What is representative sampling?
How about manual sampling?
A manual scoop or bucket sample just give the user an insight into the process at one particular point. So this would be called a grab sample and depending on the process conditions a grab sample may not be suitable due to segregation or separation. There are also dangers around taking a manual grab sample from the process, especially of the material is moving or in an open vessel for example. We often come across customers running their entire process from small grab samples taken using a tin cup or scoop. This can lead to mis information on what is actually happening in the process and also cause the loss of yield due to over drying or mixing issues. There is also an environmental hazard with manual sampling especially for powders or chemicals that can be exposed to the atmosphere, or create dust and fumes.
How does composite sampling work?
What are the types of automatic sampler I can use?
The common types of sampler come in 3 forms. A spot sampler which enters the process extend to a spot in the stream (typically at 10%) and sample from that spot. This would be the least representative of automatic sampler unless the product is homogenous, but in some non homogenous processes it is the only way available. The next type of sampler would be a Strip sampler, these types of samplers either stroke into the process (60% into the stream) and remove a strip as it retracts. By capturing a strip across the entire width of the stream of material it captures a far more representative sample. The 3rd sampler type and the ultimate would be a full cross cut sampler, this type of sampler will stroke across the entire stream and capture a full 100% cut of the process stream. The cross cut sampler can also be configured to take a composite over time building a profile of the entire production.
Which sampler types should be used in which location?
The selection of which sampler you can use in your process will be very dependent on the location you would like to take a sample and also the material to be sampled. We can assist you with this selection of course but to give you an idea. Typically liquid and slurry samples are homogenous so a spot or strip sample is sufficient in these types of material, normally a spot sampler like the Sentry Isolok is a good choice for this type of application. Powders in pneumatic