Bulk Material Sampling Systems
With over 40 years of expertise, JWII offers top-tier sampling systems including the Bucket Sampler, Cross Belt Sampler, and Cross Stream Sampler. Our solutions ensure precise and durable sampling for various industrial needs. We provide custom-made solutions for a wide range of applications.
Representative Sampling of Bulk Materials from Falling Streams and Conveyor Belts
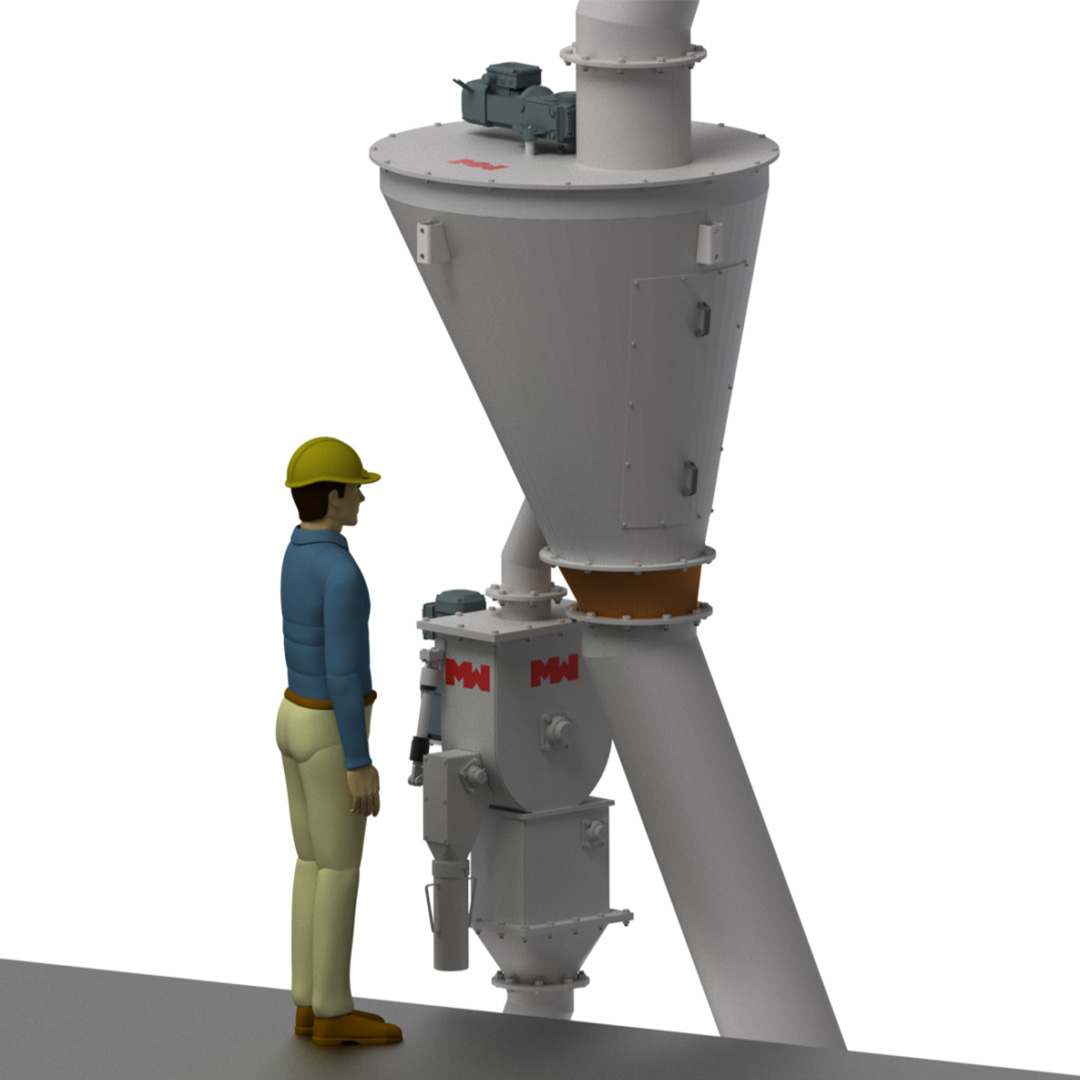
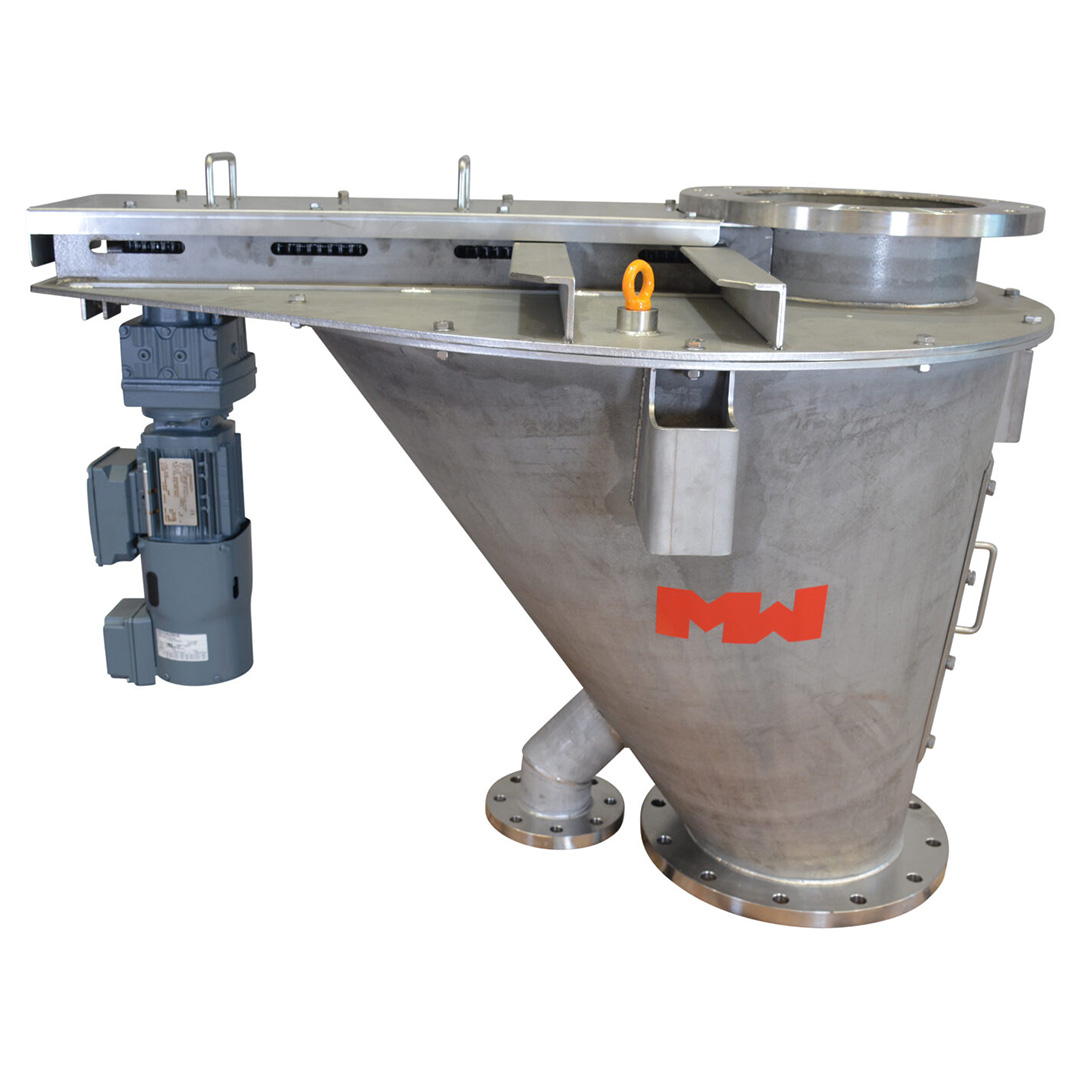
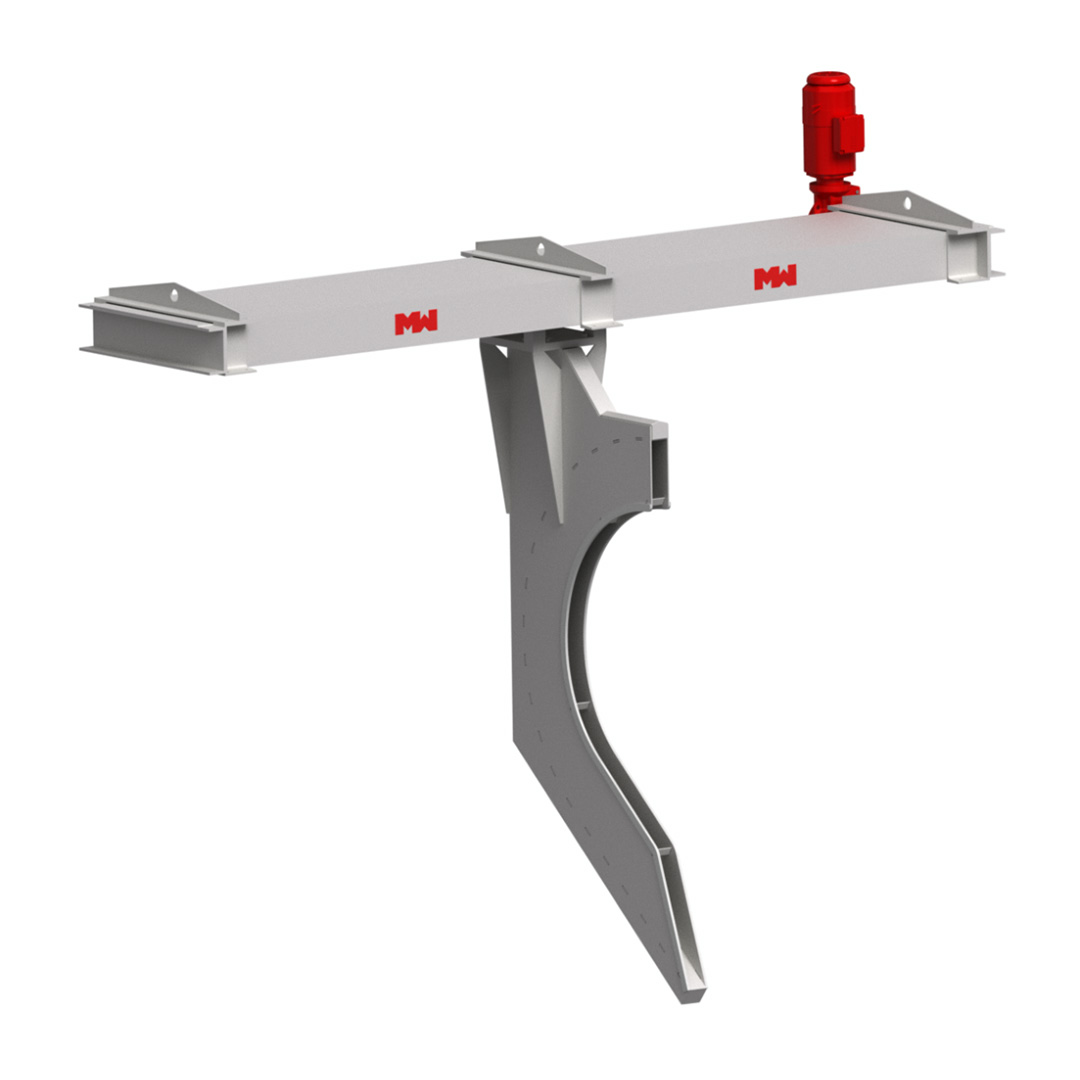
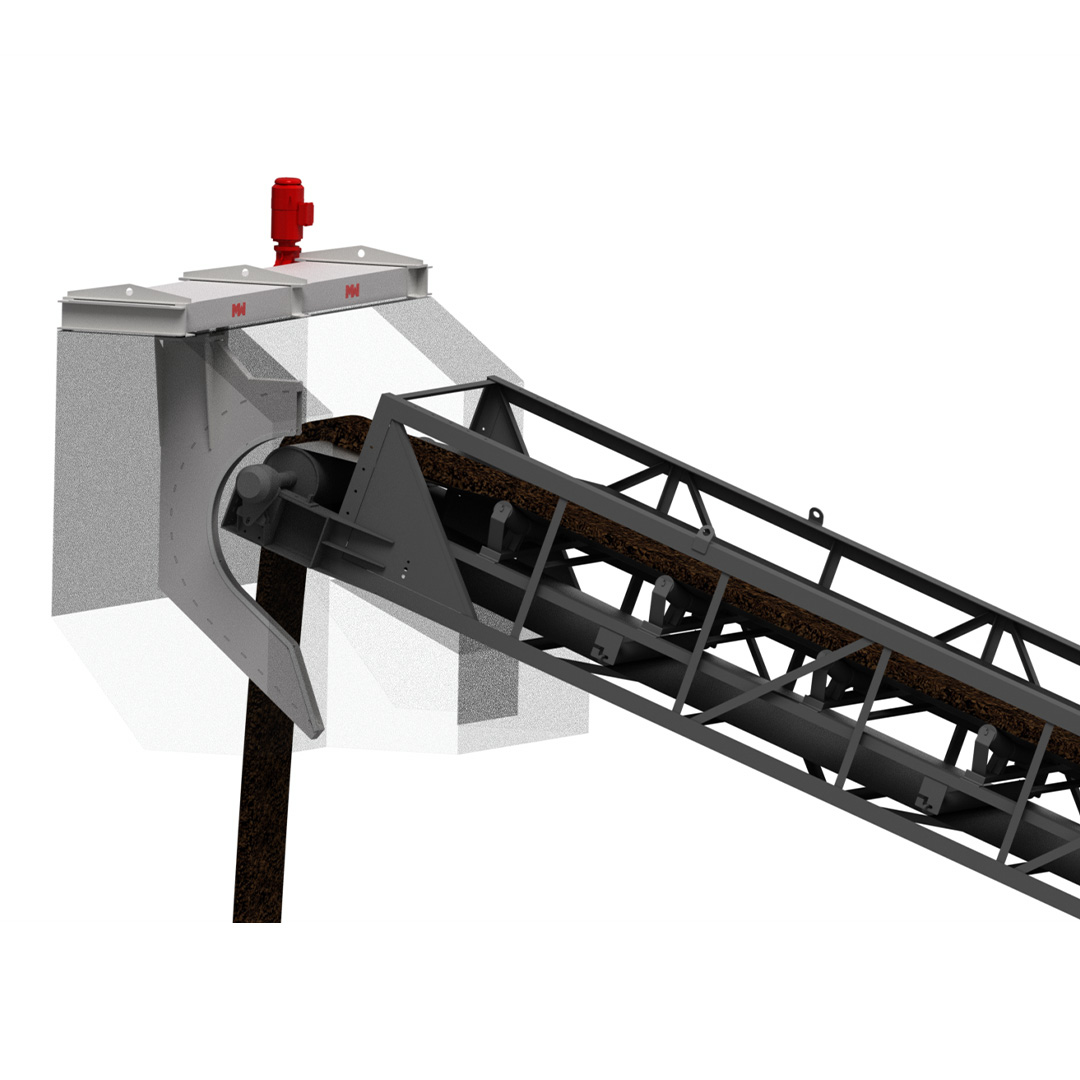
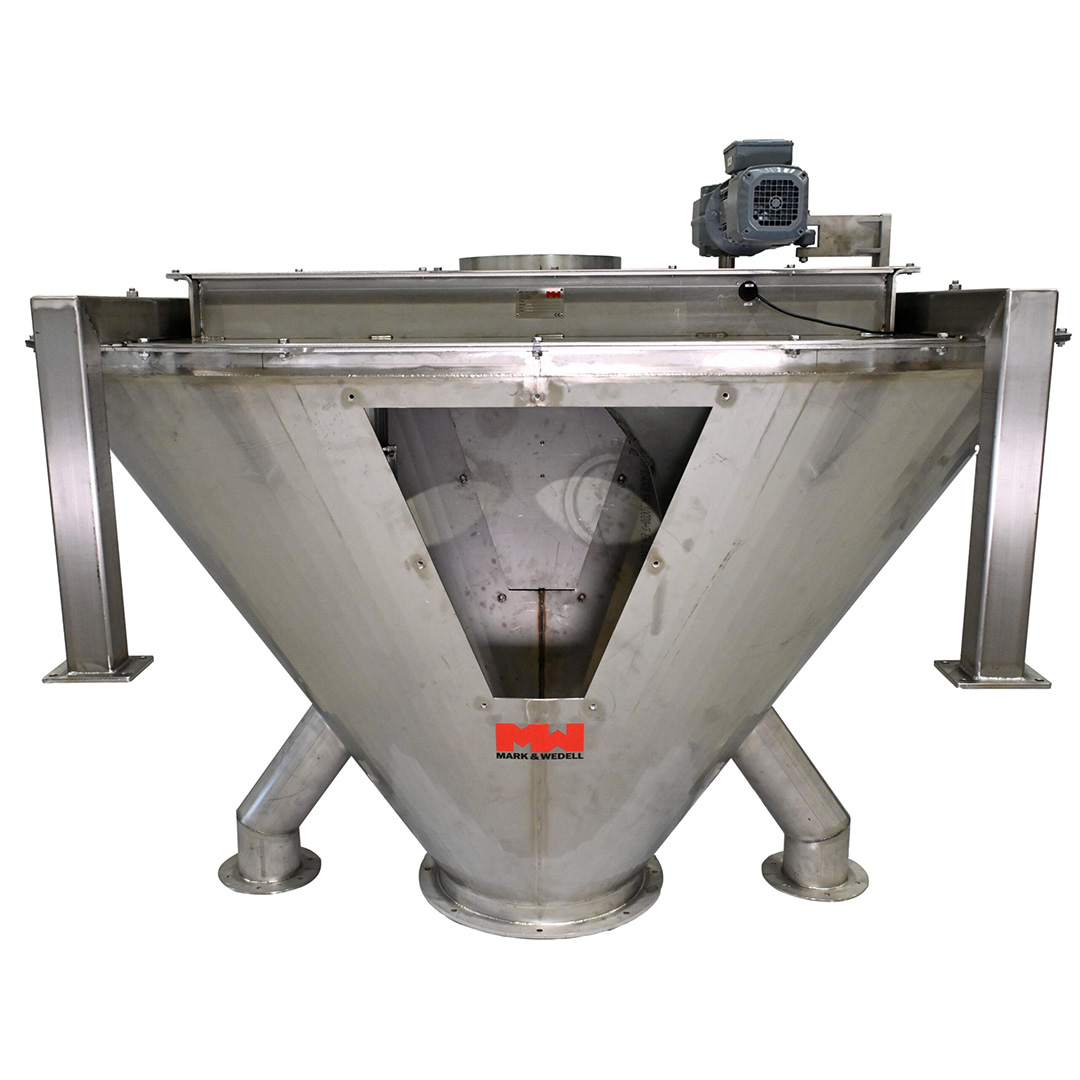
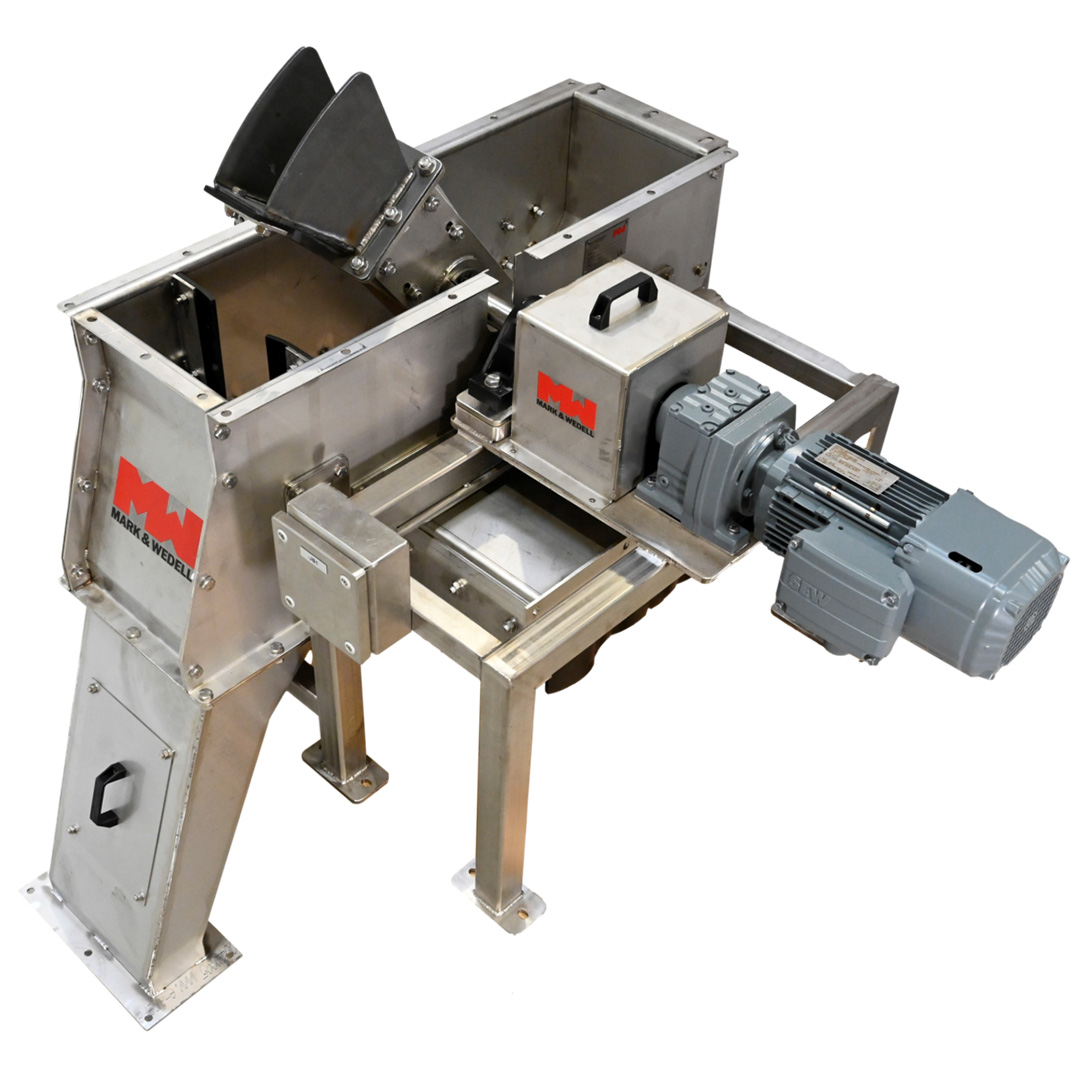
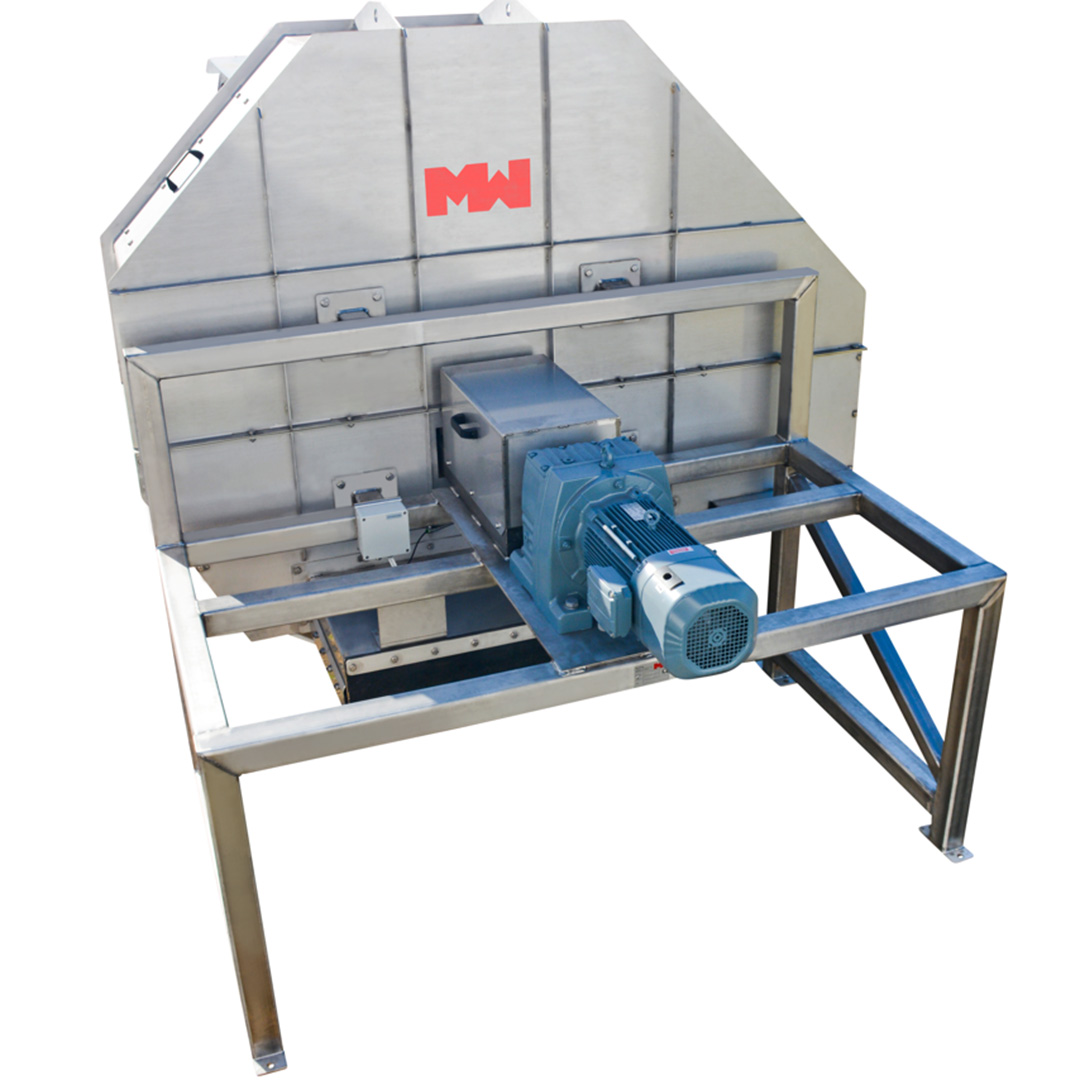
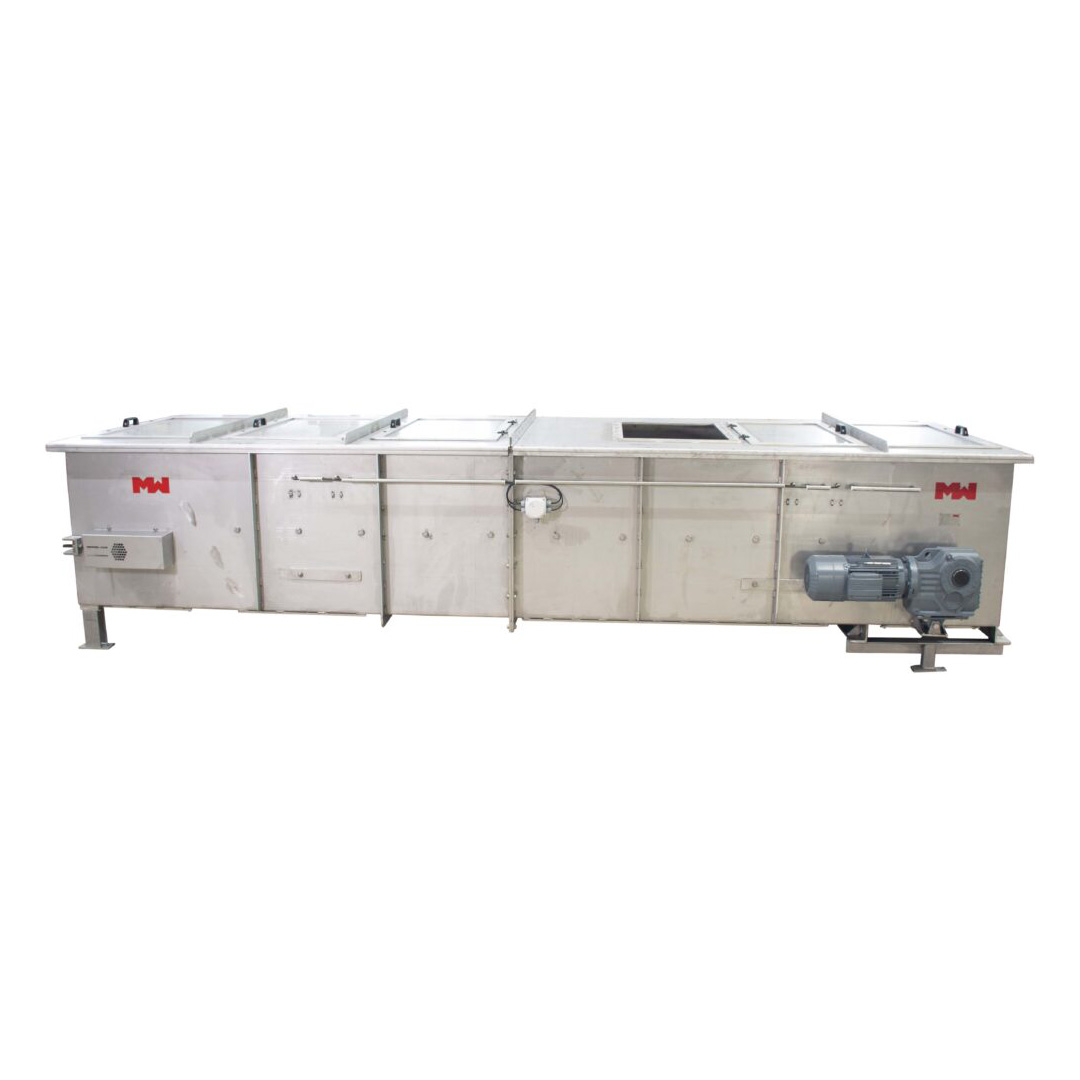
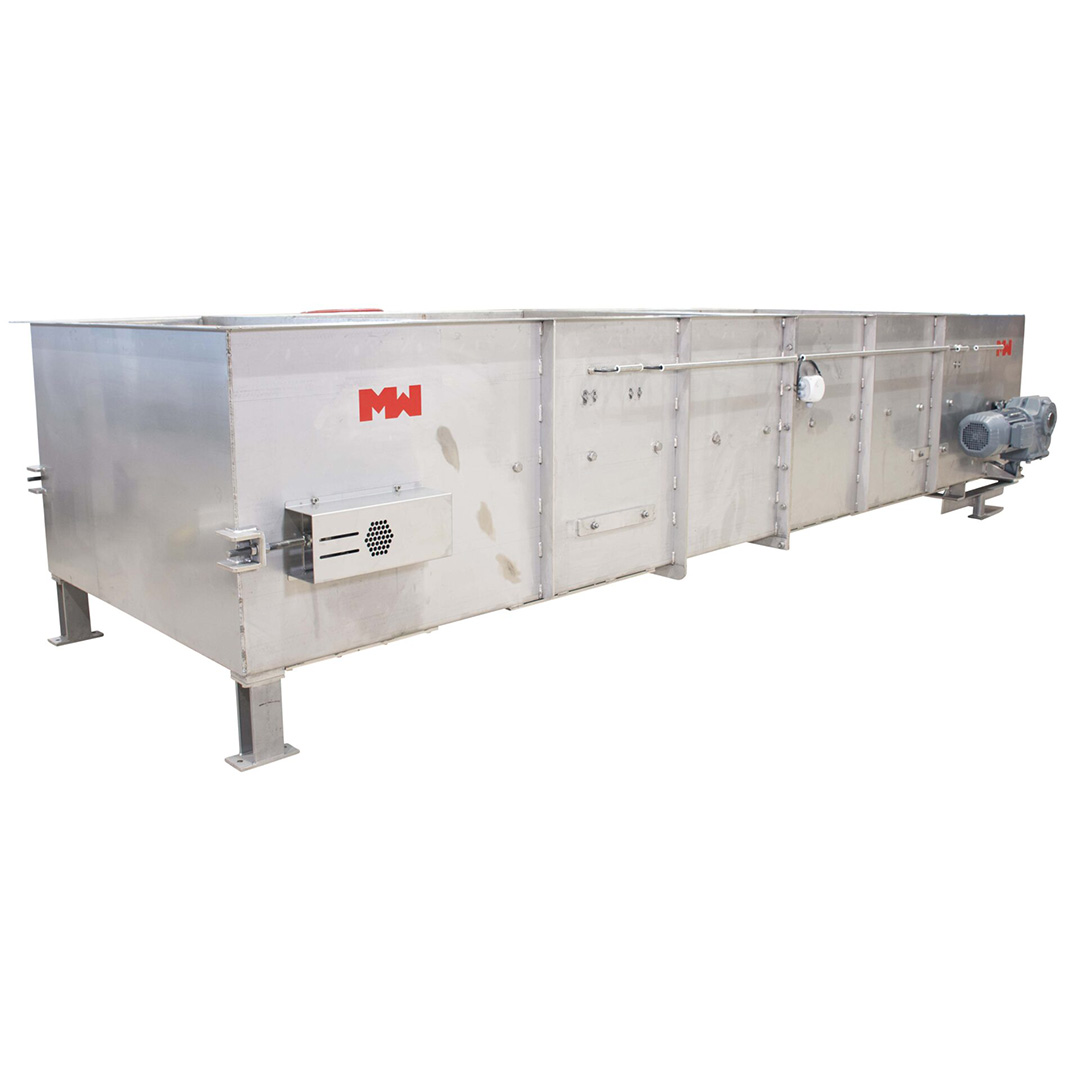
