Application feasibility studies
New, modified, and problem applications often require analysis by our Applications Lab in order to determine feasibility and optimum instrument parameters. Selection of the best NIR filter combinations is often critical to the success of the measurement. In order to do this, customer samples are normally scanned on a spectrophotometer in order to produce sample spectra for wavelength analysis, and samples are prepared and measured on the appropriate analyzer.
JWII sales/service personnel and representatives often have their customers send in samples for lab analysis. Below is a case study we did recently for one large building materials manufacturer in Australia.
Moisture and Resin in MDF fiber
The MDF and the particleboard industry manufactures wood panel from wood chips, fibers and fillers. Moisture is a critical parameter as this affects the final board and also the bonding properties of the board. Too much moisture can cause blown boards (Delamination) in the press. Resin and wax are often used as binders.
Case study on customer samples
We were provided with an excellent opportunity to perform a detailed study for the measure of Moisture and Resin in MDF fiber. We were supplied with a total of 15 resin impregnated fiber samples. With these samples we are able to select filter algorithms for both moisture and resin in these types of product.
Moisture samples in MDF Fiber
Moisture samples were conditioned over the range 2-8.5% which is wider than normally seen in production.
Material: MDF Fibre
Meaurement: Moisture
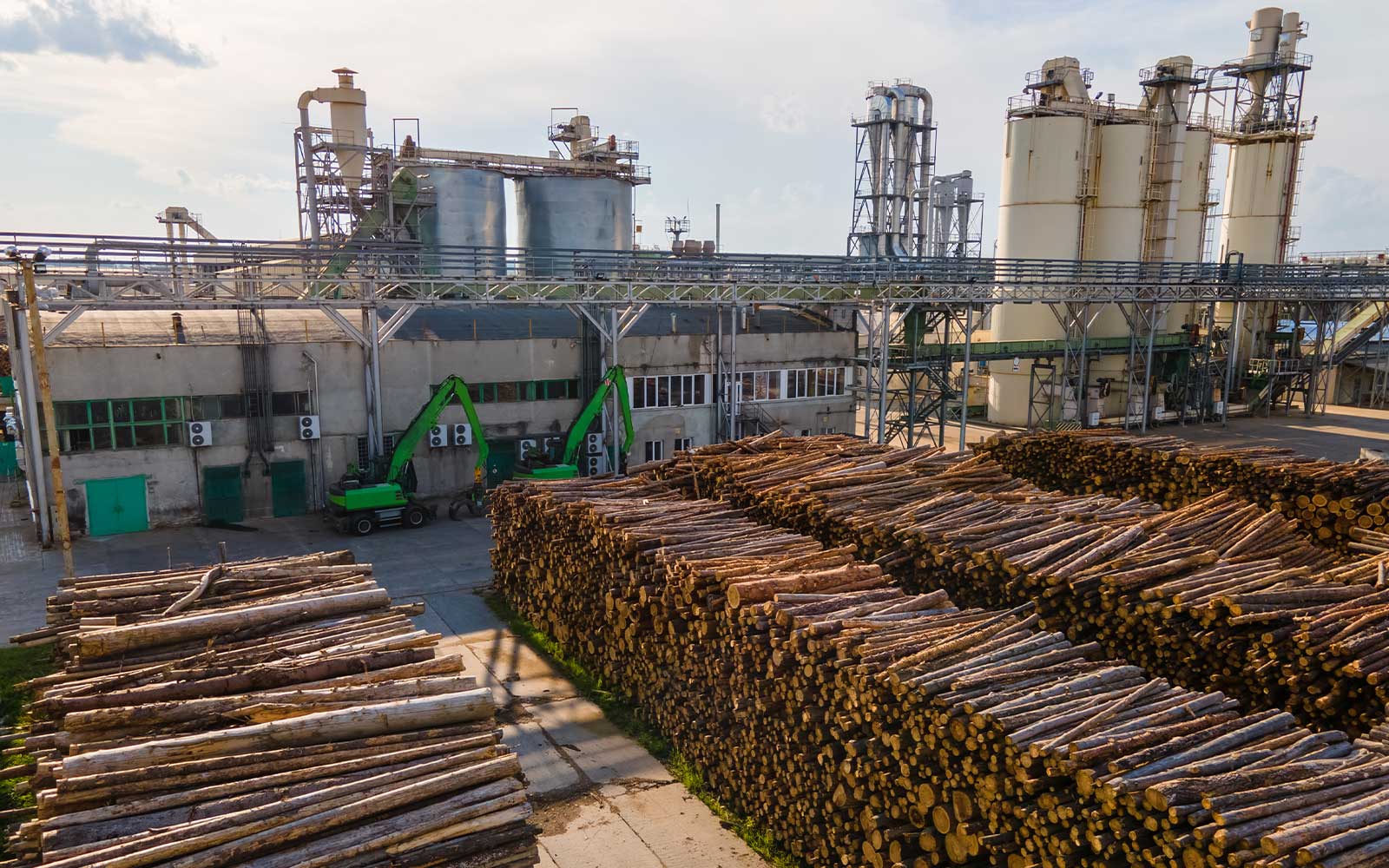
Moisture Results
Sample Number | % Moisture (Lab) | Moisttech NIR % Mositure |
---|---|---|
1 | 2.5 | 2.5 |
2 | 2.7 | 2.6 |
3 | 3.1 | 3.1 |
4 | 3.9 | 3.9 |
5 | 4.2 | 4.1 |
6 | 4.9 | 4.9 |
7 | 5.2 | 5.2 |
8 | 5.8 | 5.9 |
9 | 6.3 | 6.3 |
10 | 6.9 | 6.9 |
11 | 7.1 | 7.2 |
12 | 7.5 | 7.5 |
13 | 7.9 | 7.9 |
14 | 8.1 | 8.1 |
15 | 8.5 | 8.6 |
Resin samples in MDF fiber
Resin samples consisted of resin content from 8.5 to 19.2 percent again a wider range than normally seen in production. Also, the resin contents were accurately determined by nitrogen analysis by the customer.
