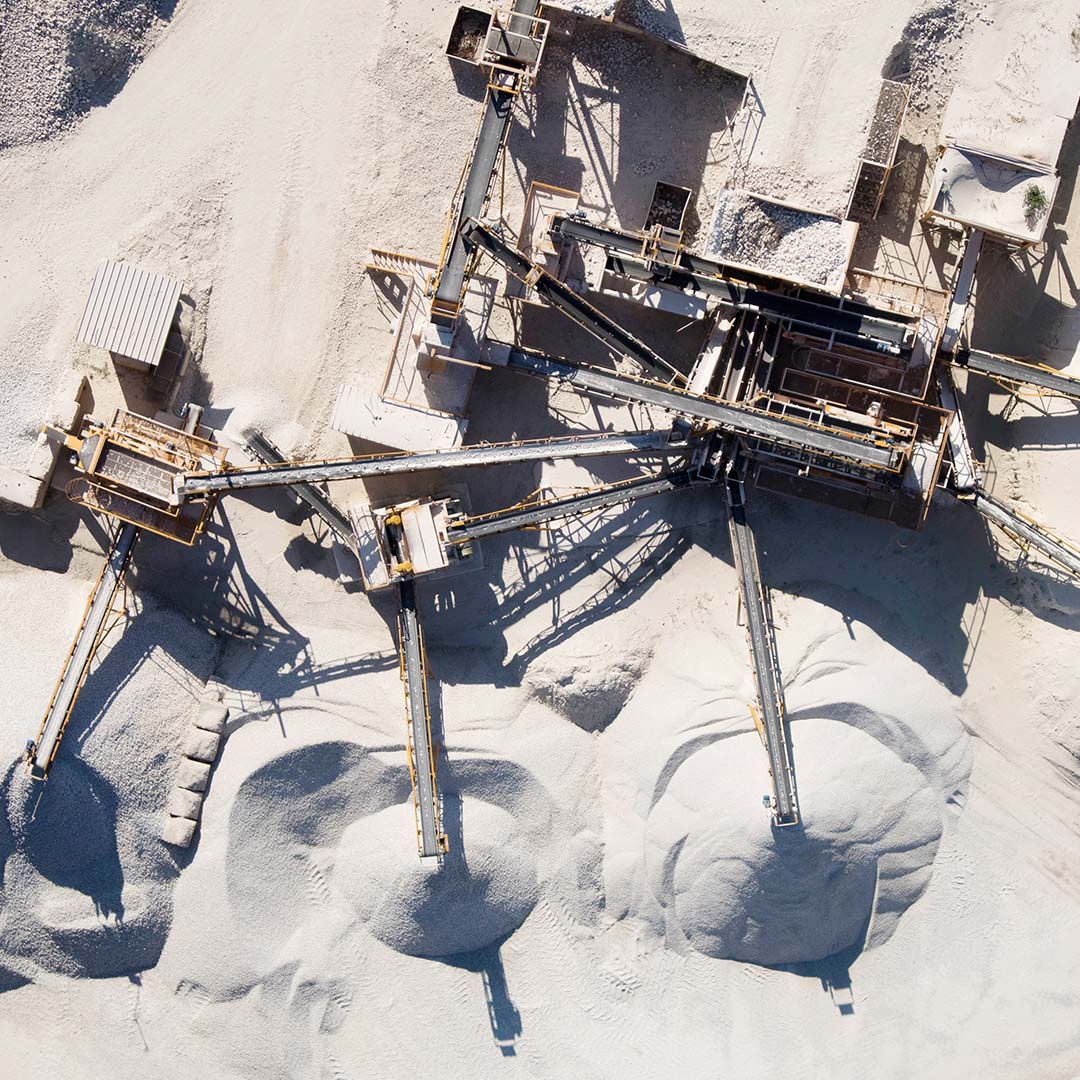
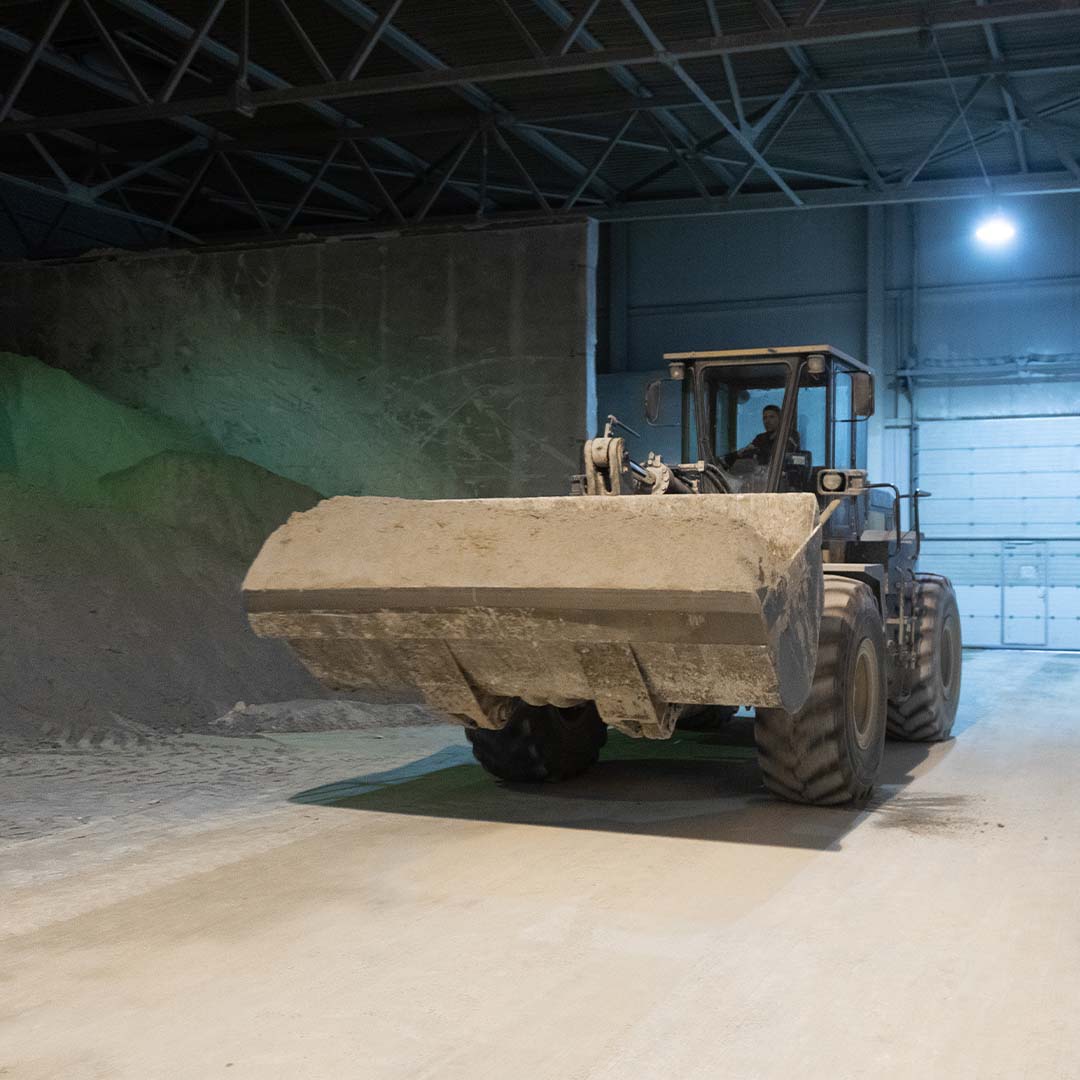
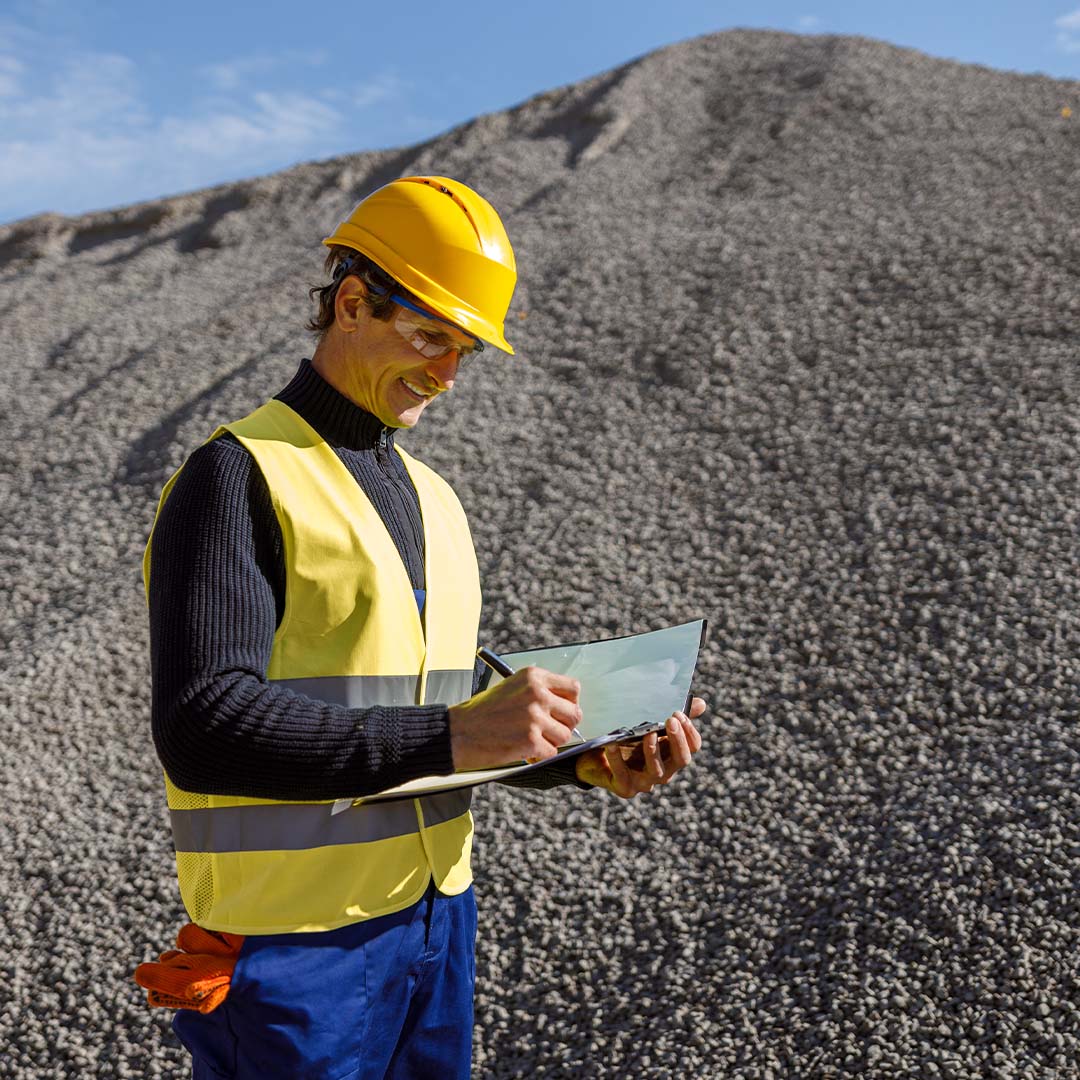
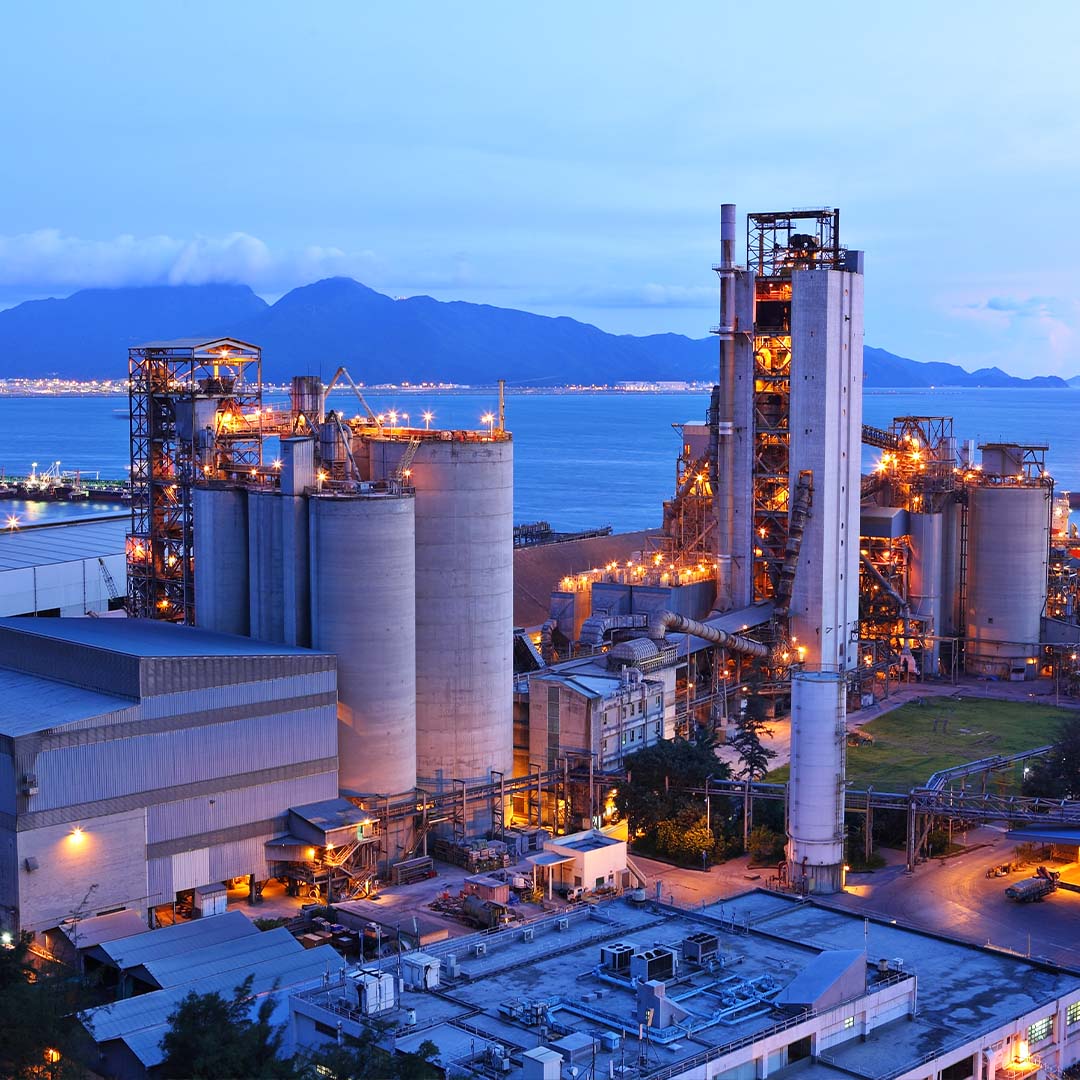
Sampling Frequency and Timing
The timing of sampling is as crucial as the process of sampling itself. Automated systems, like those from Sentry offer meticulously timed samples, ensuring that the sample reflects true process conditions, leading to more representative and actionable insights. A good example of this is for cement sampling during the loading of a truck or rail car. It is important to have traceability so each load should have a composite sample. With the use of the correctly selected sampler and controller this can be achieved with great precision.
Quality Control and Optimization
Automated samplers serve as guardians of quality control, helping QC staff and production personnel monitor the entire cement processes and the final product. Samplers not only allow samples to be taken from difficult parts of the process but also ensure compliance and assist to optimize the entire production line, contributing to a higher grade of cement ready for dispatch.
