Inline beverage analysers
Real Time analysis of beverages for process and quality control
Modular analysis for brix, diet, CO2 and O2 in beverages
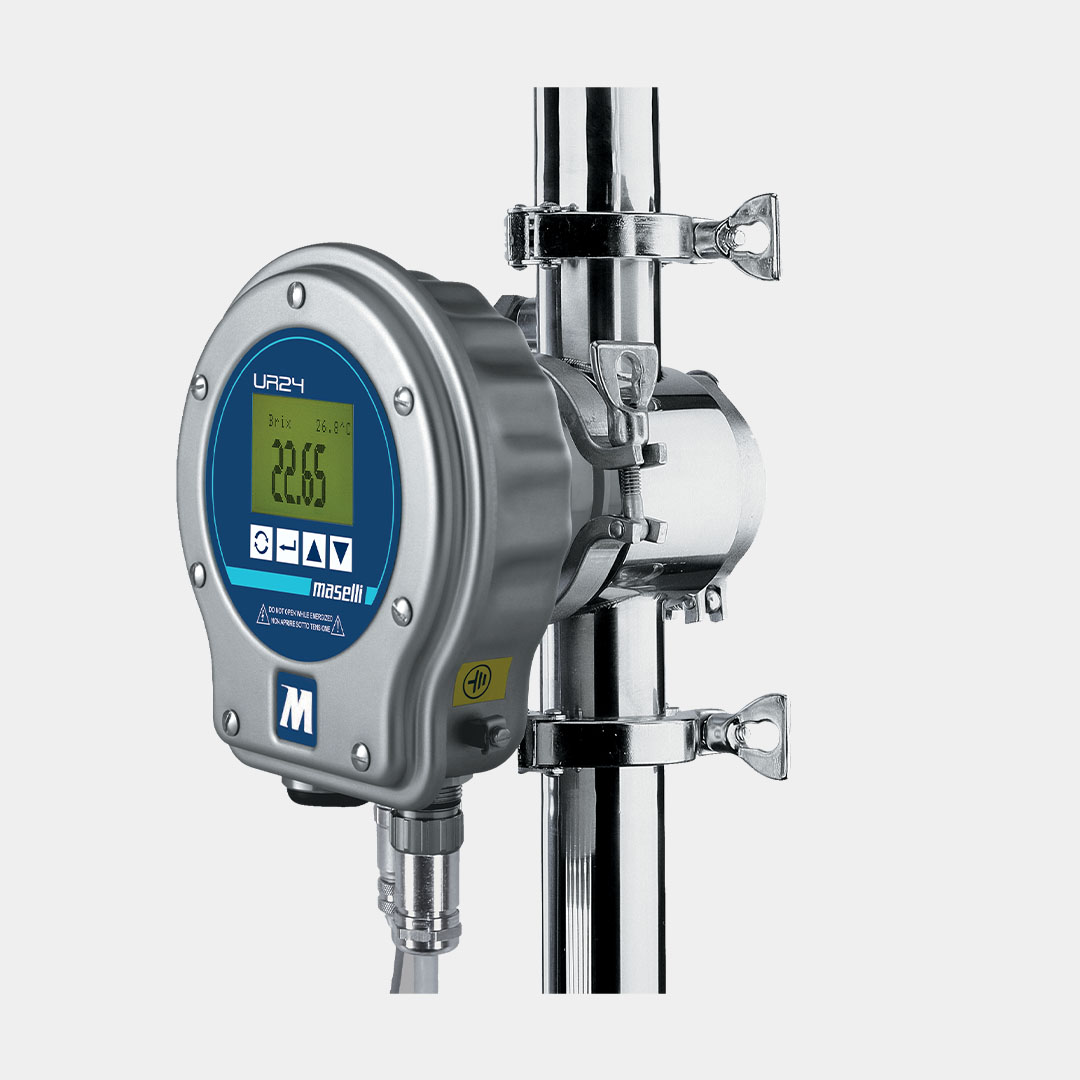