4 Decades of experience
JWII has over 40 years of experience supplying high-quality bulk material sampling systems to a wide range of industries. Our expertise ensures that our customers receive the most reliable, efficient, and accurate sampling solutions available. Our comprehensive range of automated sampling solutions are custom made and designed according to the requirements of the specific application. Sampling of bulk materials is a comprehensive process, and we endeavour to provide the more representative sample based on the material flow. If the sample you are analysing in your laboratory is not representative of your process then this compromises the accuracy of the analysis itself. Whether you need solutions for falling streams or conveyor belts, JWII and our bulk material sampling partner M&W has the experience and technology to meet your needs.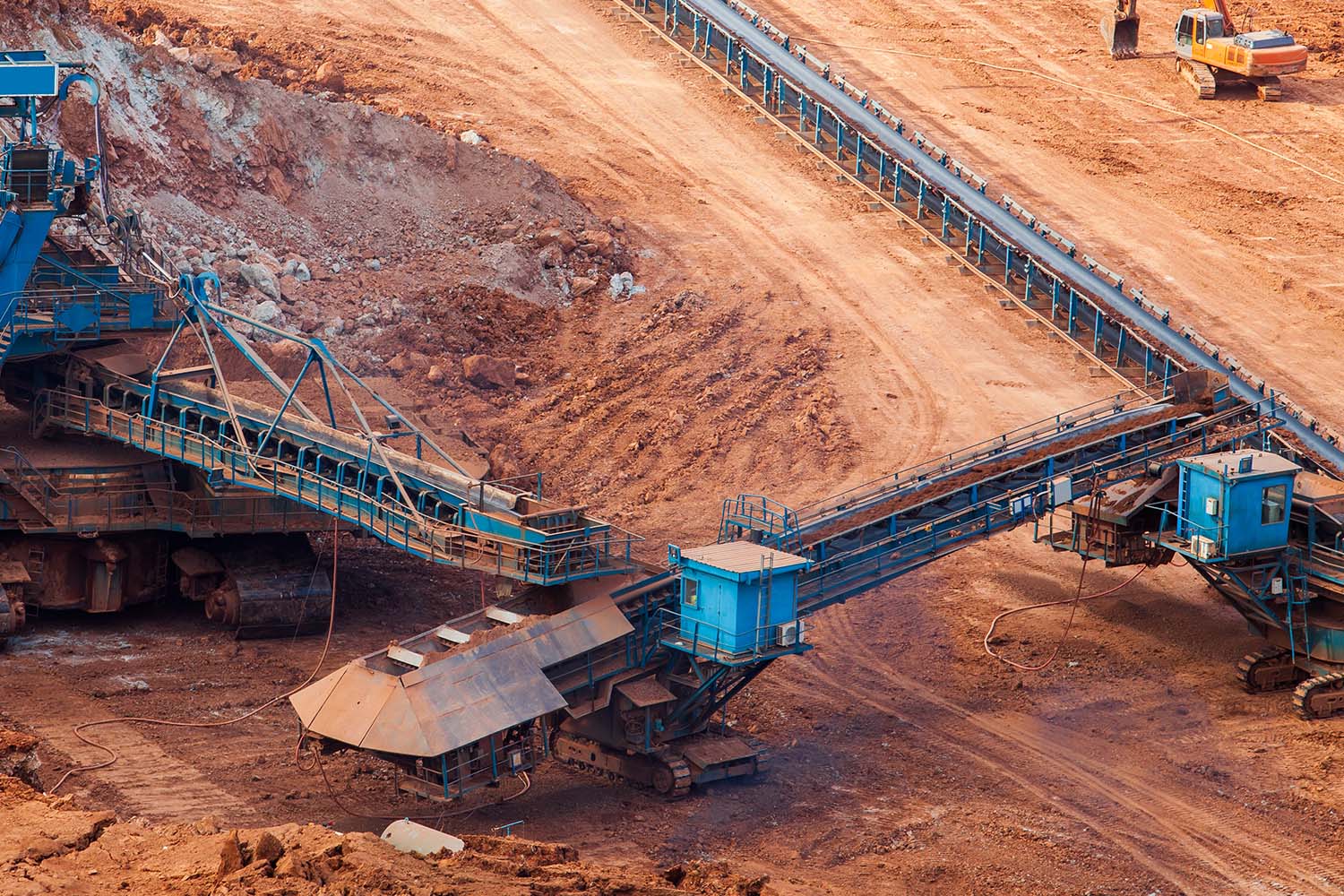