Particle Size Analysis and Control
The fineness of cement particles is directly linked to the products performance. Therefore this type of analysis is required throughout the production cycle. Specifying the correct sampling device is critical and the sampler itself should not change the product especially the particle size and distribution. This can be achieved by using the correct material and sampler type along with handling the sample to sample container transport via smooth sample discharge with a short gently sloping path so the integrity of the sample is maintained.
Integration with Process Control Systems
Today’s automated samplers integrate seamlessly with control systems, providing real-time monitoring. Signals can be provided to advise the plant control that a sample is being taken. Sample containers can also be monitored, and a full signal be sent to the QC team to request collection of the sample for analysis. The plant control system can even be used to initiate the sampler either sing a timer or manually by the operator at a specific time on the process.
Safety and Efficiency
Automated sampling brings unparalleled safety and efficiency. Operators are no longer exposed to the dangers of manual sampling, reducing accidents, and enhancing operational safety across the board. Gone are the days of plant personnel grabbing a sample from the back of a truck manually or climbing the plant to get too difficult places to extract a sample. Using Automated samplers, safety becomes the priority while also improving the sample efficiency.
Cost-Effectiveness and Asset Preservation
Not only do automated samplers safeguard the quality, but they also preserve plant asset values and lower production costs. Consistent, accurate samples lead to energy savings, better product quality, and, ultimately, superior market competitiveness.
Customization and Versatility
With the diverse requirements of cement plants, customization is key. Sentry offers a wide array of pre-engineered solutions, with the flexibility of custom-built systems, ensuring that every plant’s unique needs are met with precision and efficiency. Each sampler is designed against the cement plant sixing, so each automatic sampler is made to fit that specific application. Stroke length, auger size, aperture size, motor ratings and pneumatic cylinder size along with a host of other parameters are customised for that specific application in that specific cement plant.
Future of Automated Sampling in Cement Production
Automated sampling is set to become even more integrated, intelligent, and indispensable. The continuous refinement of sampling technologies promises to keep cement production at the pinnacle of quality and efficiency.
Automated sampling in cement production is not just about adhering to standards; it’s about exceeding them. It’s a commitment to excellence that Sentry Equipment exemplify through their innovative solutions. As the industry moves forward, automated sampling stands as a pillar of progress, ensuring that the quality of cement remains nothing less than exemplary.
Equipment referred to in this article
-
Sentry Equipment
Sentry SA Automatic Cross-cut Sampler
-
Sentry Equipment
Model B1 Point Sampler
-
Sentry Equipment
Model RX Strip Sampler
-
Sentry Equipment
Model RB Strip Sampler