Introduction to Ultrasonic Defoaming Technology
In the world of beverage production, especially in breweries, managing foam is a crucial aspect of maintaining efficiency and quality. Ultrasonic defoaming, a technology pioneered by companies like Bubble-Tech, is making significant strides in this area. Utilizing ultrasonic sound waves, this innovative approach not only tackles the challenge of foaming in bottles and cans but also enhances the overall packaging operation. This blog delves into various case studies to explore the effectiveness of this technology in the beer, dairy, and chemical industries
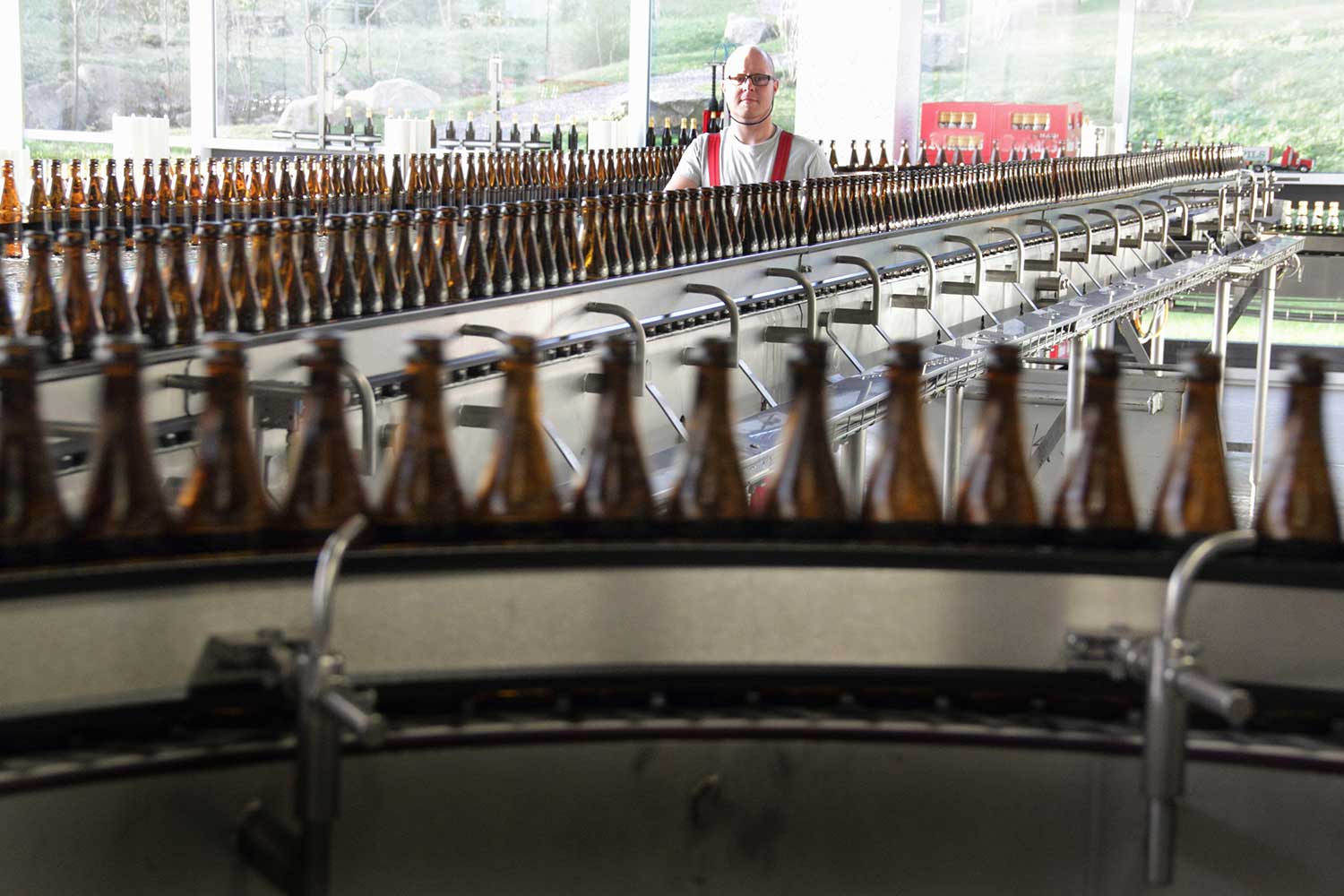
Case Study 1: Increased Filling Speed in European Beer Bottling Line
A large European brewery grappling with the challenges of filling speed saw a transformative change with the introduction of ultrasonic defoaming technology. Initially facing issues with over-foaming, which severely hampered their operational capacity, the brewery adopted Bubble-tech’s defoaming solution. This move not only addressed the foaming issue but also optimized their entire filling process.