Representative Sampling of Bulk Materials in a Falling Stream
Materials with a high content of dust, the Bucket Sampler is one of our recommended technologies. Bucket sampling consists of a cutter moving though a falling stream of material which provides the most representative type of sample as the complete stream is captured. The issue here is the quantity of the initial cut may be too large and this is where careful and concise secondary sampling techniques come into play. Let us explain in more detail.
Bucket Sampler
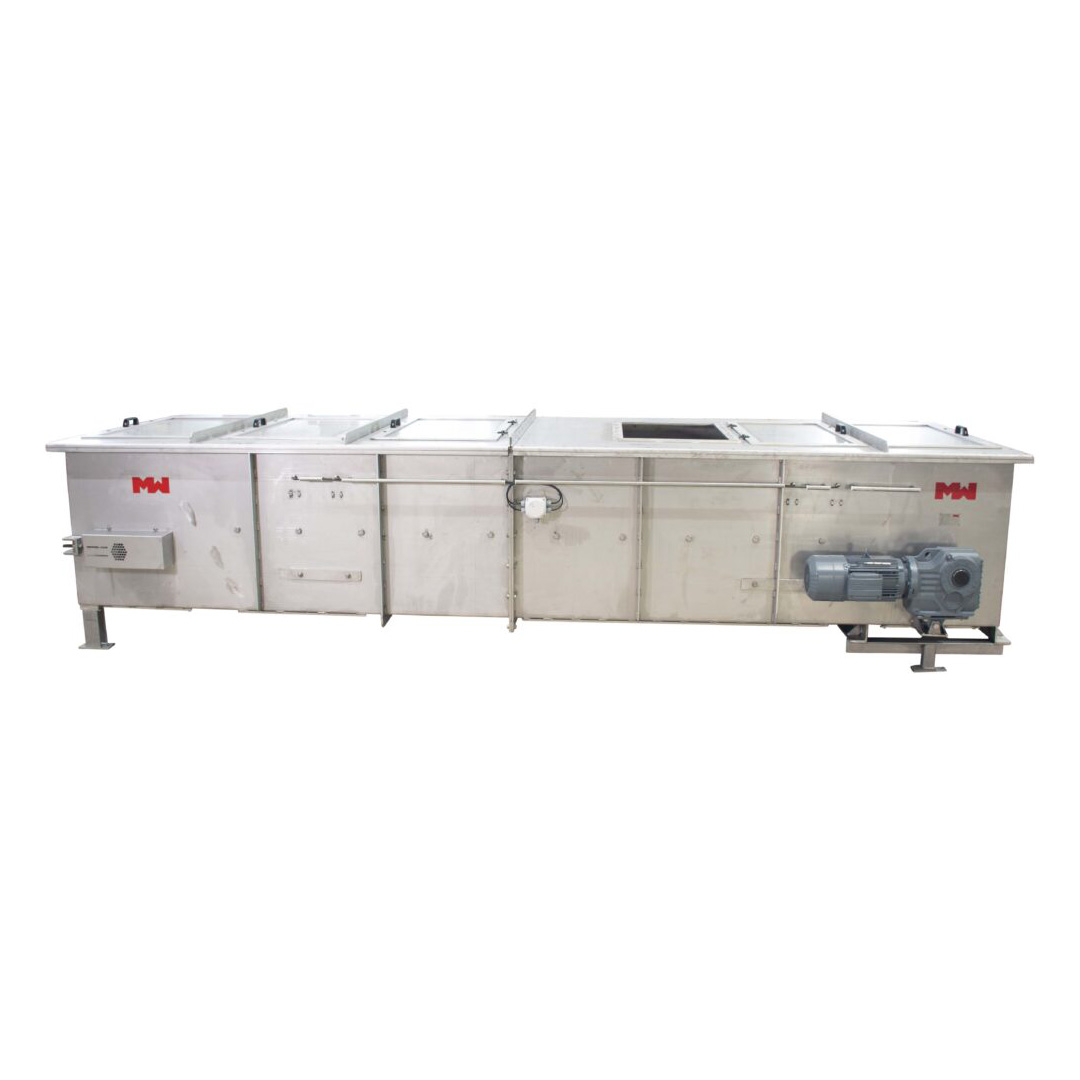
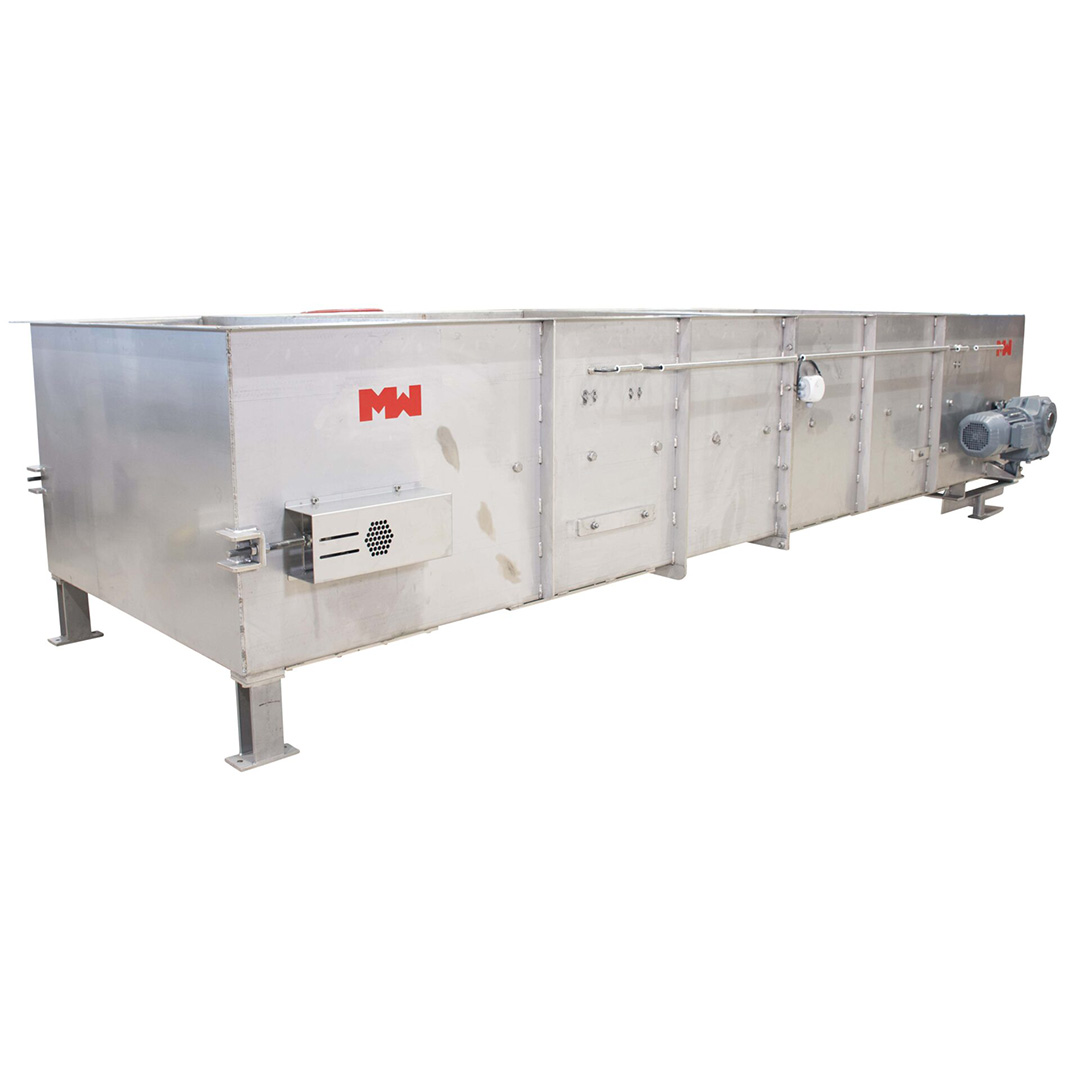
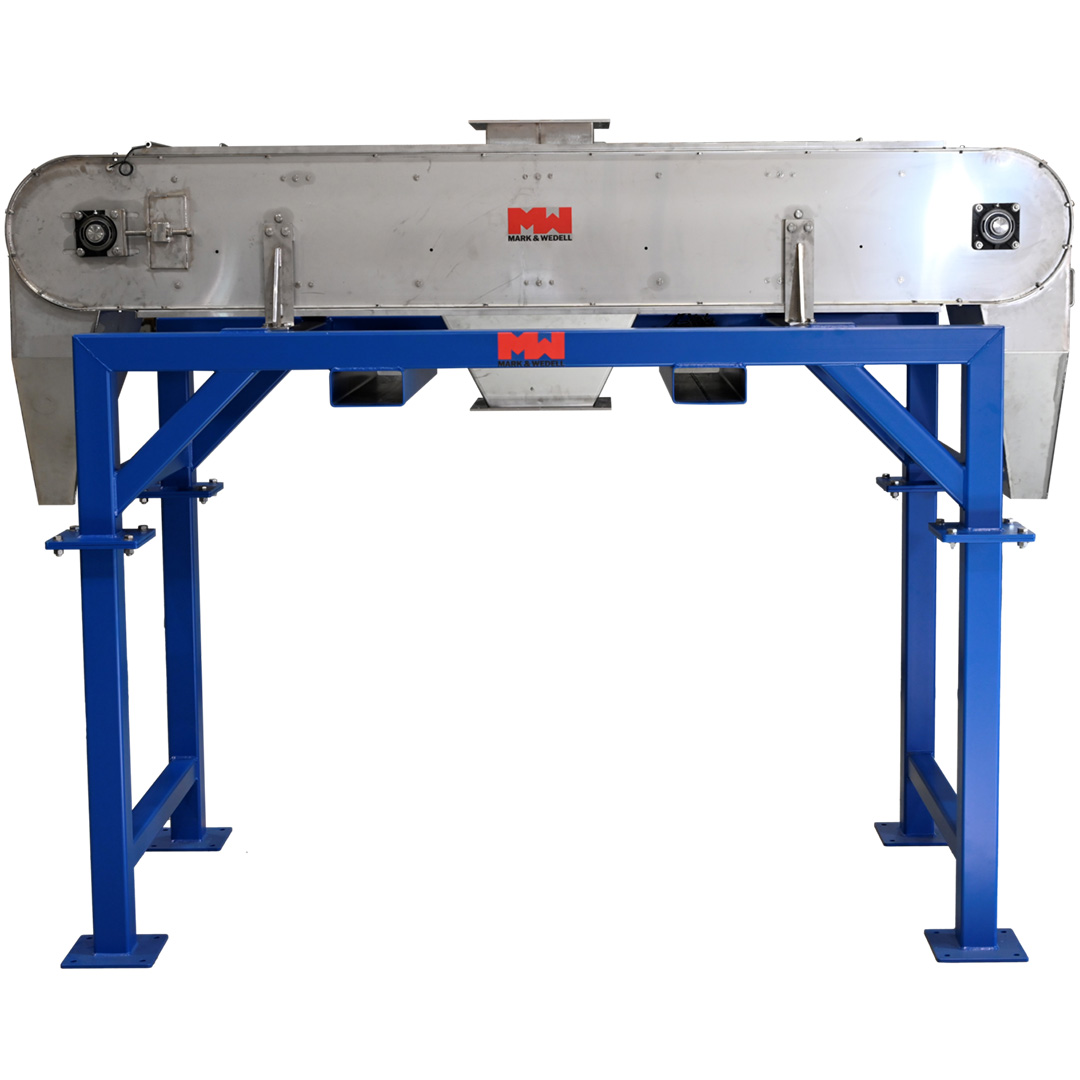
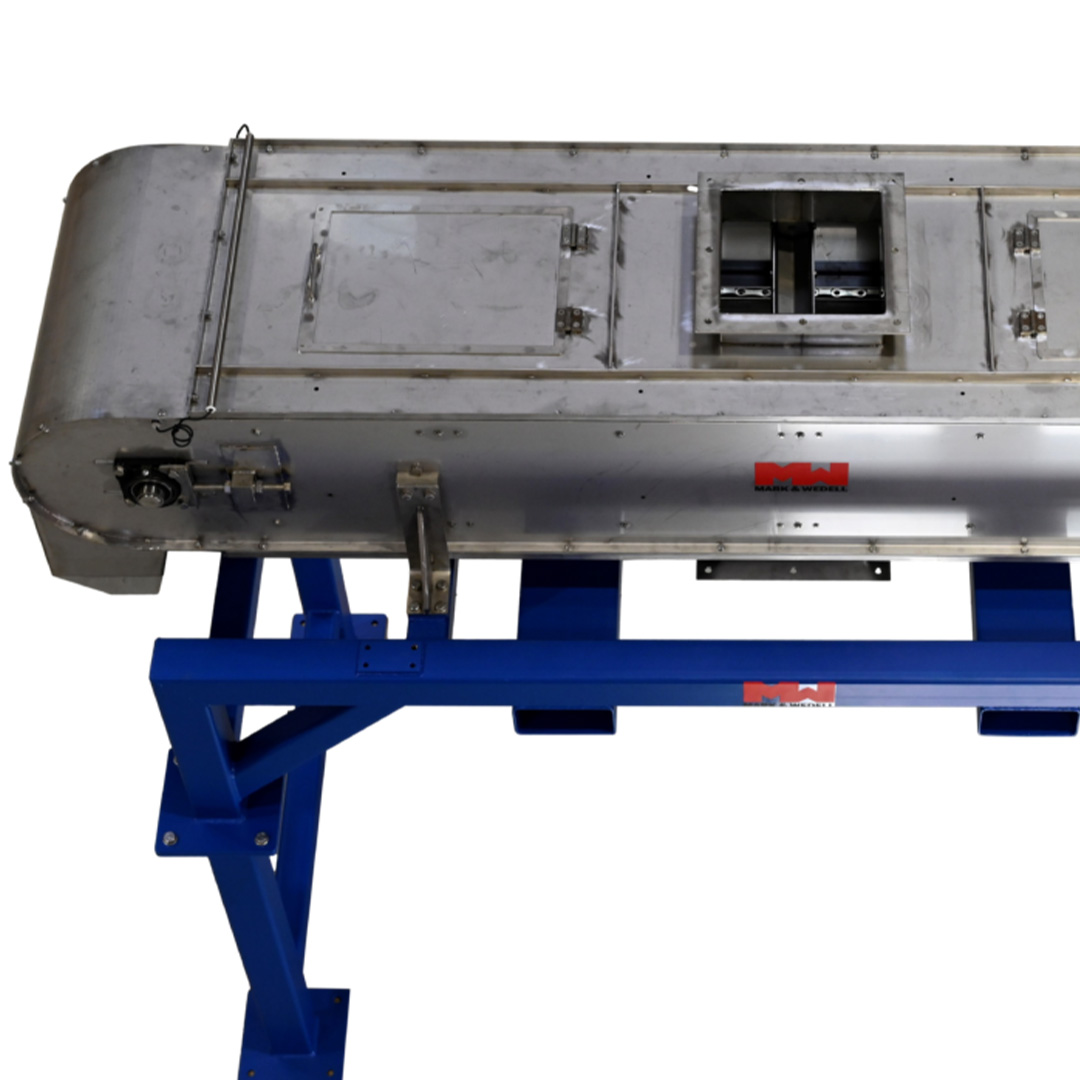
