Fill level inspection
X-Ray, High Frequency and Infrared fill level inspection systems with rejection and diversion accessories
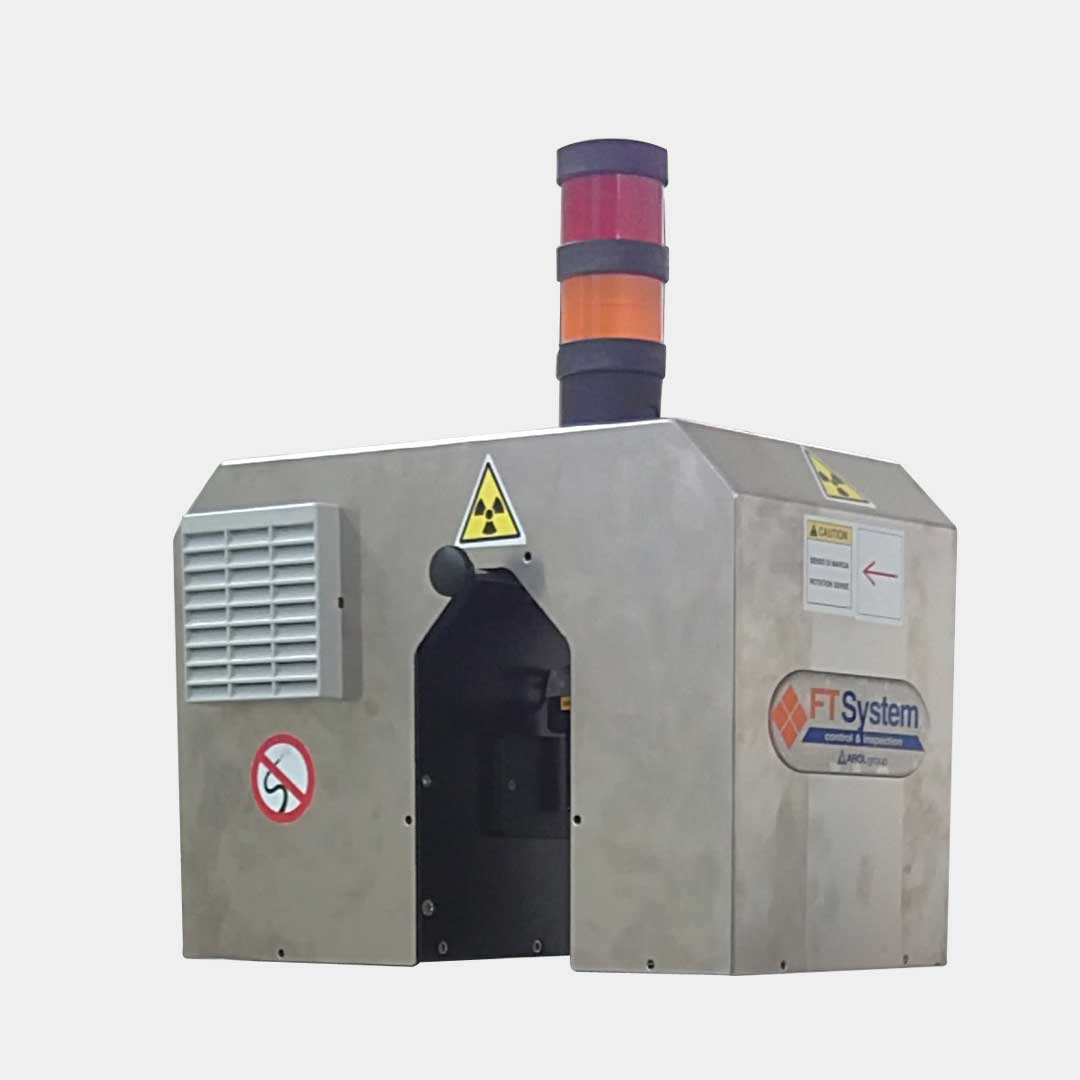

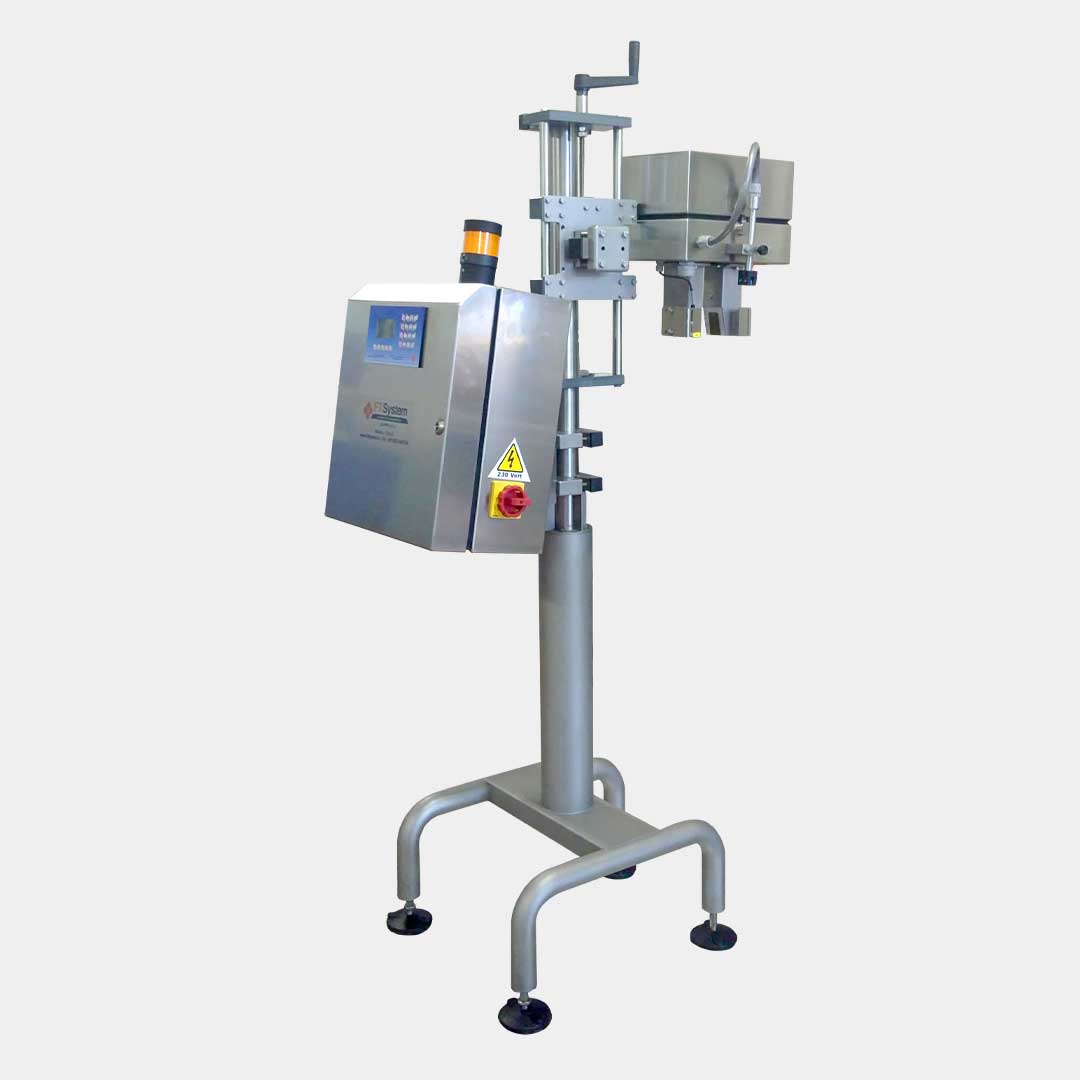
Fill level inspection
JWII offers unique solutions for package quality inspection for both filled and empty containers. Establishing itself since the company’s inception as a market leader of inspection systems for the beverage industry, packaging industry, food industry and pharmaceutical industries in Australia and New Zealand.
JWII Work together with leading brands around the world and are currently partnered with FT System of Alseno Italy who have designed very innovative and technical solutions for some of the industry’s most challenging Inspection problems.
Since the company’s foundation in 1982, fill level analysis has been at the forefront of the portfolio of products we offer. With a range of fill level monitors available JWII can provide specific solutions designed for your product and factory environment. Fill level control is one of the most important measurements as it not only allows the client to monitor and reject underfilled product it can also monitor overfilling and help in reduced waste and provide product yield savings
Fill level control systems are designed around global standards and to prevent disputes over the distribution of underfilled products, they help you and your business be confident your customers are receiving the correct amount of product matching the content disclosed on the label. The technology is designed to measure the product volume in the container at real time production speeds upto 2000 containers per minute, 120,000 containers per hour.
The Fill level equipment manages the measurement and we also handle rejection of non-conforming products. We can precisely reject only the non conforming container from the line, without compromising the good containers surrounding it. Rejection methods can be as simple as a push to knock the container from the line, to very sophisticated upright rejection and positioning ejectors using multiple fingers.