Implementation and Advantages of Foam Control
The implementation of the defoaming unit was a seamless process, minimizing downtime and maximizing efficiency. The technology brought forth several advantages, including increased productivity, reduced liquid losses, and significant production efficiency gains. This not only improved the brewery’s operational capacity but also had a positive impact on their bottom line.
Results: Enhanced Productivity and Efficiency
Post-implementation, the results were clear and significant. There was a marked increase in filling speed, longer run times, and a notable reduction in downtime for cleaning. Financially, the brewery benefited from reduced operational costs and waste treatment expenses, leading to a quick payback period and overall cost savings.
CO2 and Energy SavingsÂ
One of the standout benefits of ultrasonic defoaming technology in this case is its contribution to reduction of CO2 usage. With the high cost of CO2 beer producers can use this technology to reduce CO2 usage on the line. Another benefit is increasing the filling temperature, the brewery was able to cut down on energy consumption during chilling and pasteurization. Moreover, the technology contributed to reduced CO2 and water consumption, aligning with the brewery’s corporate sustainability KPIs.
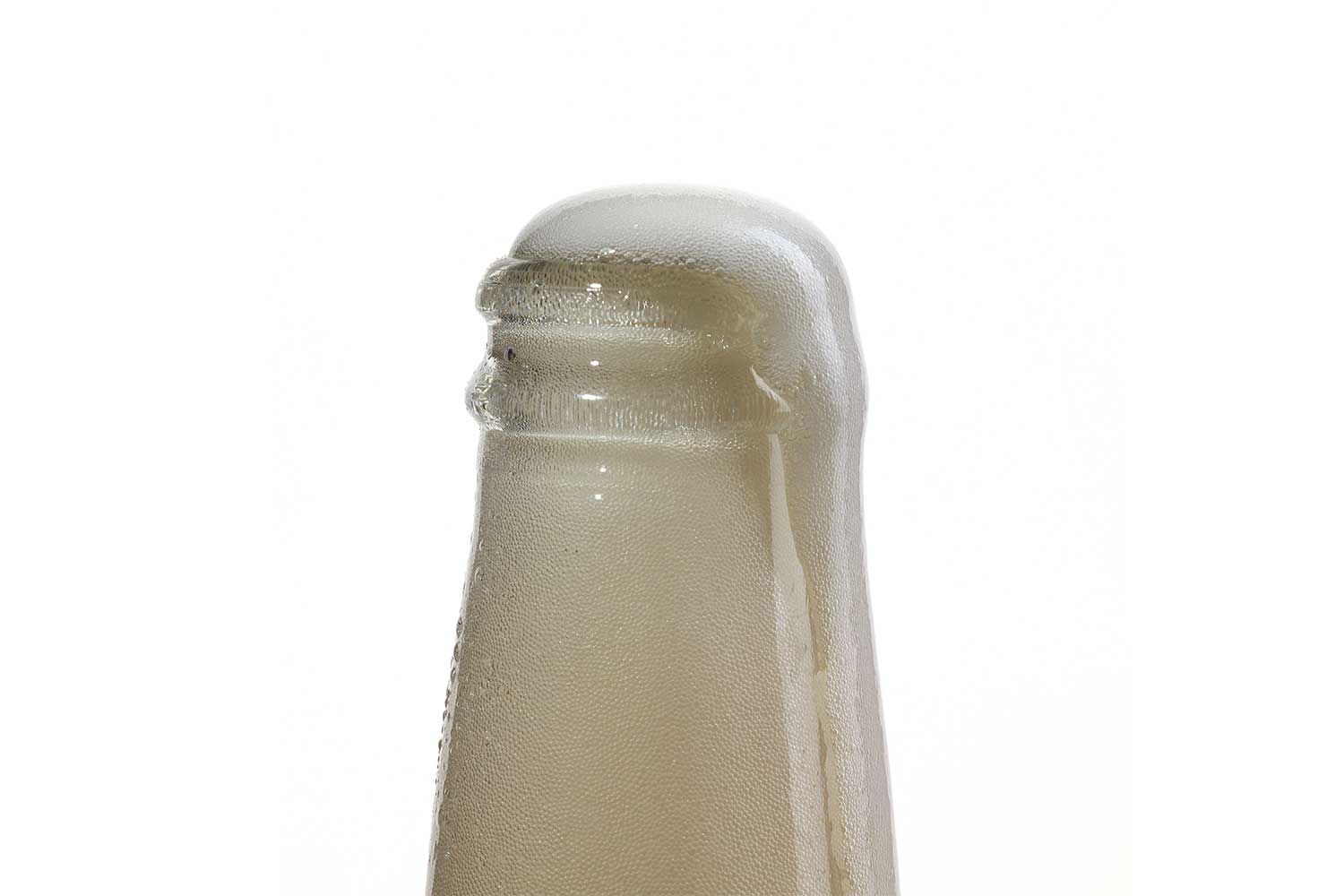
Case Study 2: Reducing Over-foaming and Reject Rate
A brewery in the Asia Pacific region faced challenges with over-foaming and high reject rates. The implementation of Bubble-tech’s de-foaming technology brought about a significant reduction in foam loss, beer extract losses, and bottle rejects, showcasing the versatility and effectiveness of this solution in different operational scenarios.
Hygiene and Quality Improvements
Beyond operational efficiency, ultrasonic de-foaming technology also enhanced hygiene and quality within the filling process. It effectively eliminated contamination risks on caps, seals, and packages, ensuring a higher standard of product quality and safety – a critical factor in the beverage industry.
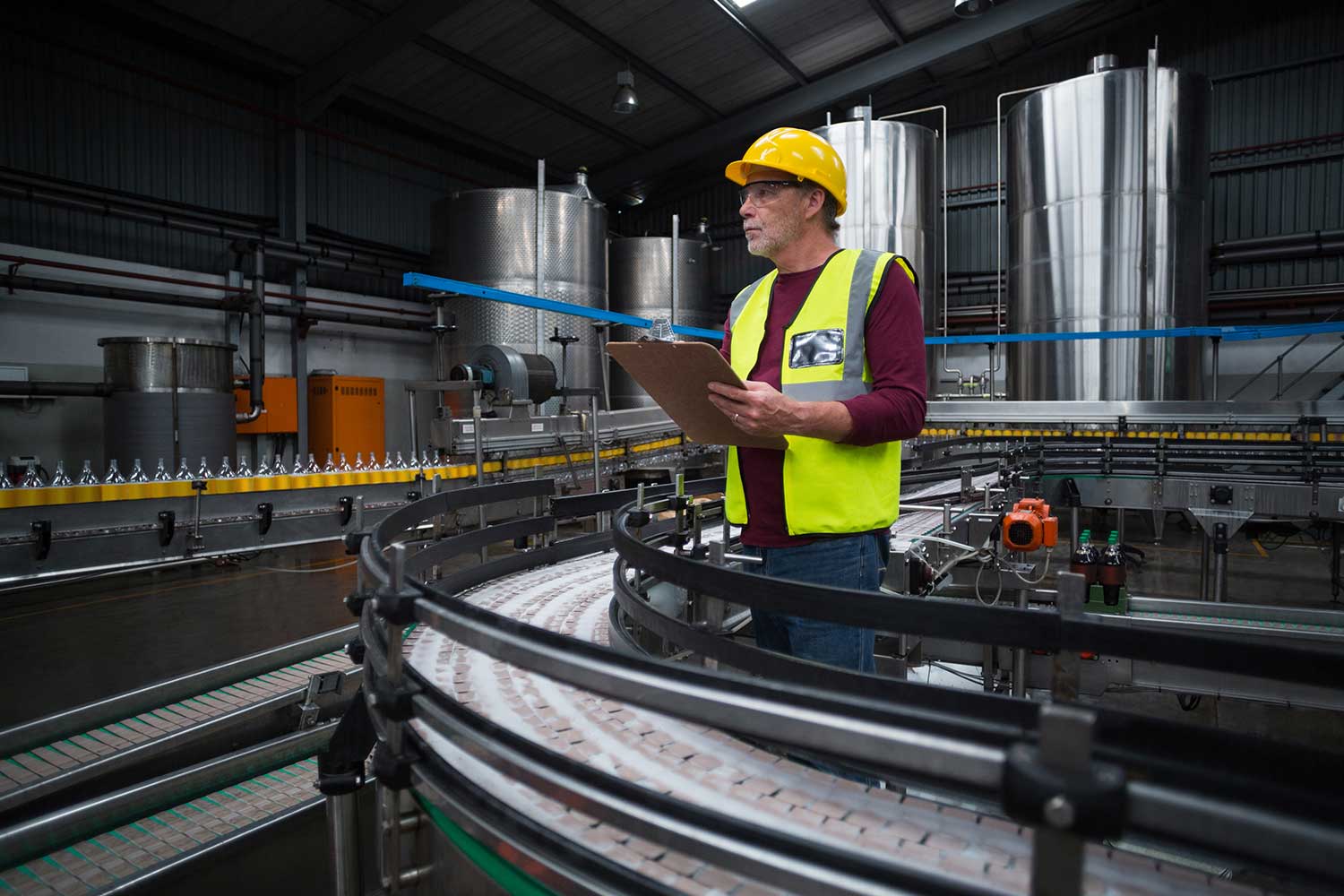
Case Study 3: Innovative CO2 and Temperature Management in Can Line Filling
An Australasian brewer was filling 330ml cans at a rate of 80,000 per hour, facing challenges with the required chilling to 5°C from 10°C, aimed at reducing foaming. This process involved significant energy consumption for both chilling post-pasteurization and rewarming post-seaming to avoid condensation and quality issues. They also had a very high CO2 cost and wanted to reduce or eliminate the use of CO2 bubble breakers.
Implementation of the Ultrasonic De-foaming system
Capable of handling up to 120,000 cans per hour an ultrasonic defoamer S-500 was used, this was to address high foam levels and operational speed. This solution allowed for maintaining a filling temperature of 10°C, thereby eliminating the need for additional chilling to 5°C and reducing energy consumption significantly.The S-500 system’s efficiency negated the need for a costly chiller installation (saving capex) and decreased yearly energy costs.
Due to large increases in CO2 cost this brewer wanted to reduce or eliminate CO2 bubble breakers on their can line fillers. This was achieved by the installation of the Bubble-tech de-foamer.This brewery saw an ROI payback period of less than 6 months.
This example exemplifies the substantial benefits of optimizing filling temperatures in beverage production, achieving significant energy savings and operational efficiency while maintaining product quality.