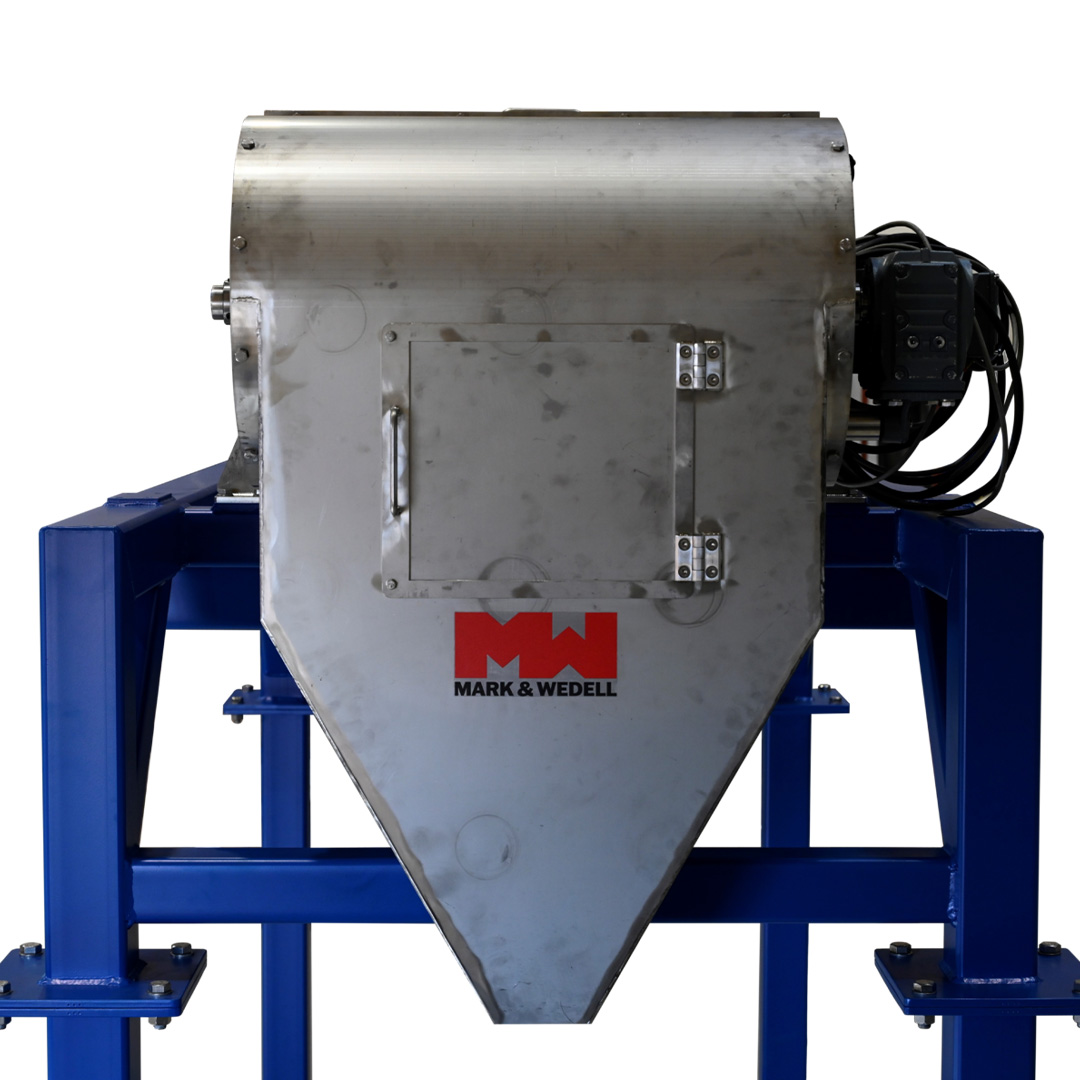
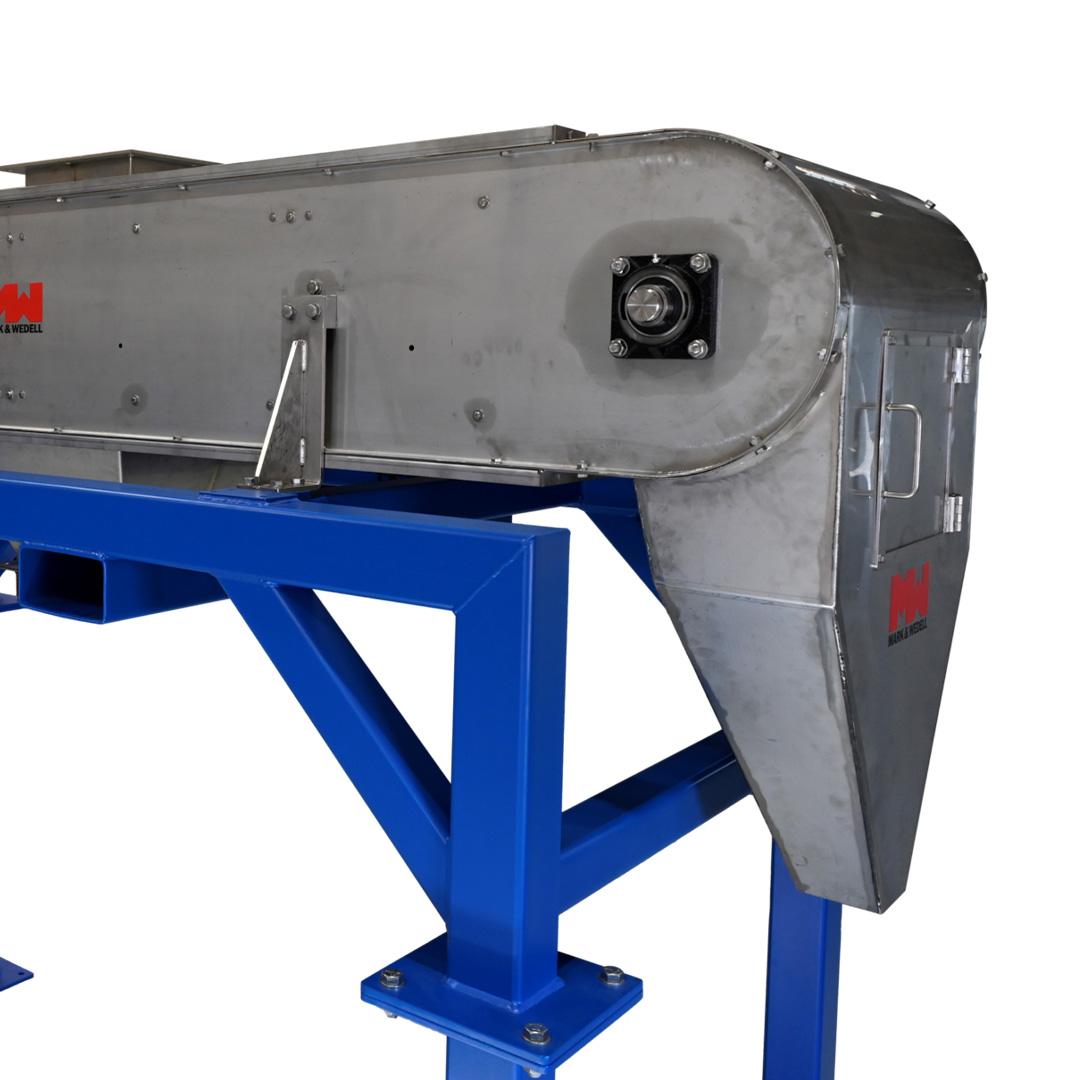
The Bucket Sampler (BS) is designed to extract increments/cuts from a free-falling flow of bulk material in a vertical duct. Representativity is ensured since a complete cross section of the material is collected. The sampling outlet of the BS is connected to a Screw Conveyor by a chute and further refined in a representative way to provide the end user with a representative sample in the quantity they can handle in the laboratoory. The steps in the sampling process can be seen in the diagram fig.1 as outlined below
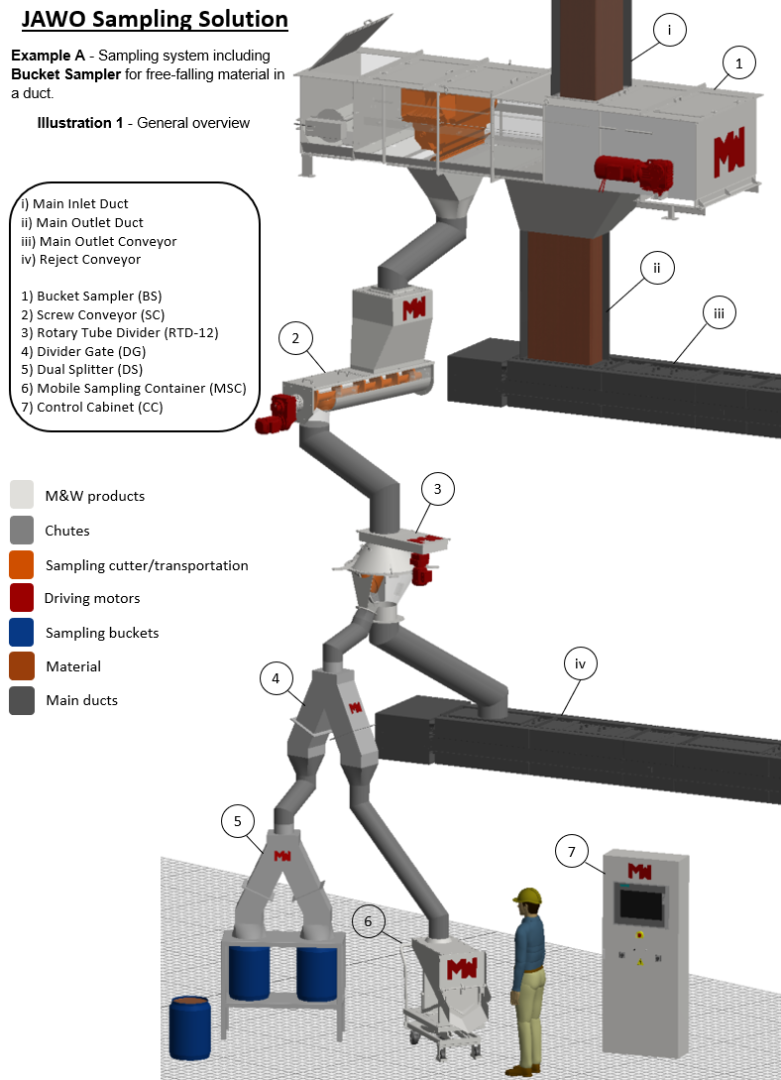
- Screw Conveyor (SC): Transports and/or dispenses the bulk material by rotation of a screw, connecting to a Rotary Tube Divider.