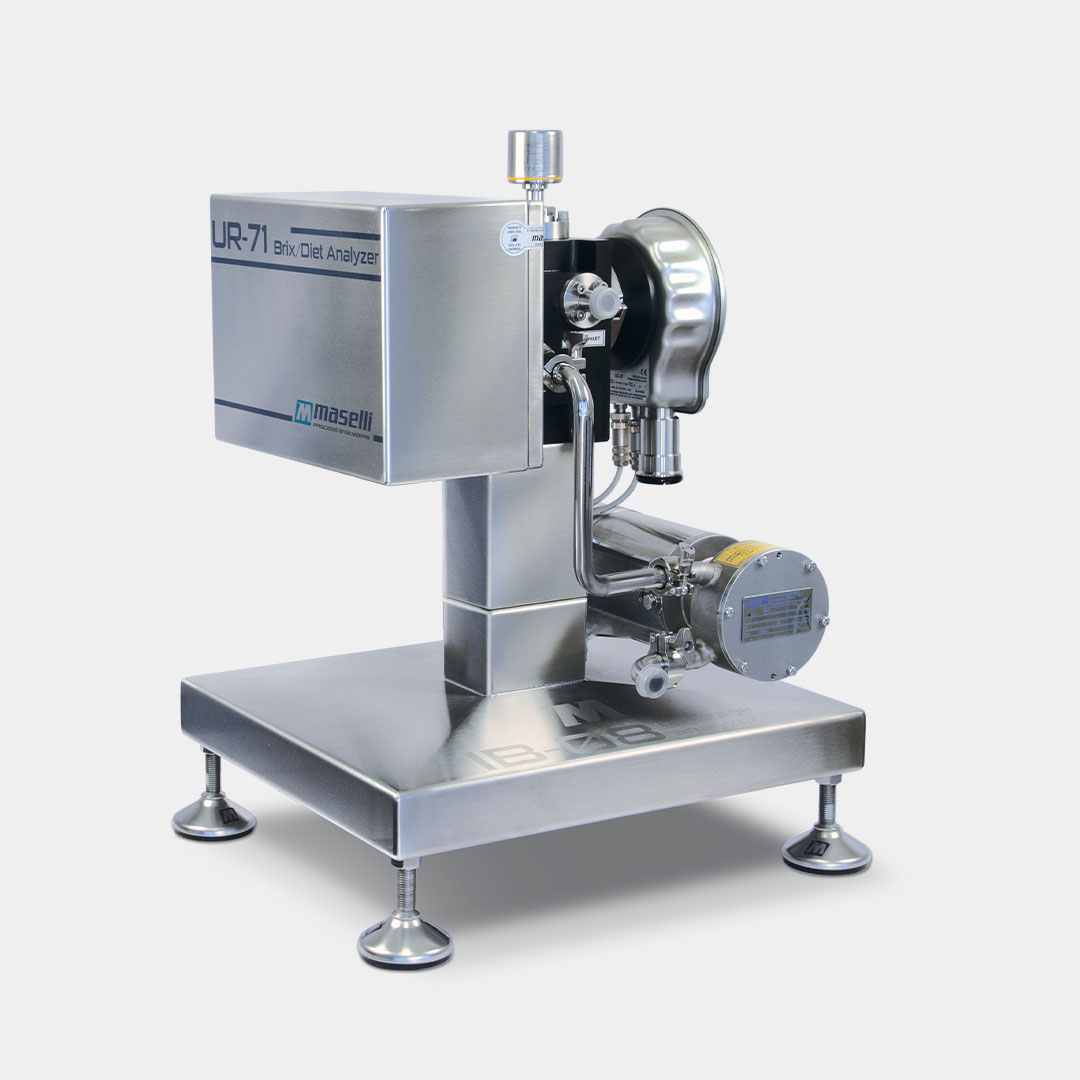
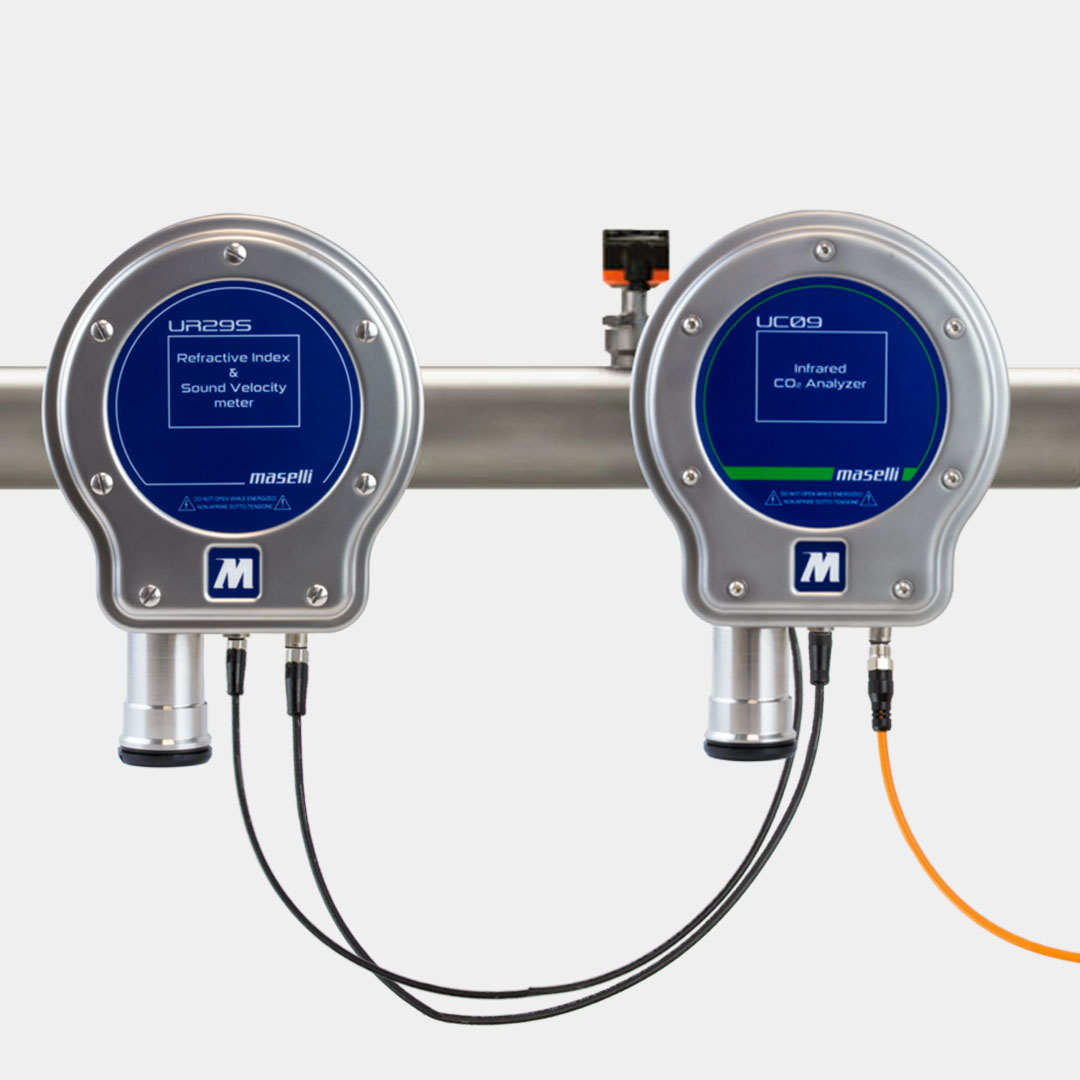