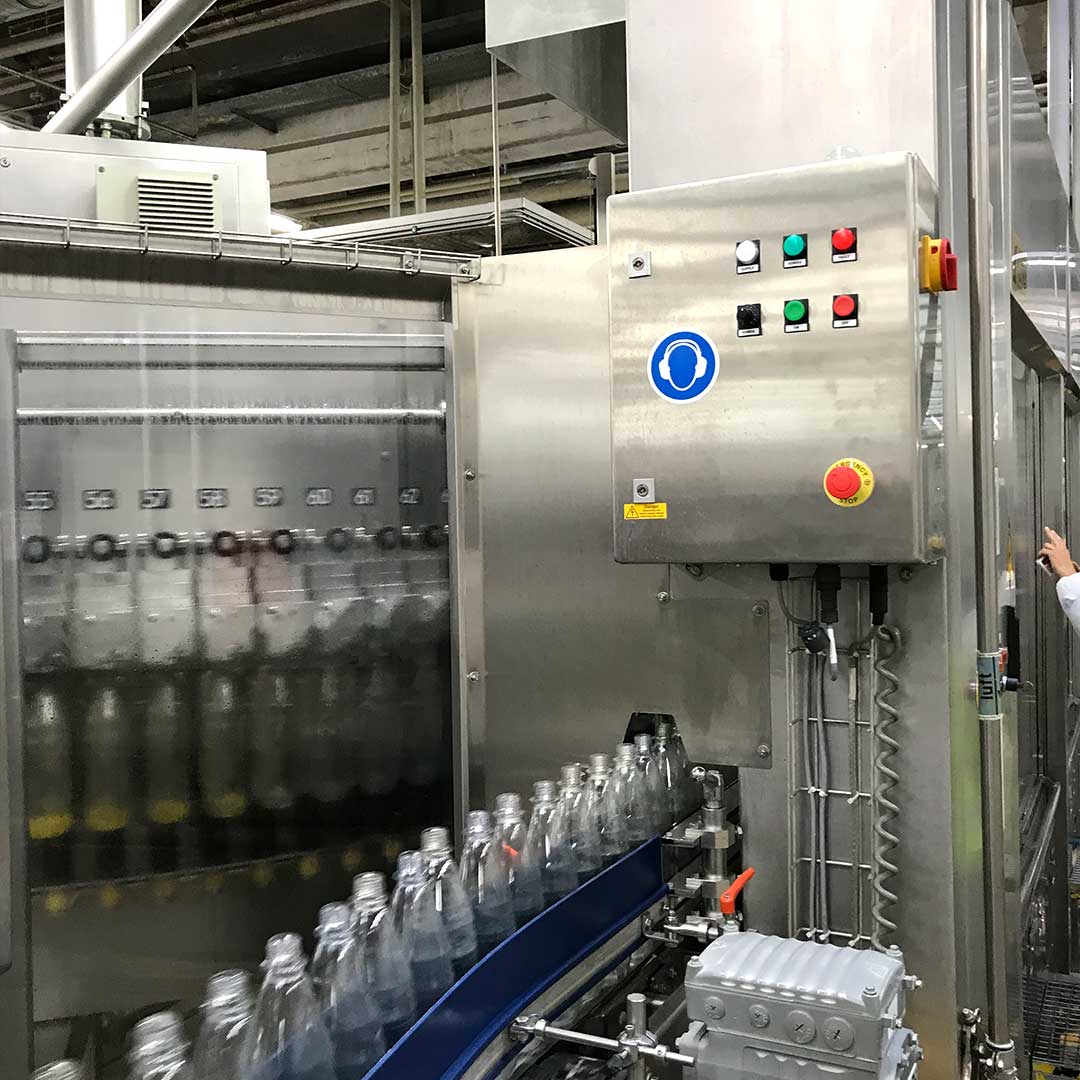
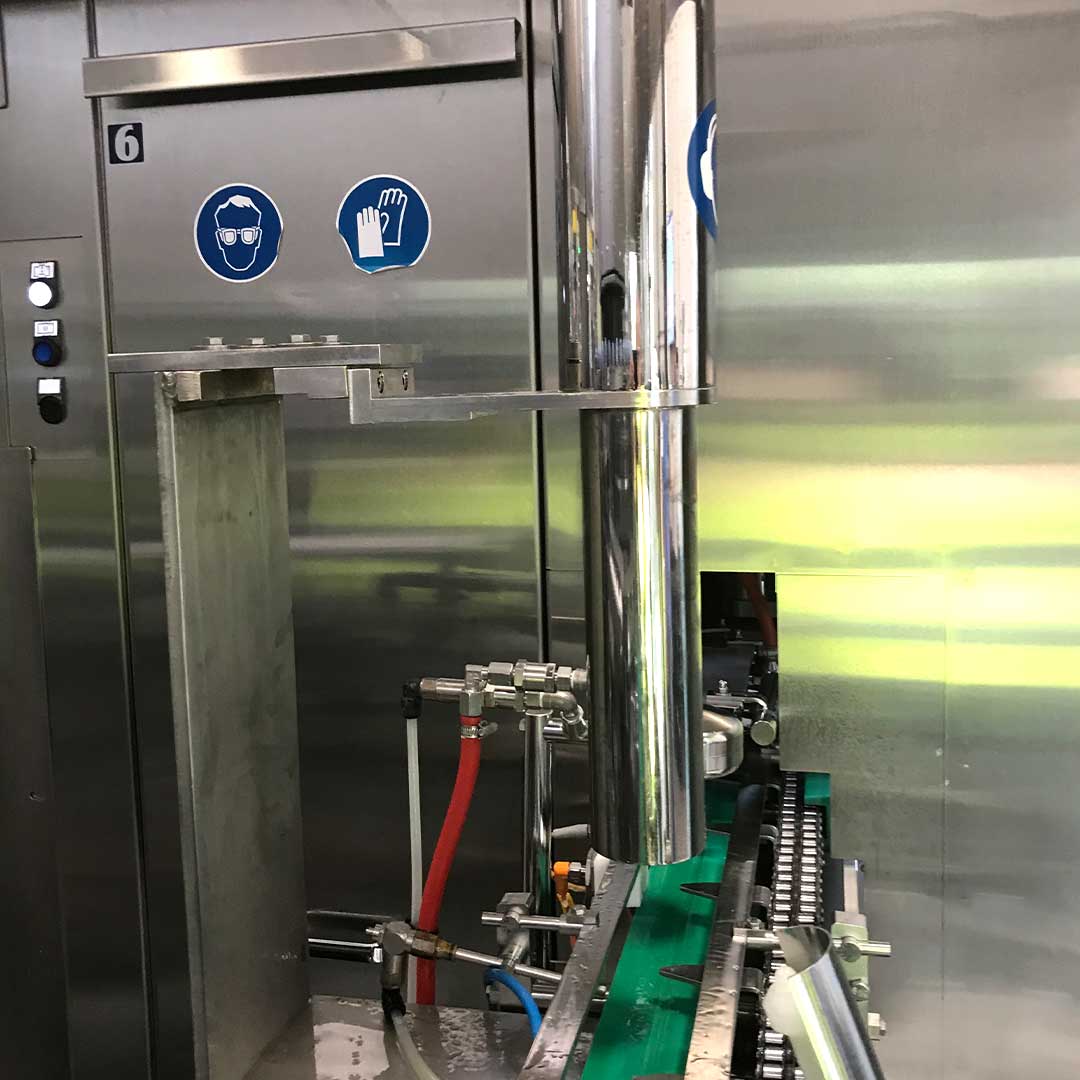
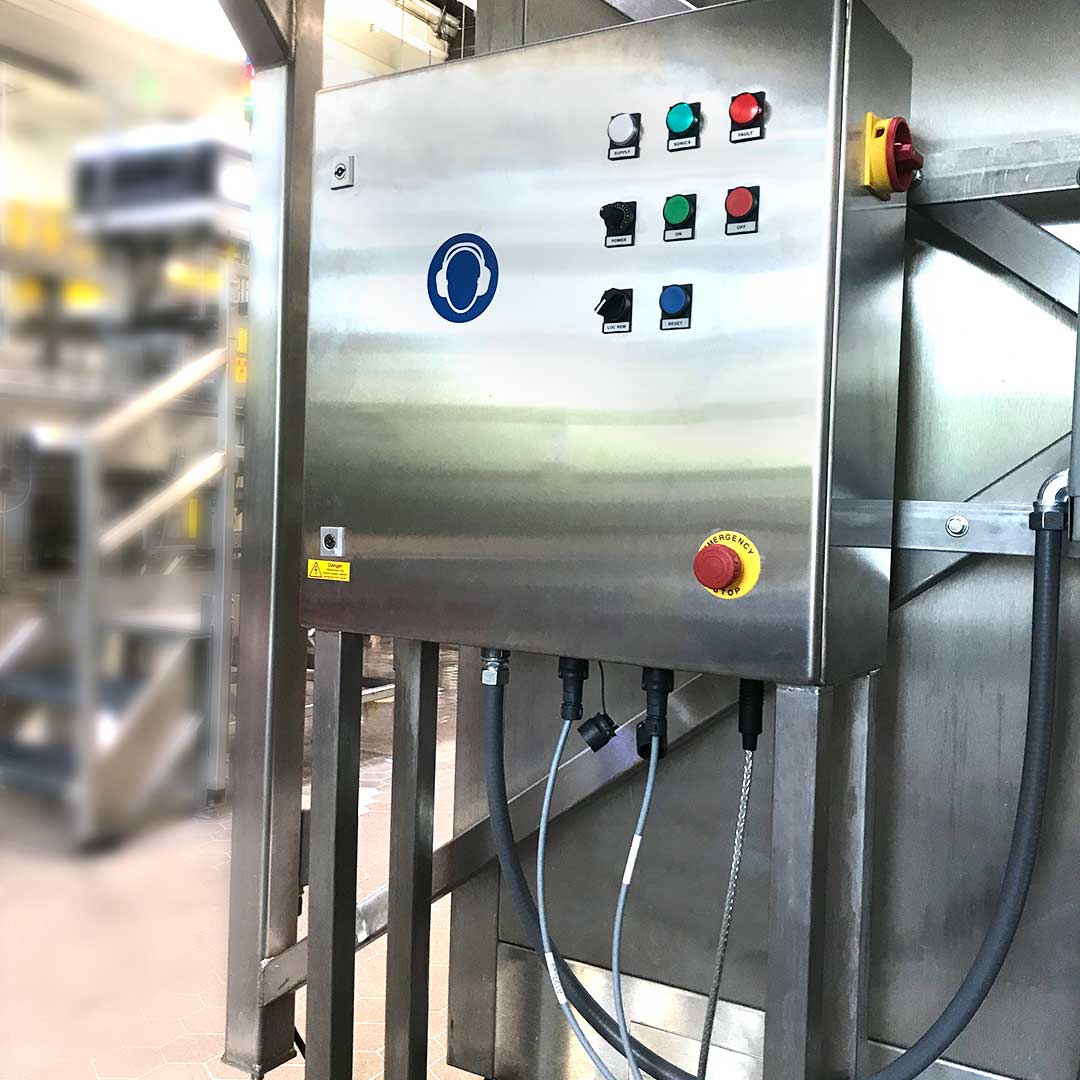
Technical Aspects and Design of Bubble-tech Models
Bubble-tech de-foamers are available in various sizes dependent upon the line speed requirements S-100, S-300 and S-500 models are notable for their low energy consumption, minimal maintenance requirements, and easy integration into existing production lines. Their hygienic and durable design further adds to their appeal, making them a preferred choice for breweries looking to improve their operations.
Performance Guarantee and Customer Assurance
Bubble-Tech partnered with JWII in Australia and New Zealand to offer a performance guarantee which backs each de-foaming unit, providing customers with assurance of the technology’s reliability and effectiveness. This guarantee reflects the company’s confidence in their product and its ability to deliver the promised results.