- Rotary Tube Divider (RTD): Splits the material stream into a sub-sample and a reject stream. This ensures that a portion of the material is available for detailed analysis while the rest is safely disposed of.
- Divider Gate (DG): Directs the representative material either to the Dual Splitter or the Mobile Sampling Container, allowing flexible sample management.
- Dual Splitter (DS): Splits the bulk material into two buckets, offering options for different sample sizes and quantities.
- Mobile Sample Container (MSC): Receives up to 200L of representative sampled material, making transportation and handling of samples efficient and safe.
Control Cabinet (CC): Controls, powers, and protects the sampling machines, ensuring reliable and consistent operation.
Where would we recommend a Bucket Sampler
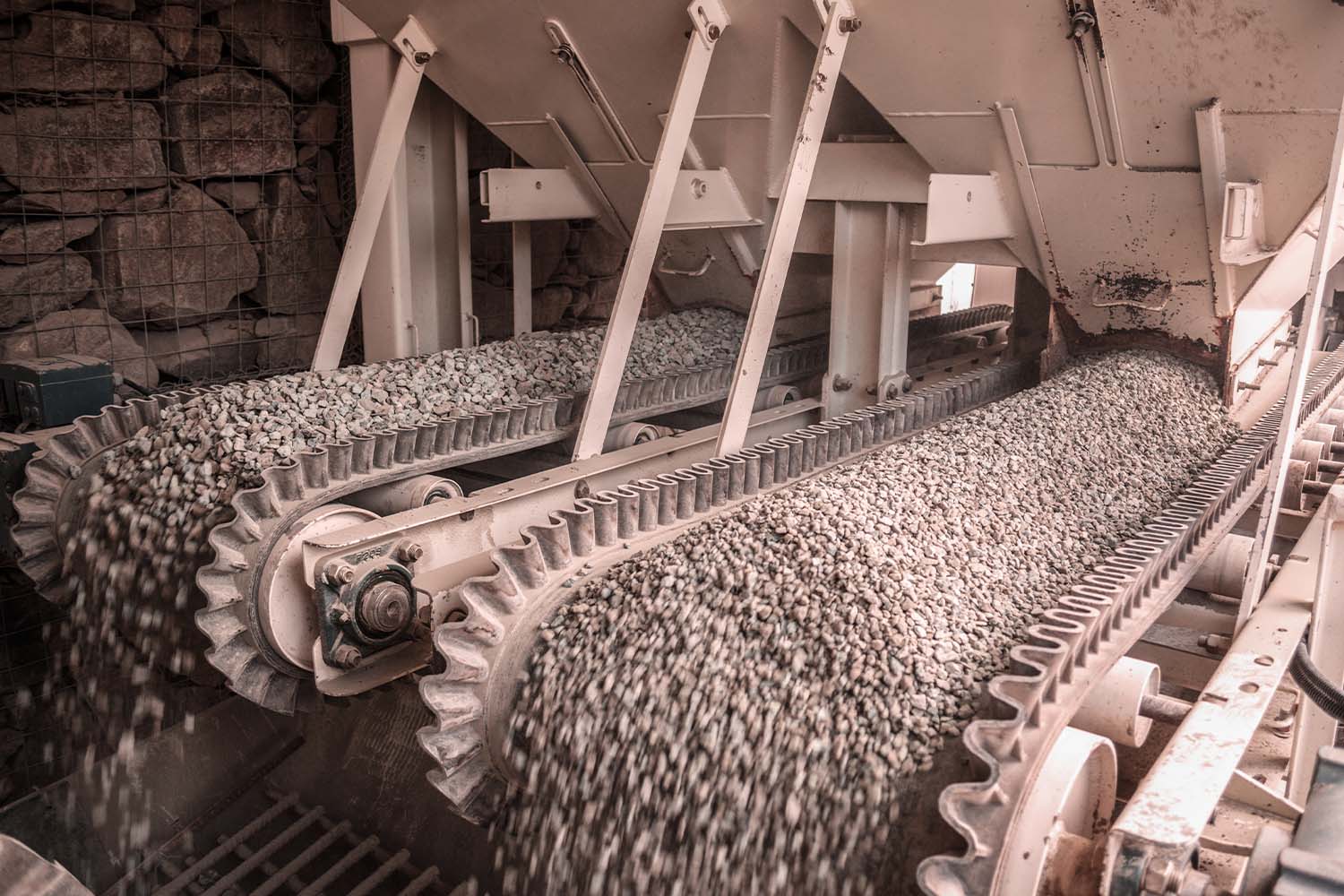
The Bucket Sampler ensures accurate and representative samples of bulk material in a falling stream, particularly for materials with a high content of dust. It is commonly used in industries such as mining, cement, agriculture, and bulk materials. The robust design of the Bucket Sampler guarantees minimal maintenance and long-term reliability, making it an ideal choice for high-demand applications.
Representative Sampling of Bulk Material from a Conveyor Belt
Sampling of bulk material from a conveyor belt can be very tricky as smaller particles tend to be at the bottom of the conveyor trough and larger at the top. It is therefore imperative the sampler captures a realistic cross section of the entire belts content. This is where the Cross Belt Sampling System comes into play. This system is designed to provide accurate and continuous sampling directly from the conveyor without interrupting the material flow.
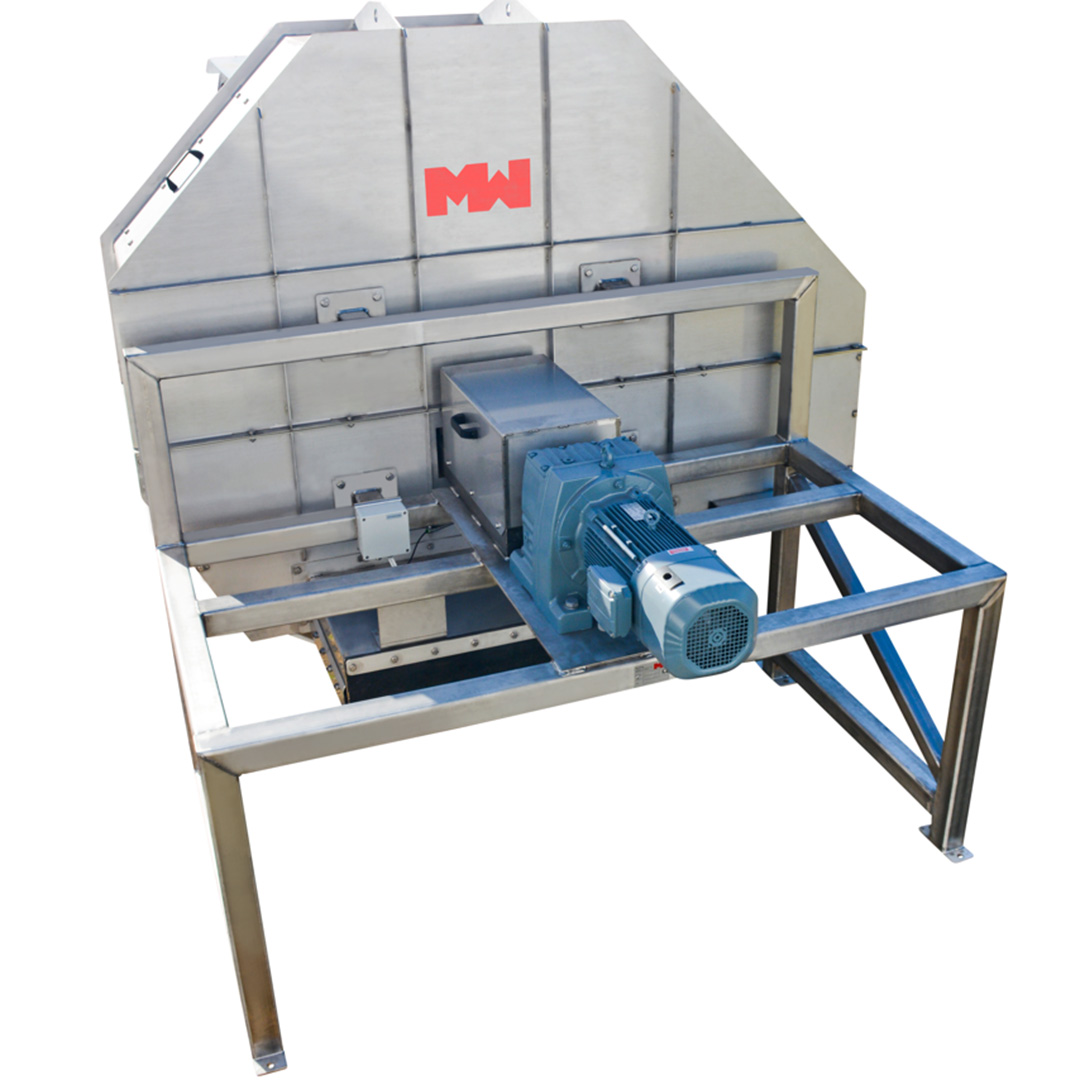
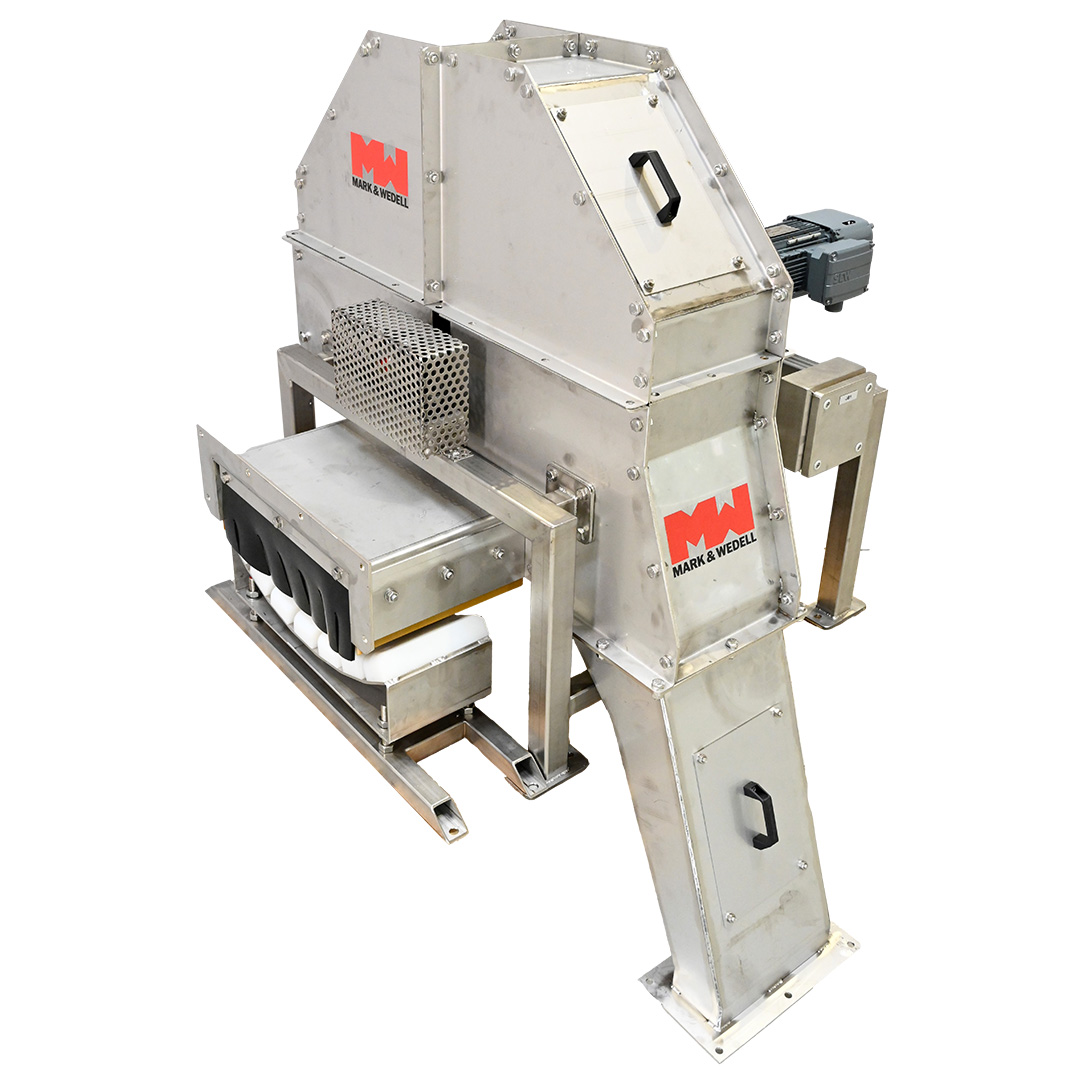
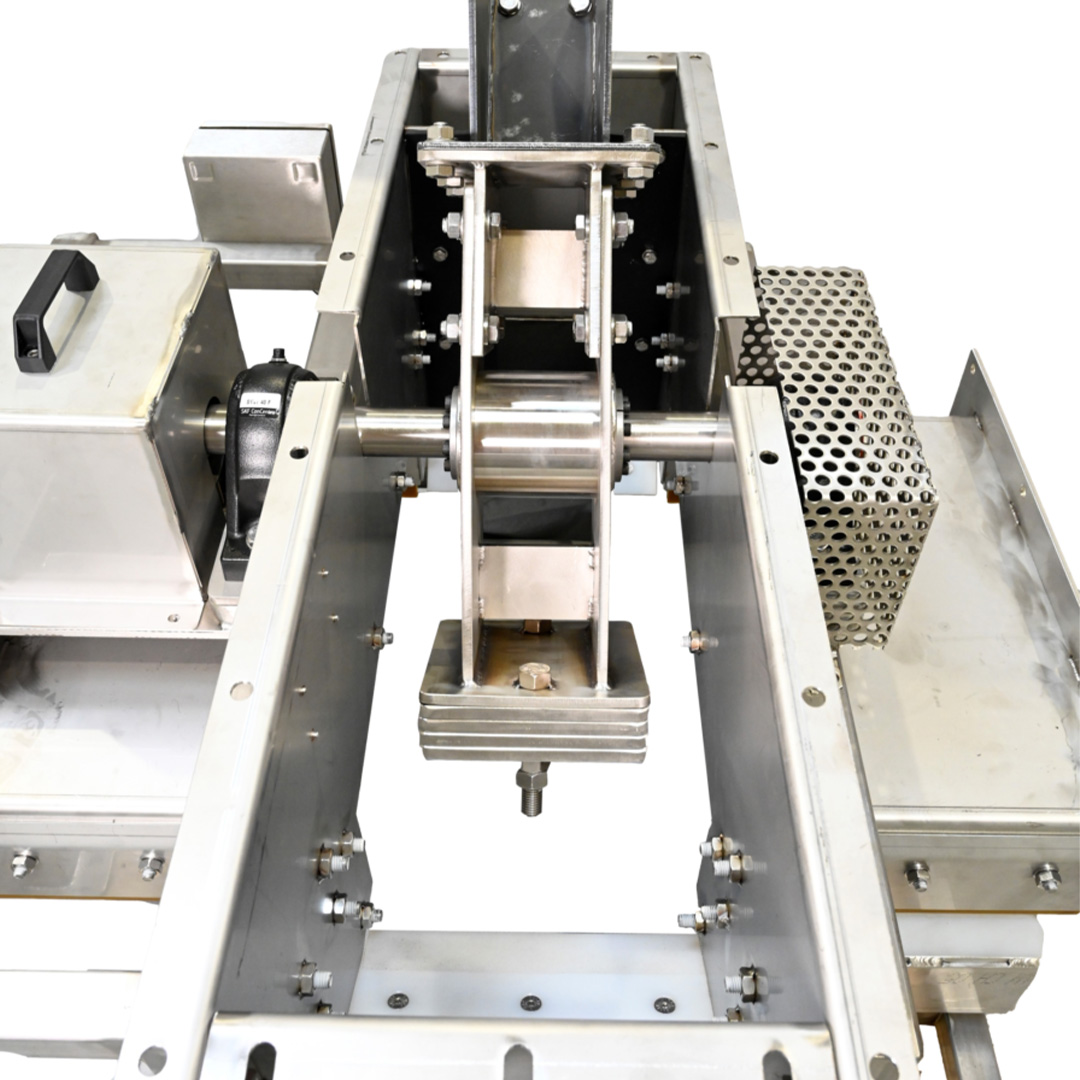