We obtained an excellent correlation between our values and the customer’s resin content values.
Material: MDF Fibre
Measurement: Resin %
Sample Number | % Resin (Lab) | Moisttech NIR % Resin |
---|---|---|
1 | 8.5 | 8.9 |
2 | 8.8 | 9,1 |
3 | 9.7 | 9.4 |
4 | 10.1 | 9.9 |
5 | 10.7 | 10.1 |
6 | 11.3 | 11.3 |
7 | 12 | 11.7 |
8 | 12.4 | 12 |
9 | 13 | 13.5 |
10 | 14.3 | 14.8 |
11 | 15.3 | 15.6 |
12 | 16.3 | 16.5 |
13 | 17.9 | 18.1 |
14 | 18.3 | 18.5 |
15 | 19.2 | 19 |
Next steps to test the analyser in the plant
The results above were very encouraging so we then pre-calibrated an IR3000 gauge based on the above results and arranged to install it on the customers line.
Selecting the analyser location
The MDF fiber comes from a cyclone dryer and over a weight belt and although this is an ideal location for dryer control the resin is not added at this point. It was however marked as a good potential location for a moisture only sensor in the future. After the weighbelt the fiber falls and resin is applied, it then drops onto the forming line.
We decided the most suitable location for the MoistTech IR3000 was on the MDF forming line just after the resin addition. We located the sensor just after the scalper which is a rotating blade that forms the MDF mat into a uniform height before going into the continuous press. See picture below of a typical installation.
Analyser mounting and installation
A representative from our service department assisted the customer to install the unit on line during a shutdown. The Mechanical installation of the MoistTech IR3000 gauge is simple as it has 2 mounting brackets included. These brackets accept a 32mm diameter pipe so fabricating a small frame was straightforward. We then connected the power and analog outputs 4-20mA and an Ethernet connection to the gauge. These were all via the ports on the rear of the sensor with the connectors supplied with the gauge. We also installed a filter regulator with 5psi of air to the air purge tube on the gauge lens just to keep it positively purged and avoid any dust build up on the gauge measurement window. Gauge is a non contact technology so we mounted the sensor 200mm from the surface of the product.