Client Testimonials and Industry Impact
Positive feedback from clients who have adopted this technology underscores its impact in the industry. While specific testimonials highlight individual successes, the technology’s broader impact on the beer bottling and canning industry cannot be overstated, demonstrating its potential to revolutionise standard practices.
Comparative Analysis and Broader Industry Impact
When compared to traditional methods, ultrasonic de-foaming technology stands out for its efficiency, environmental friendliness, and operational benefits. Its broader impact on the industry includes enhanced sustainability, reduced waste, and improved product quality, setting a new standard in the brewery sector.
Conclusion and Future Outlook
These case studies and client experiences discussed in this blog highlight the significant benefits and potential of ultrasonic de-foaming technology in the brewing industry. Looking ahead, the continued evolution and application of this technology promise to bring further innovations and improvements, solidifying its role as a key driver in the advancement of the brewery industry. For more information on Bubble-tech and ultrasonic de-foaming technology and how it can apply to your business please contact one of our experts.
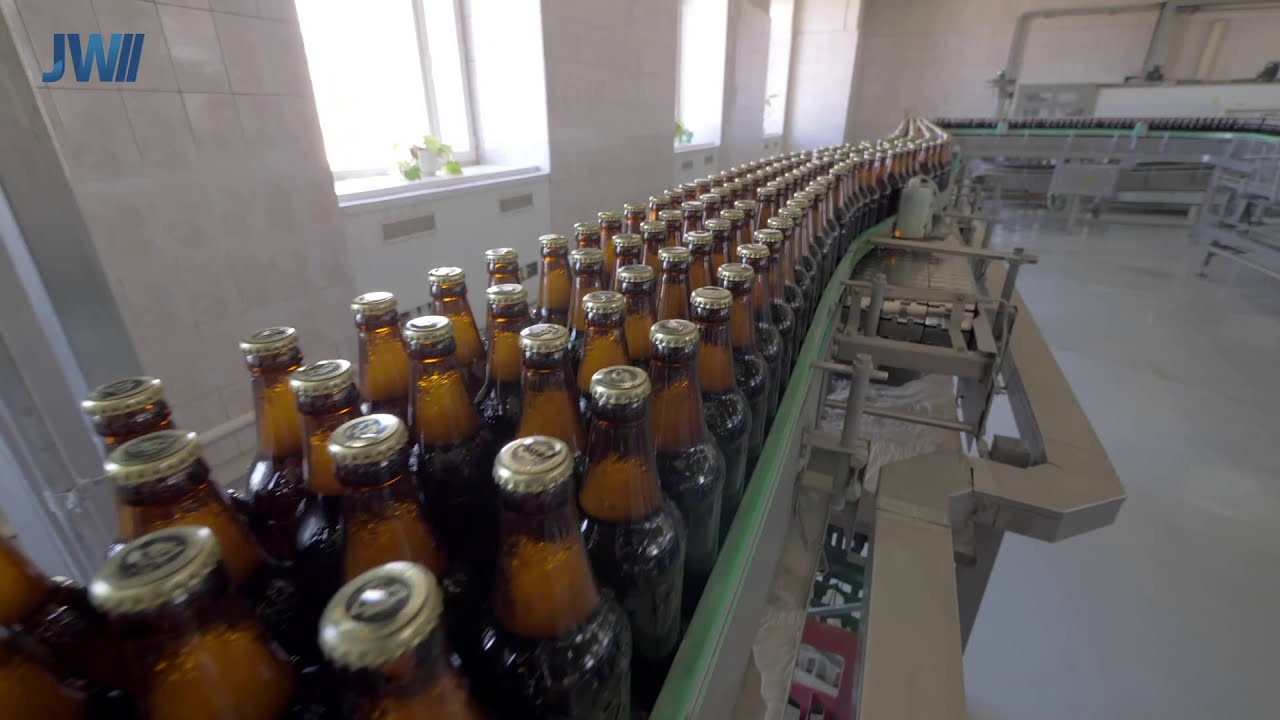