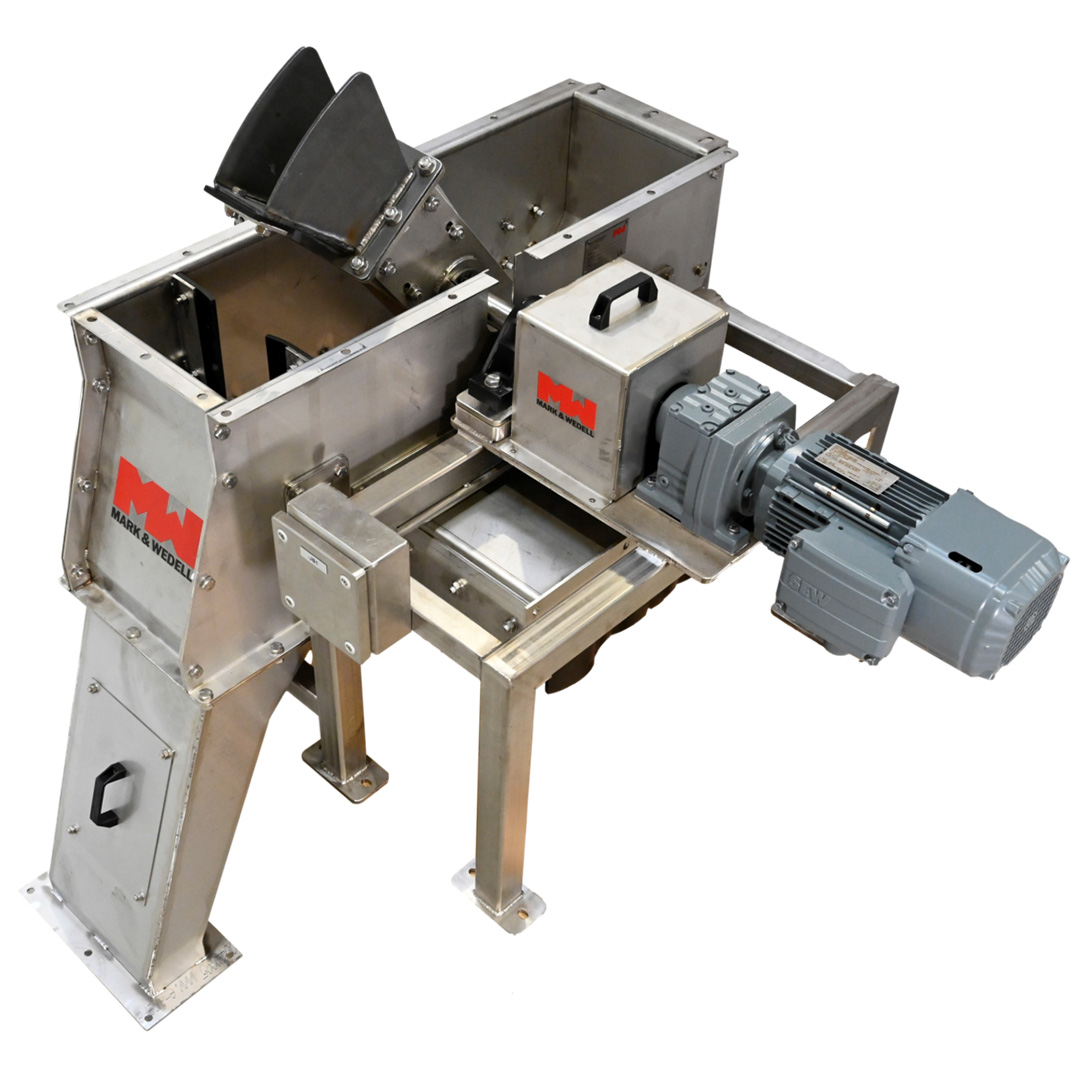
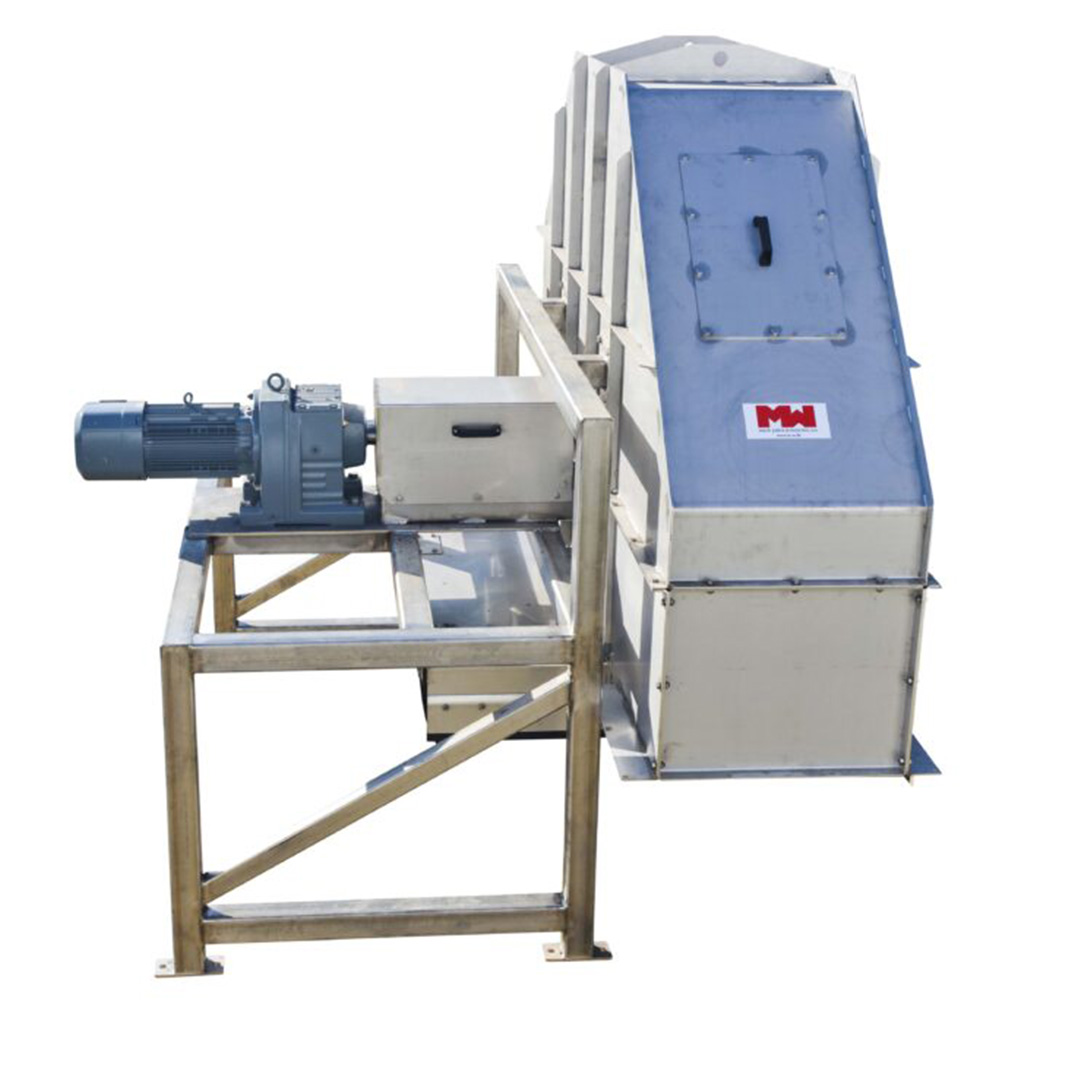
Cross Belt Sampler
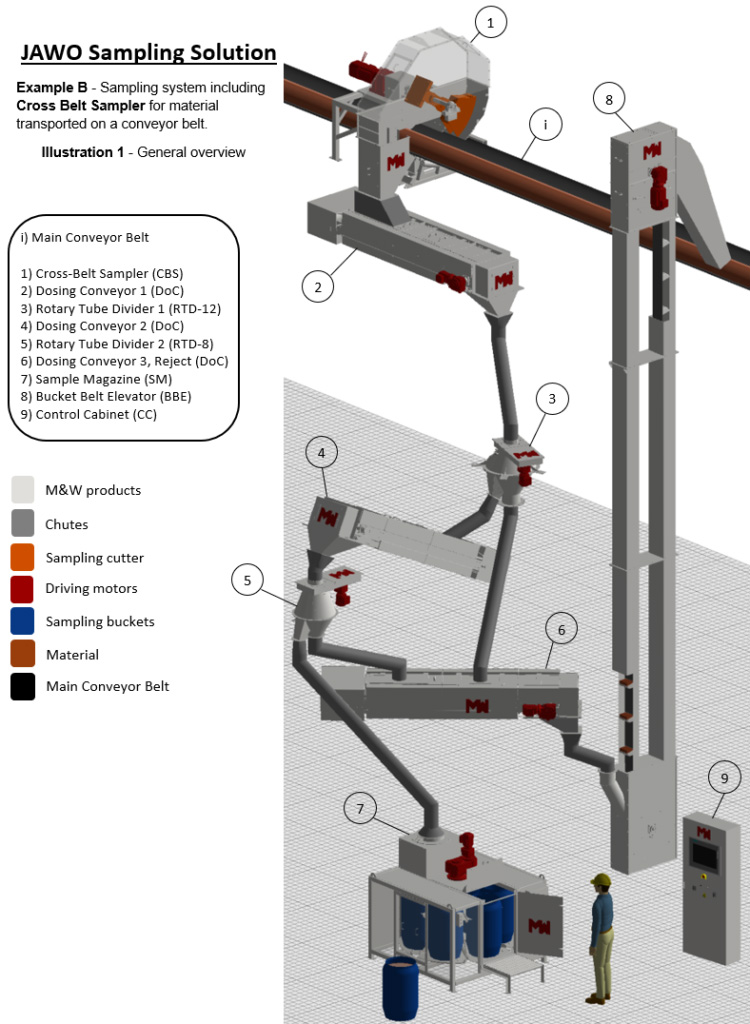
- Dosing Conveyor 1 (DoC): Ensures minimum spillage and correct dosing, connected to a Rotary Tube Divider. It is designed to handle a variety of materials with precision.
- Rotary Tube Divider 1 (RTD-12): Splits the material stream into a sub-sample and a reject stream, maintaining sample integrity and representativity.
- Dosing Conveyor 2 (DoC): Transports the sub-sample to a second Rotary Tube Divider, facilitating multiple stages of sample processing.
- Rotary Tube Divider 2 (RTD-8): Further divides the sub-sample, enhancing the accuracy of the sample distribution.
- Sample Magazine (SM): Automatically fills sample buckets with representative samples, preventing contamination and ensuring sample integrity.
- Bucket Belt Elevator (BBE): Lifts the reject stream back to the main conveyor belt, ensuring efficient material handling and reduced waste.
Applications for Cross Belt Samplers
Cross Belt Samplers are used for continuous and representative sampling of bulk materials on a conveyor belt, ensuring accurate and uninterrupted sampling in industries such as mining, agriculture, and other bulk materials. Cross Belt Samplers are designed to handle tough industrial environments, providing durable and reliable performance.
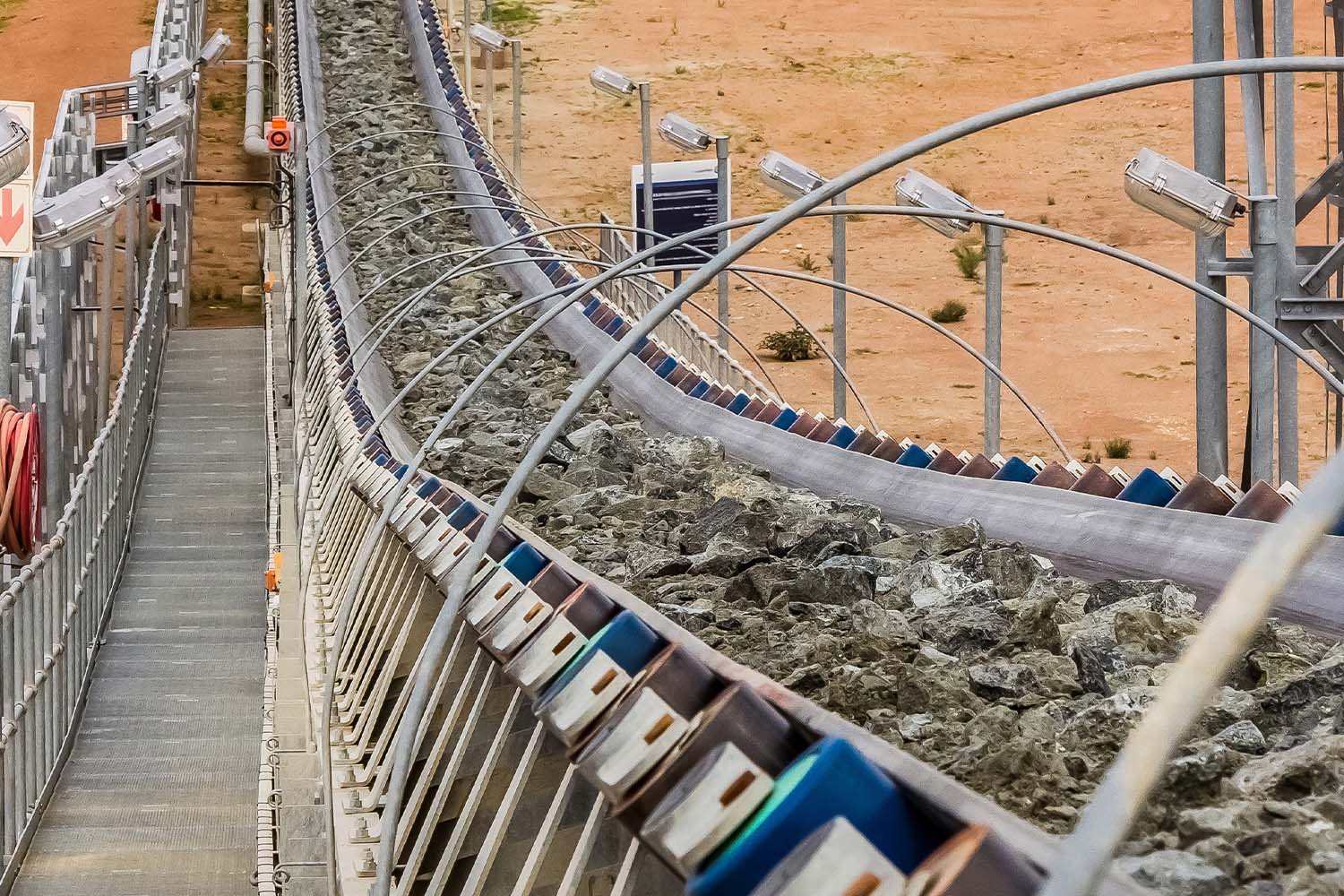
Representative Sampling of Bulk Material in a Conveyor Head Chute
To ensure a representative sampling of bulk material at the end of a conveyor belt, the Cross Stream Sampler can be fitted into the head chute of a conveyor. This type of sampler can be used if there is enough space where the conveyor discharges. The advantage of this type of sampler is a full cut of the falling material can be made, providing the most representative cut of the process material.