conveyors are not homogenous but its also difficult to fit a full cross cut sampler in these locations, so then a strip sampler would be used like the Sentry model RX. If the material is in a gravity chute or exiting a hopper and is free falling, this would be ideal for a full cross cut sampler like the Sentry model SA. Conveyor belts are also an area of interest and samplers are typically fitted in the head chute of the conveyor where the material is falling for the best accuracy.
What are the benefits of representative sampling?
It is very important to have the right type of sampler in the right location to give you a representative idea of your process. This will provide you with reliable and accurate analysis results, will help you save money by reducing waste and downtime, protect your operators and the environment, and ensure product quality and regulatory compliance. You can also get yield improvements and process optimisation which all add to savings.
How do I control an automatic sampler?
Where can I get more information on the samplers offered by JWII?
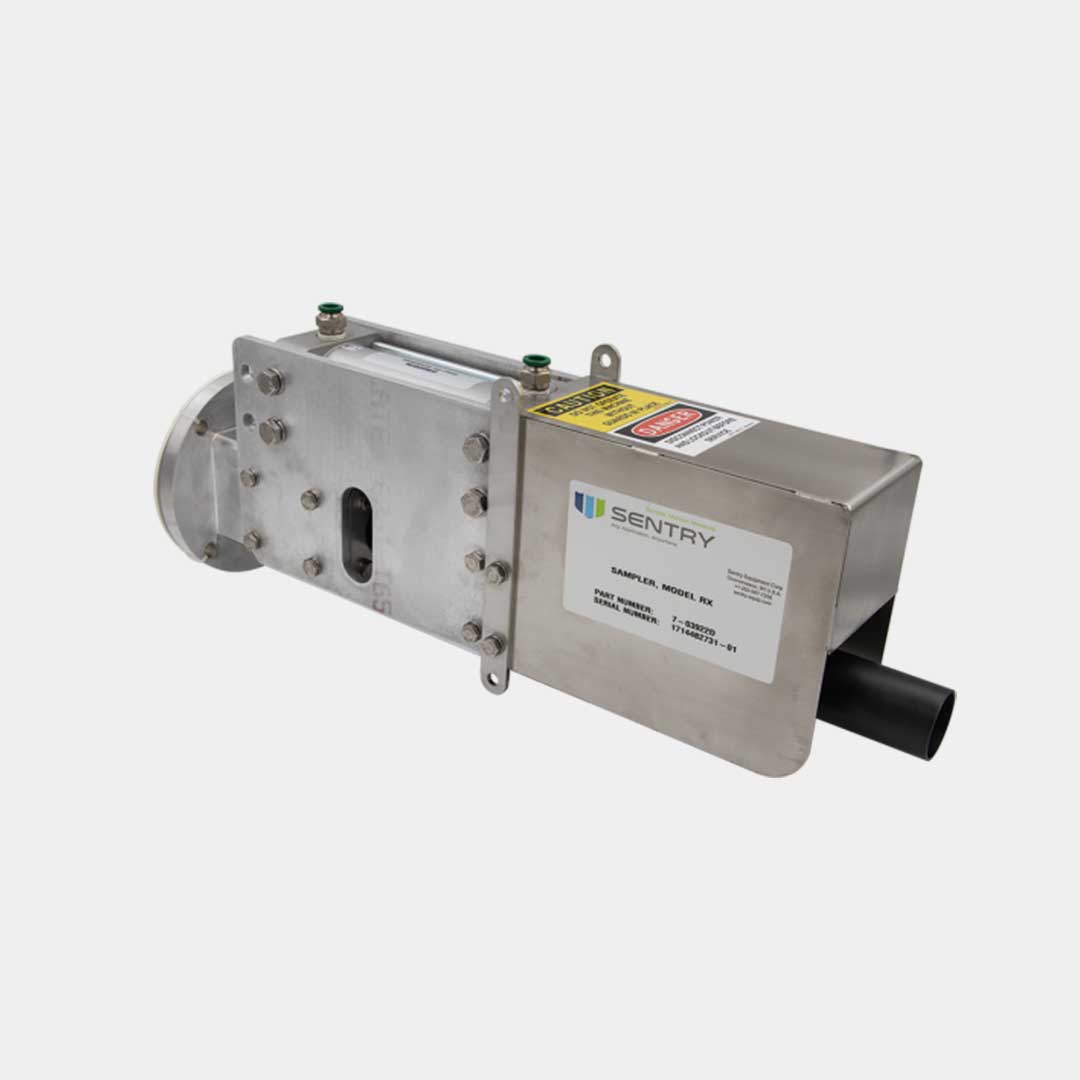
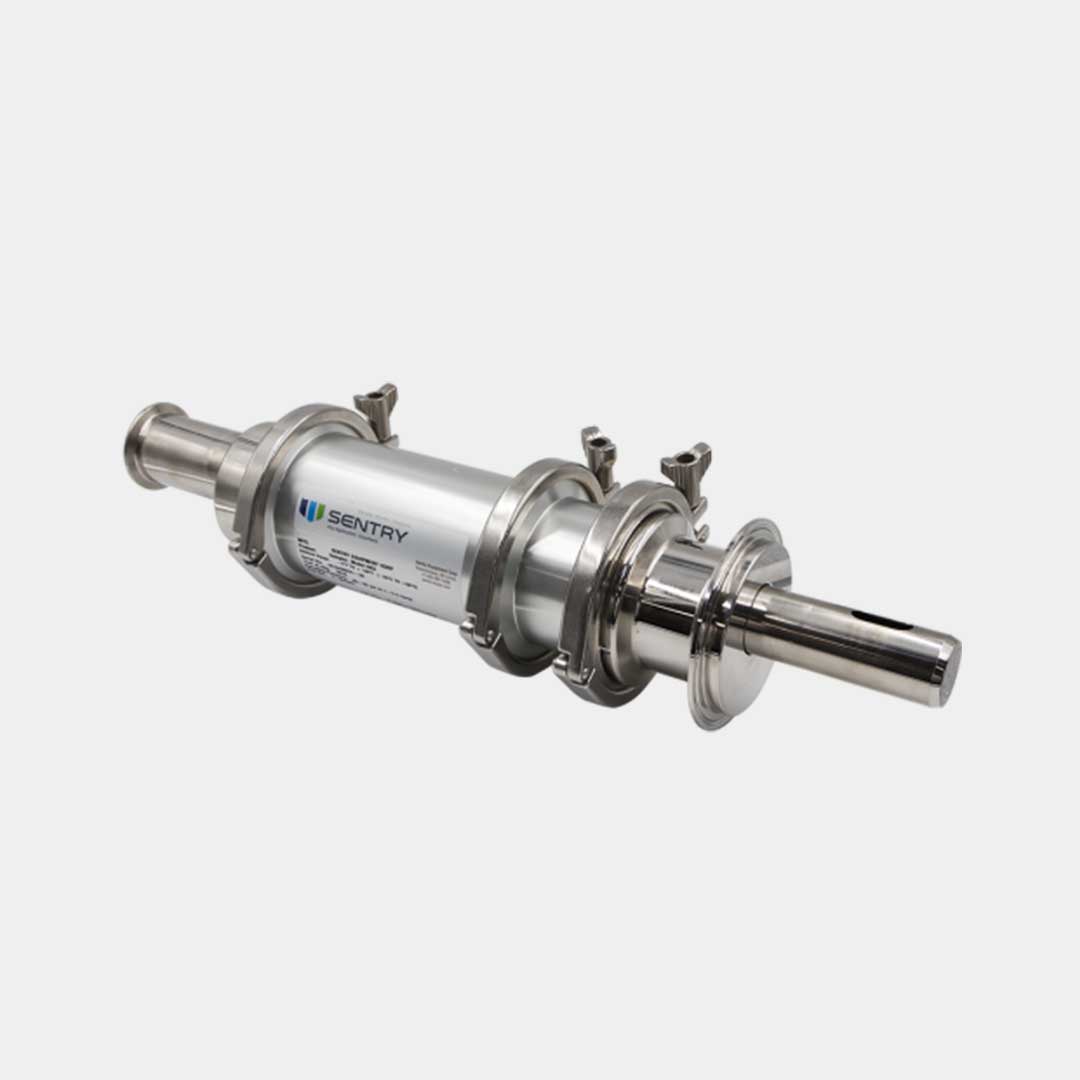
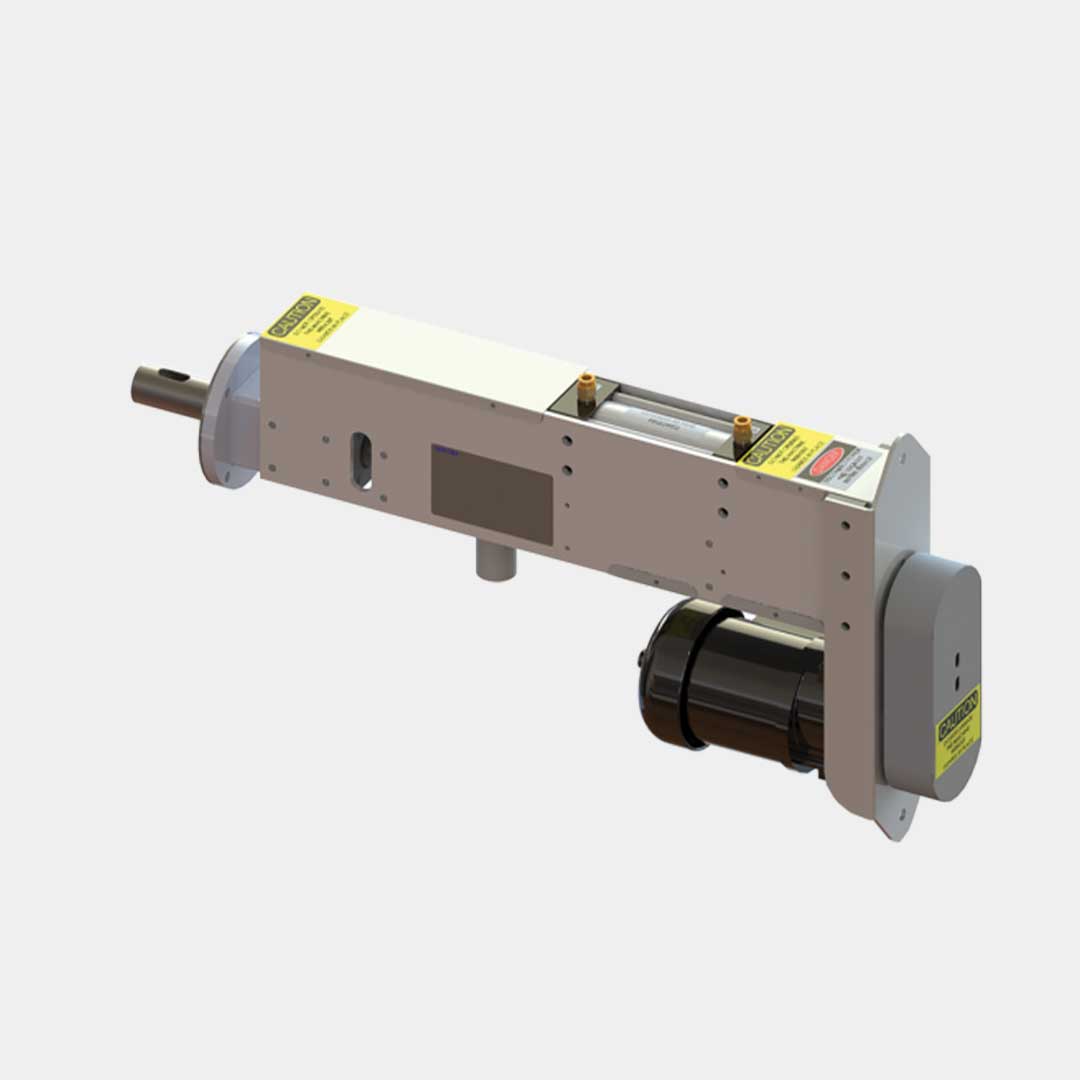