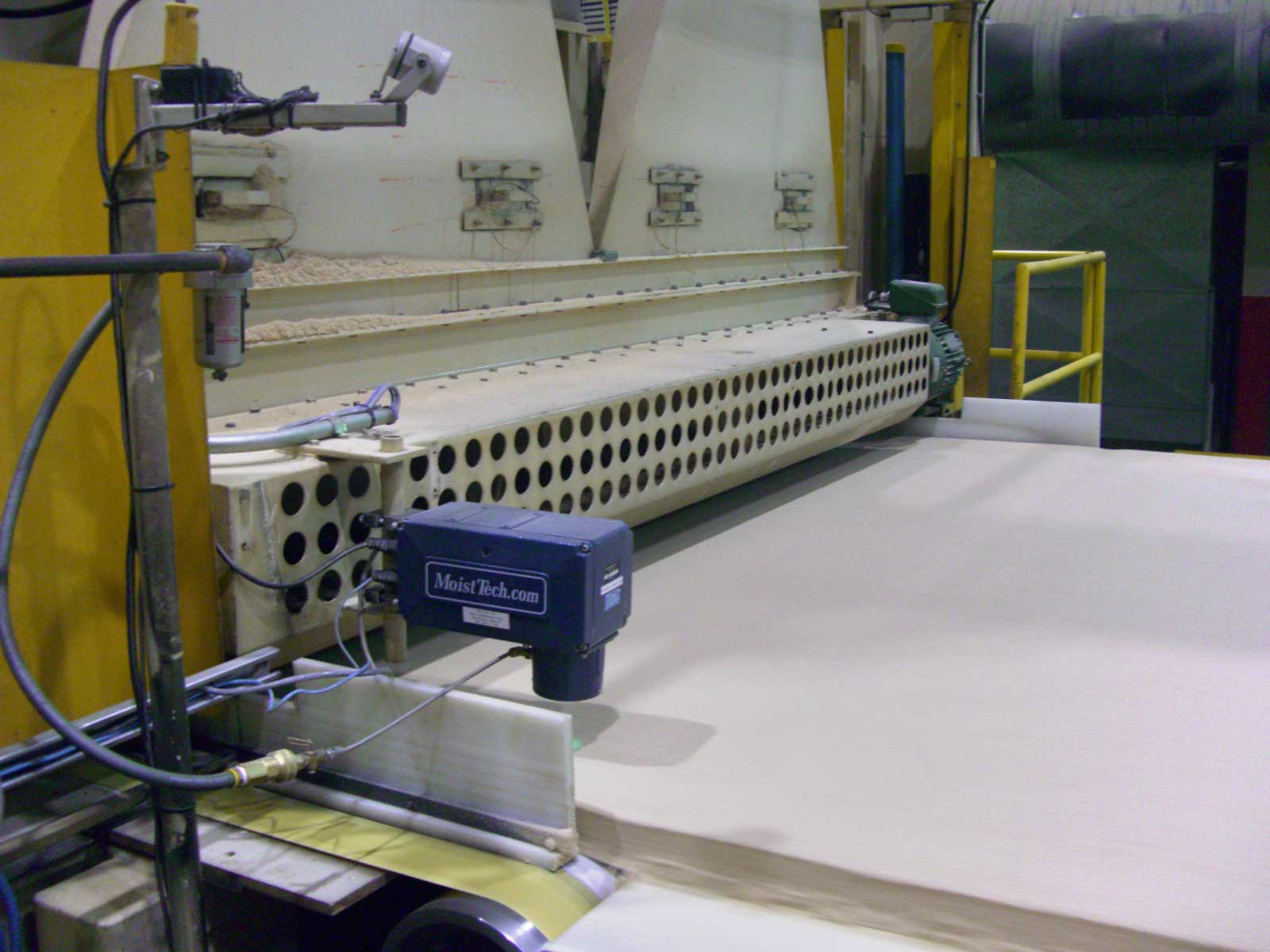
Signal connectivity
Output signals were connected to the plant DCS, in this case we used 4-20mA, the gauge does have the option to add Profibus, Profinet, Devicenet and Ethernet IP later but in this case it was not needed.
We then connected the Ethernet cable to a laptop which is running the configuration software which is provided free of charge with the gauge. This allows configuration, calibration and data logging of the gauge reading.
On site factory test
They system was left on site for a period of 2 weeks where data was collected and compared to the existing laboratory methods and the results achieved were comparable to what we found in the applications lab.
Return on investment
Customers concluded with these types of results there would be significant savings in terms of quality and yield. Moisture control and the reduction of delamination and blown boards, resin savings as it is an expensive part of the process controlling the addition more accurately has major benefits.
Key benefits
Process line benefits with the MoistTech IR3000 for moisture and resin control are clear. The ability to minimize costs and increase efficiency in the plant is easily achieved. With today’s lean manufacturing initiatives this is a key way to make process and quality improvements in building material manufacture.
- Reduction in blown boards and delamination
- Reduction in Board Fires / Explosions Due to Dust
- Increased Product Quality
- Lowered Energy Costs from Proper Dryer Control
- Reduced Start-up Times
- Less Waste & Downtime
- 100% Product Inspection
- Significant Resin Cost Savings
JWII staff is experienced with the building materials industry and have a range of analysers for various MDF applications. If you have interest in this application or have other requirements for analysers in your plant please feel free to contact us and we would be more than happy to help.