Cross Stream Sampler
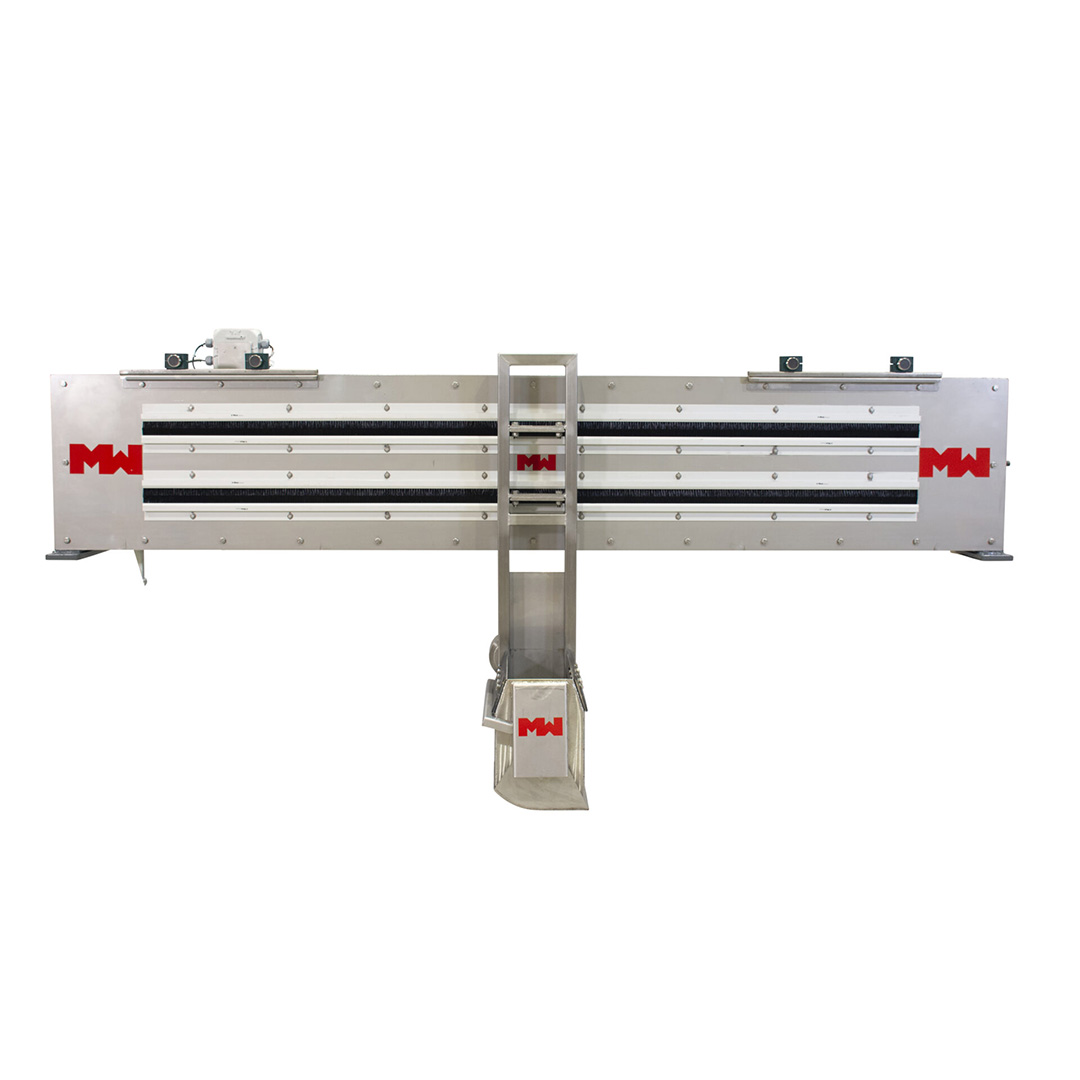
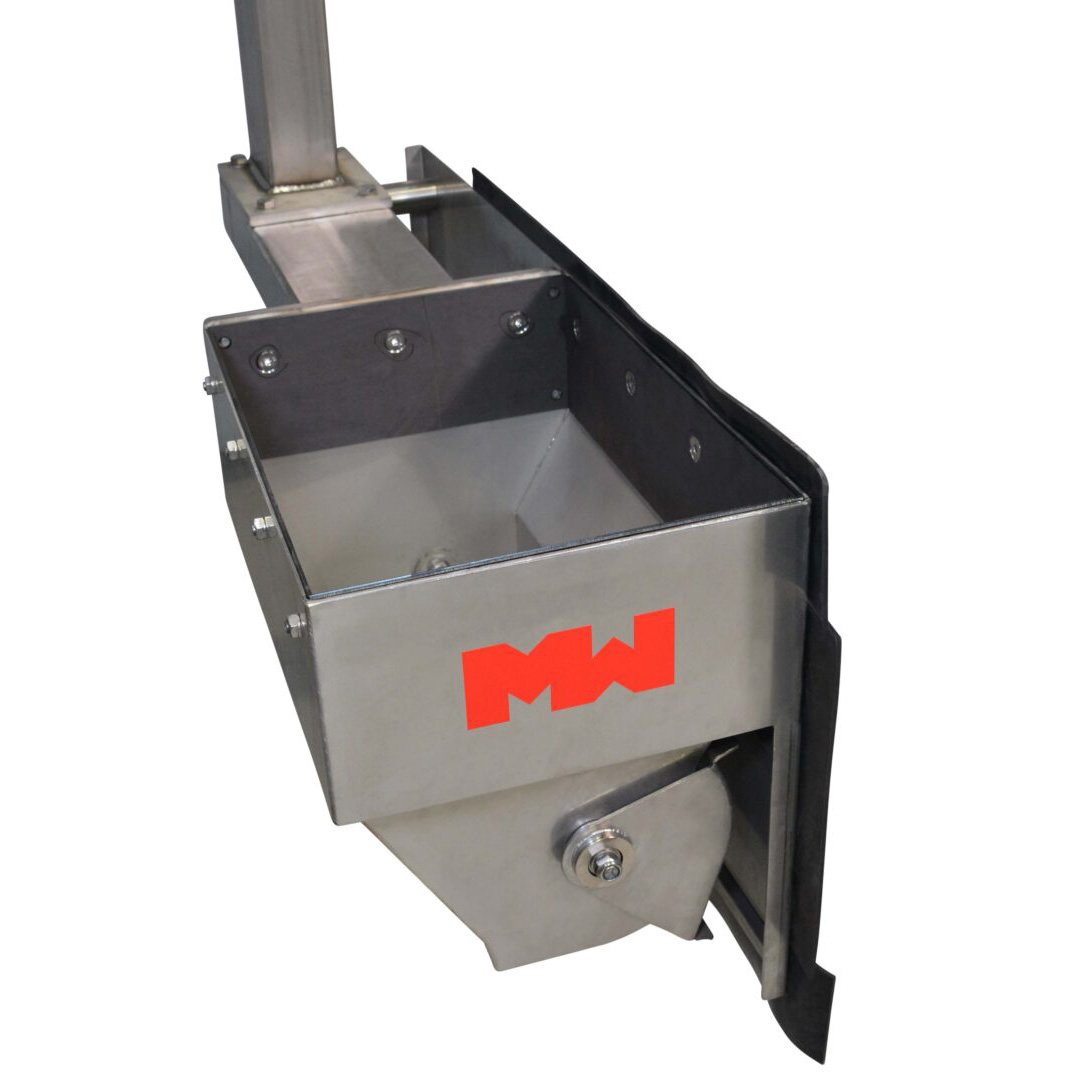
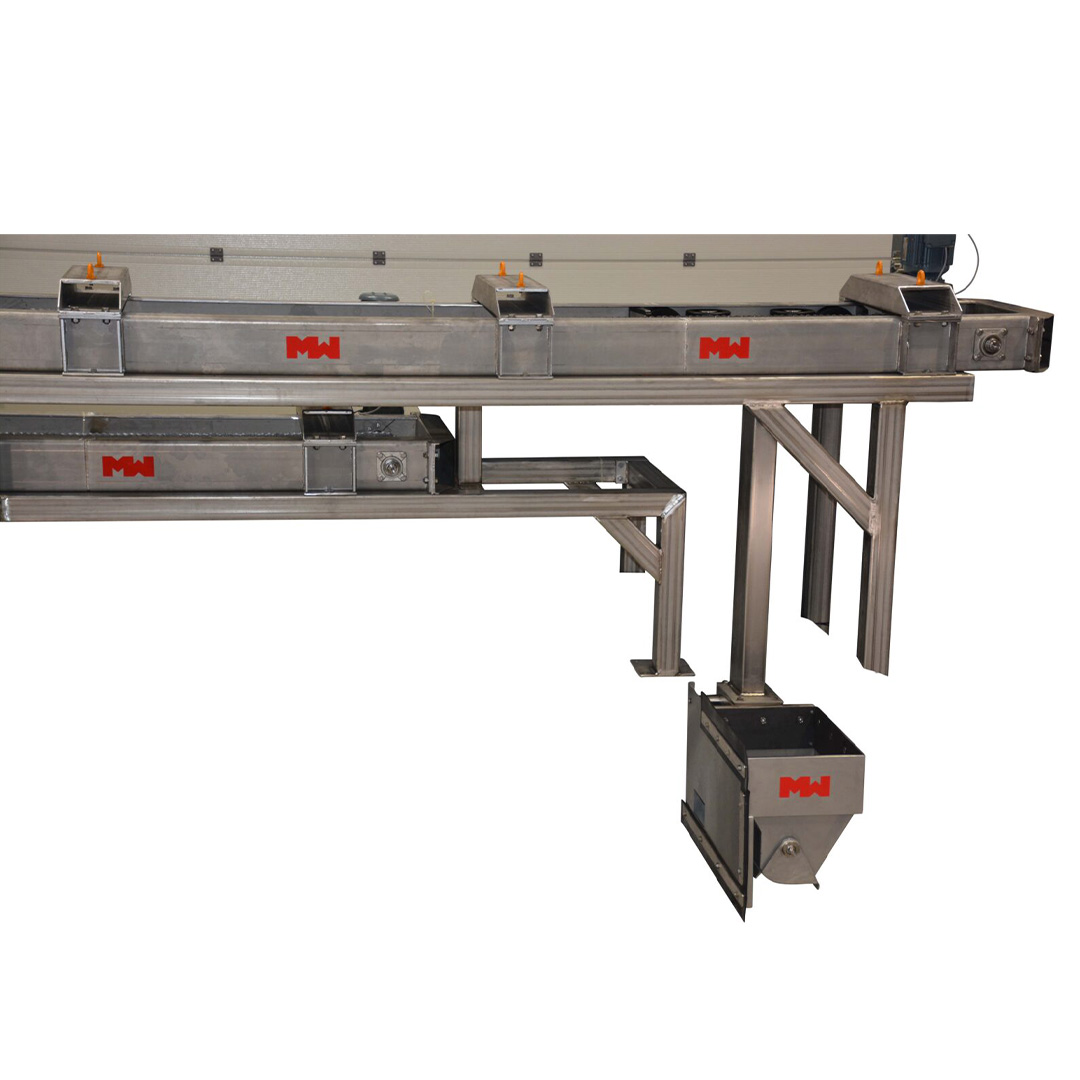
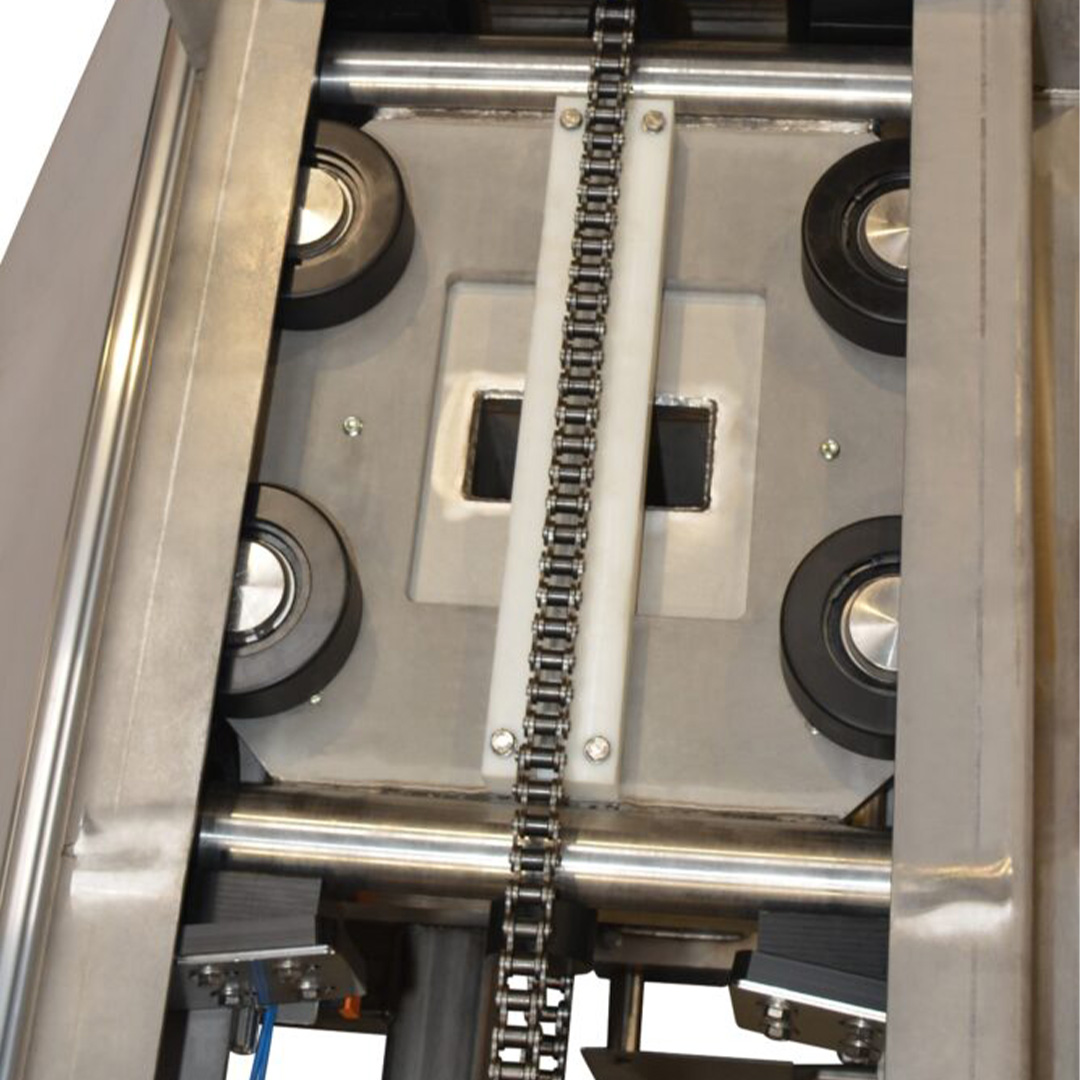
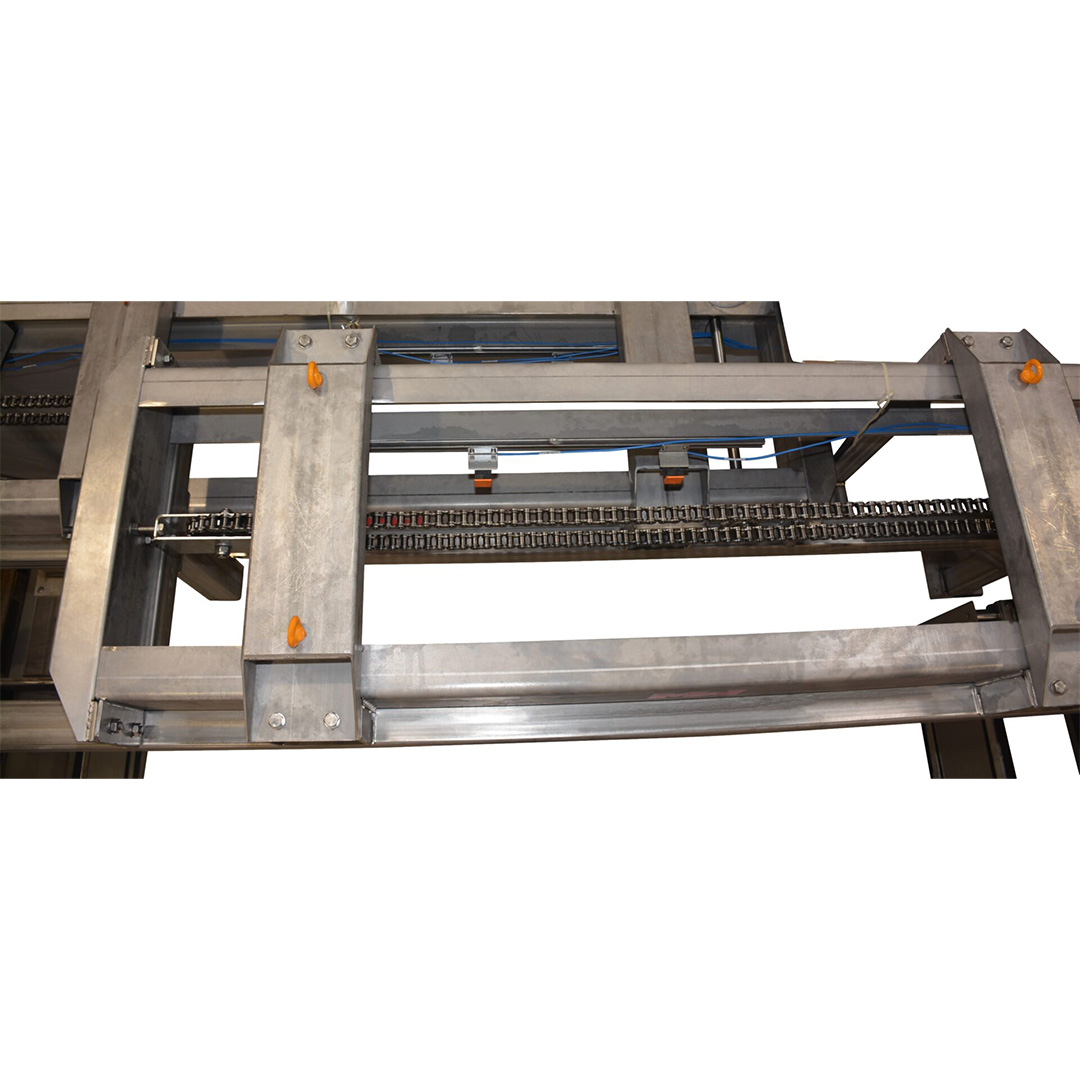
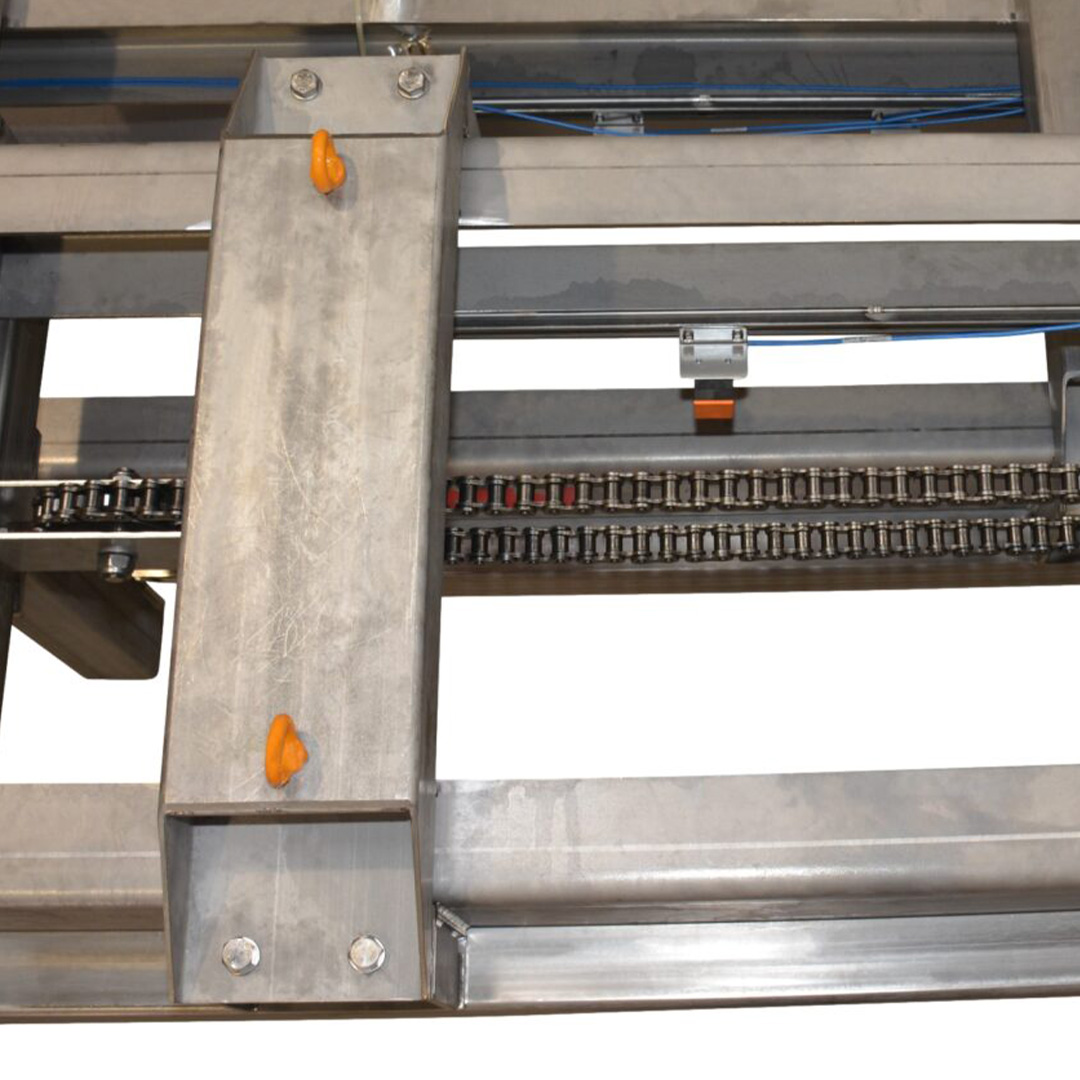
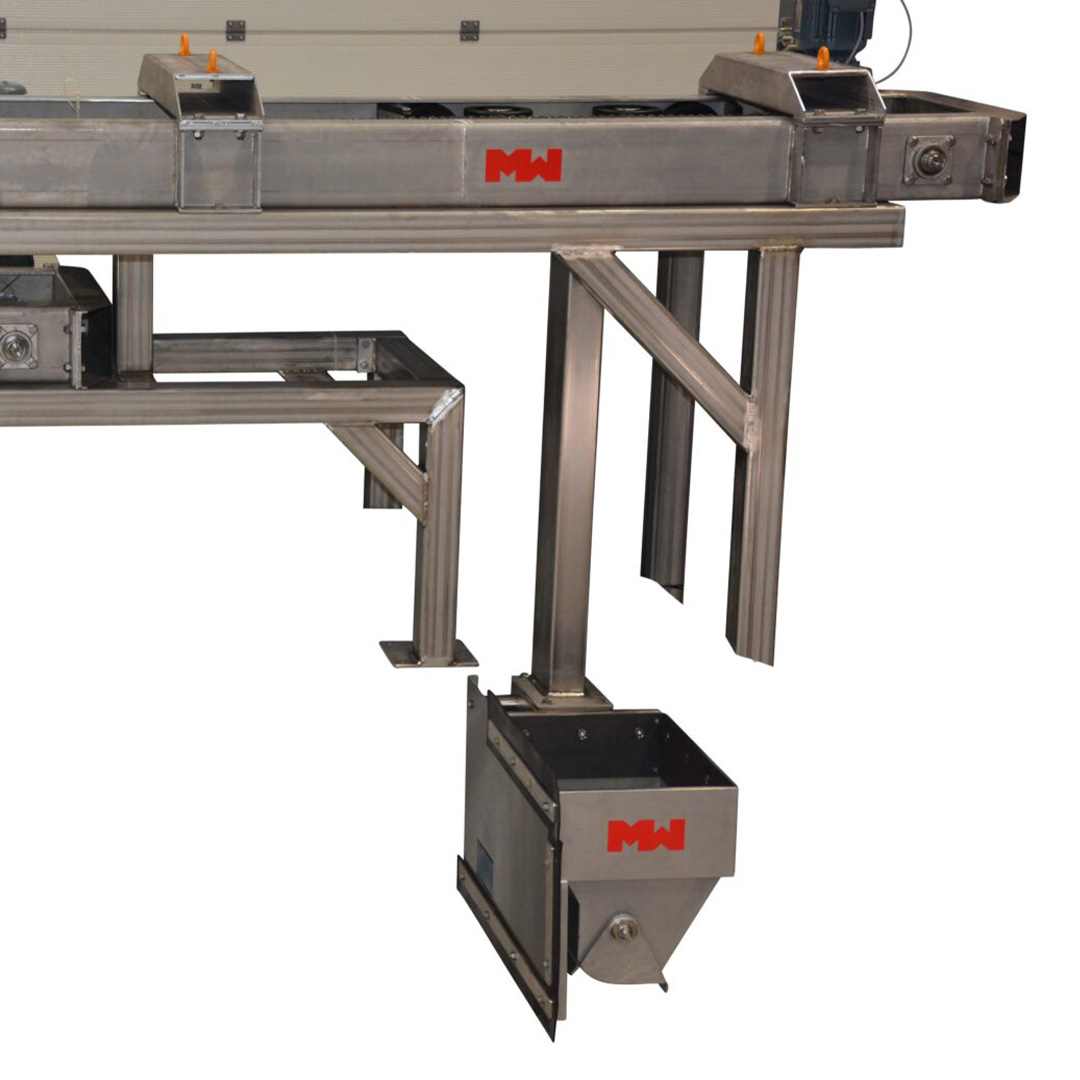
The Cross Stream Sampler (CSS) extracts a representative increment/cut of bulk material from a free-falling stream at the discharge point of a conveyor belt. Representativity of the increment is ensured by extraction of a complete cross section of the material stream. The sample is then handled in additional stages to ensure a final representation of the process is provided in the correct quantity according to the plants requirements. Techniques to reduce the sample size in a representative way can be seen in fig.3 and as outlined below.
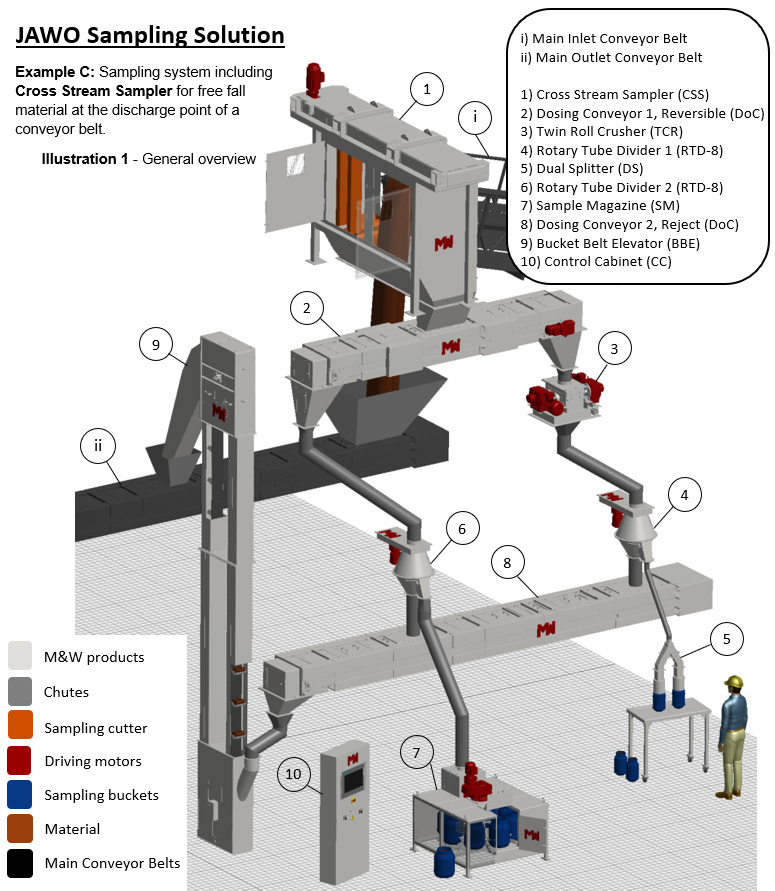
- Reversible Dosing Conveyor (DoC): Transports and/or dispenses the bulk material to either the Twin Roll Crusher or the Rotary Tube Divider, providing flexible sample processing options.
- Twin Roll Crusher (TCR): Reduces particle size by crushing, ensuring consistent sample preparation.
- Rotary Tube Divider 1 (RTD): Splits the material stream into a sub-sample and a reject stream, maintaining sample integrity.
- Dual Splitter (DS): Splits the bulk material into two buckets, allowing for varied sample sizes and configurations.
- Rotary Tube Divider 2 (RTD): Further divides the bulk material, leading to a Sample Magazine for accurate sample storage.
- Sample Magazine (SM): Automatically fills sample buckets, ensuring a composite sample and preventing contamination.
- Bucket Belt Elevator (BBE): Lifts the reject stream to the main outlet conveyor belt, ensuring efficient material handling.
- Control Cabinet (CC): Controls, powers, and protects the sampling machines, ensuring consistent and reliable operation.
More about the Cross Stream Samplers
Cross Stream Samplers are automated solutions for representative sampling of flowing streams of bulk material, ensuring accurate and continuous sampling in industries such as mining, minerals, agriculture, cement, bulk materials and many more. Cross Stream Samplers are designed for efficiency and durability, providing reliable performance in demanding industrial environments.