Fill level machines use approved testing methods and JWII offer a range of technologies to meet the requirements of the application in any container type. Technologies available include measurement with HF High Frequency and Infrared which are typically used for PET or glass bottles (without foil overlays), and X-Ray used for Bottles with foil overlay, Aluminium bottles and Aluminium or steel cans.
Fill level monitoring systems help the user minimise the number of rejects in the event of a filler malfunction by providing an alarm if a certain number of underfilled products are rejected. This allows for corrective action to be taken to avoid product wastage. This also helps with product quality going to market assisting in the reduction of customer complaints.
We also offer filler valve management software to provide information on specific filling valves that are not performing optimally either by under or overfilling the product.The filler valve management system also has a sampling function to allow the user to select specific valves and sample from those at full production speeds. This is particularly useful for filler diagnosis.
The filler valve monitor also allows cap and seamer faults to be monitored where a high, missing or misaligned cap can be tracked to the capping head. Seamer faults can also be tracked to the seaming heads. Samples can also be taken from specific cap or seamer heads using the sampling function embedded in the Filler management system.
Our range of fill level monitoring systems can also be connected with other inspection solutions, such as cap integrity inspection for misaligned or missing caps as well as inspection for label, bar code, date code inspection, leakage, vacuum, pressure measurement and many more.
JWII also offer a full range of inspection solutions through the entire package and product phase of the process, beginning with package inspection of cap quality and preforms to empty bottle and can inspection before entering into the filler, fill level control, cap closure inspection, sealing and seaming integrity, label inspection, code inspection weight control and rejection of the faulty products from the line.

- Fill Level Monitor
- Fill Height Measurement
- Underfill detection and rejection
- Overfill monitoring
- Filler Capper seamer control
- Push rejectors
- Upright rejectors
- Cap Integrity Inspection
- Filler valve monitoring
Common applications for fill level inspectors:
- Beverage Can
- Beverage Bottle
- Beer Can
- Beer Bottle
- Food Packaging
- Dairy Liquids
- Instant Coffee
- Packaged coffee based beverages
- Packaged Tea based beverages
- Milk powder
- Baby Formula
- Pharmaceutical liquids
- Pharmaceutical Vials
- Pharmaceutical Ampules
Typical fill level inspection questions answered by our experts
What is a fill level Inspector?
A fill level inspector is used to continuously monitor each bottle or can produced on a manufacturing line. The device is mounted over the line and inspects each package as it passes the inspector. If a container does not conform to specification the inspector can then send a signal to a rejection device to remove that specific package from the line.
What technology is used for a beverage can inspector?
Typically as beverage cans are made from Aluminium x-ray technology has to be used to penetrate the metal and measure the fill level. The x-ray beam is focused at a point on the container to measure the liquid. If liquid is present the x-ray density will be different to if liquid is missing, therefore we can very accurately determine the fill level in the can. In the past gamma fill level inspection was used for this application, but due to environmental concerns around the disposing of gamma sources and the fact they emit radiation even of powered off, most systems have now moved to x ray as it is far safer and once the x ray tube is turned off it is no longer emitting radiation and can be disposed of safely. Typical x-ray tube life is 5-10 years depending on the number of hours operated per day.
What is the meaning of fill level?
The fill level is the liquid level within a container where the correct amount of product is reached. In a container on the outside label there will be a volume disclosure for example 330ml for a typical beverage. The fill level is the point on the neck of the bottle that is reached when there is the correct amount (in this case 330ml)
Can checkweighers be used for fill level monitoring?
Typically beer and beverage filling lines are filling product at high speed and a checkweigher would not be able to respond quickly enough to each individual container's weight. Therefore fill level has been the preferred method over the weight for high speed on line measurement of beer and beverage containers.
Can the system provide a fill level warning?
When a product is filled on a production line and inspected using a fill level monitor the operator can be notified in a number of ways. The system can provide a visual alarm by way of a light or beacon, this is usually preferred as the manufacturing environment is noisy. Alternatives are an audible alarm like a siren. Another option is to have the inspection machine stop production after an initial warning and a number of sequential faults.
Does the fill level inspector come with a system manual?
We provide the manual in electronic format. The machines themselves also have embedded manuals and teach functions within the system software itself. An intuitive touch screen can be used to navigate the manual and ask common questions related to the equipment operation.
Can the system measure over and under fill level inspection?
This is available on our systems and the benefit of this is you are monitoring for non conforming products on both sides of your specification band. An under filled container is measured and rejected. An over filled product is measured and reported so the client can then adjust the filler to improve product yield. Using the filler monitoring software we can also identify the specific valves that are under or over filling to make the filler optimisation process easier.