How can we help with your sampling needs
Materials We Sample
Our products are trusted by companies across a broad spectrum of bulk materials, including:
- Iron Ore
- Zinc Ore
- Gold Ore
- Platinum Ore
- Bauxite and Alumina
- Copper Concentrate
- Coal
- Mineral Sands
- Grain
- Seeds
- Cement
- Clay
- Aggregate
- Salt
- And many more…
Mark & Wedell
-
Bulk Material Sampling
Vezin Sampler (VS)
-
Bulk Material Sampling
Cross-Belt Sampler
-
Bulk Material Sampling
Cross Stream Sampler
-
Bulk Material Sampling
Bucket Sampler
Bulk Material Sampling Systems questions answered by our experts
What are the different types of cross belt sampler?
There are typically 2 types of sampler used to remove samples from a belt; these are rotary “sweep” type samplers that would move a rotating cutter through the material on the belt. The other type is a cross cut sampler moving a cutter left to right across the belt. Both types provide a representative and unbiased sample.
How many sampling stages would be needed?
This will depend on the initial quantity of sample on the belt and the desired quantity for the end sample. A sample handling system is designed based on the end users criteria. Sampling systems are typically a primary and secondary sampler but there may be further stages needed to reduce the sample quantity in a representative way.
How do I decide which sampler is best for me?
Our experts will provide an application sheet to be completed by the user. Based on the material, location of the sampling point, sample frequency and sample quantities we will custom design a system to meet your requirements.
How much space do I need to fit in a cross cut sampler?
Typically a primary full cross cut sampler will need approximately 2 meters in vertical height to fit into a process line. The physical size of the sampler will depend on the sample volume. If we are provided with drawings of the plant we can advise the best type of sampler for the location. As they are all custom made we can tailor to suit your process requirements.
What are the main objectives of sampling in metallurgical processes?
Sampling in metallurgical processes serves several key objectives: measurement of production, metallurgical accounting and corporate governance, trouble-shooting, and optimization surveys.