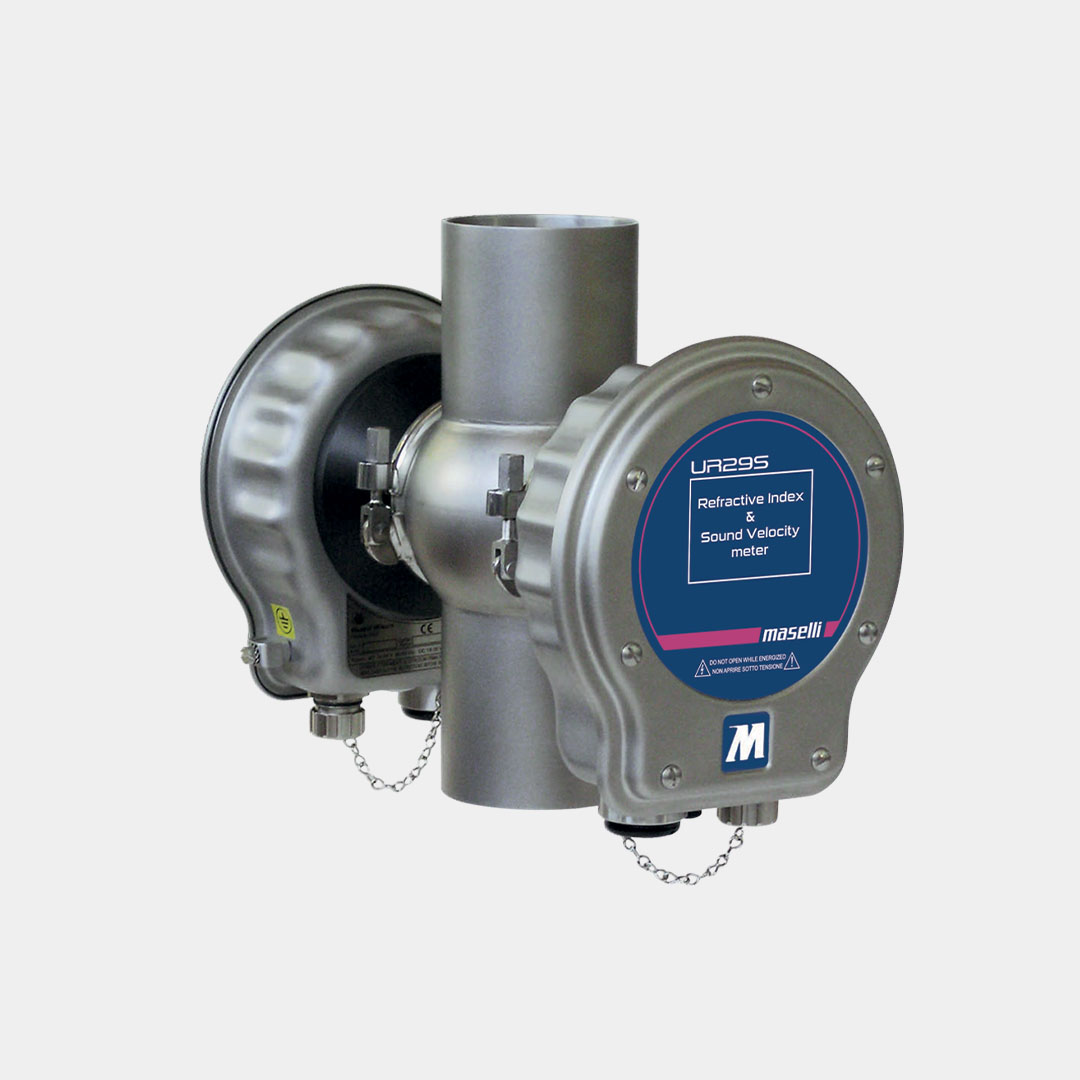
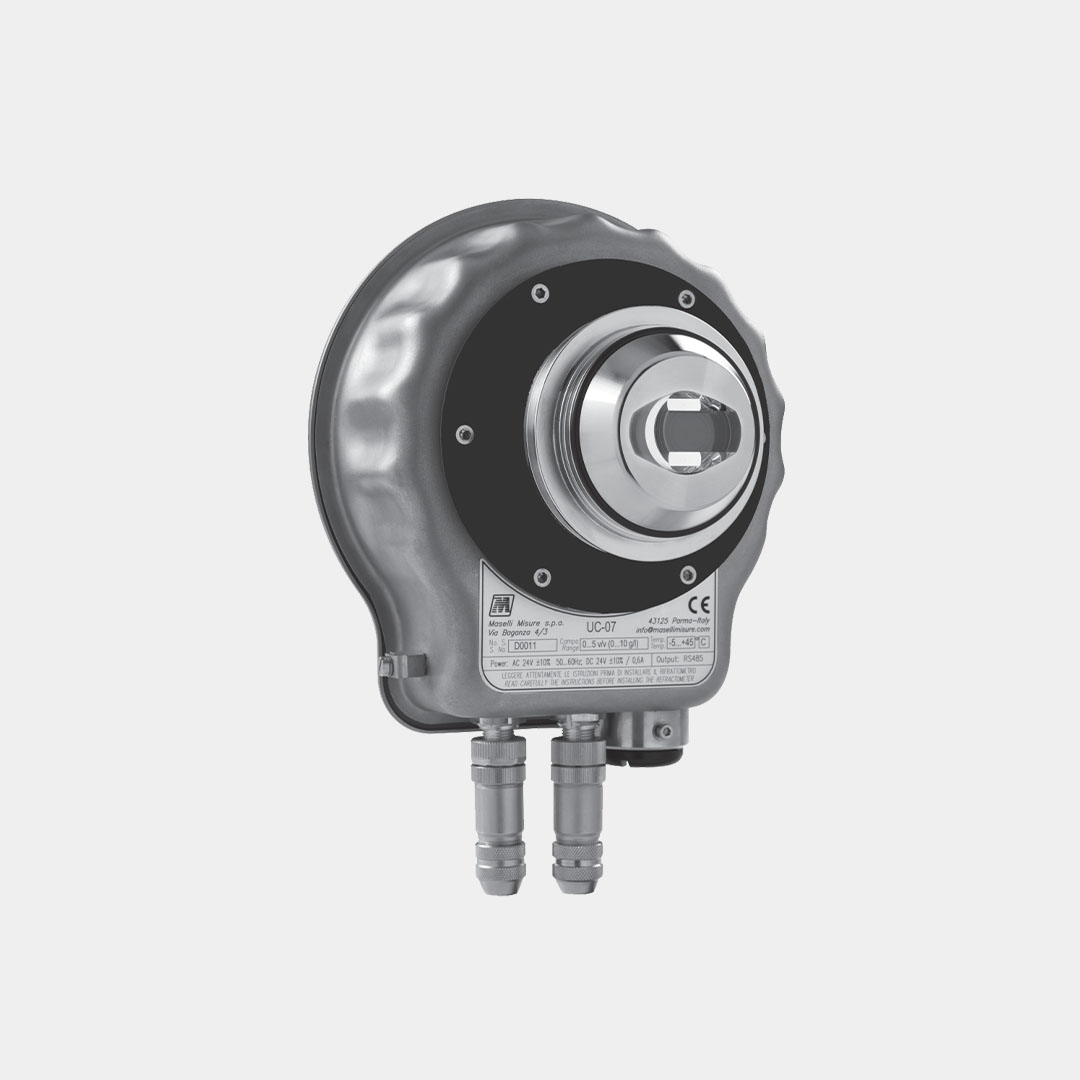
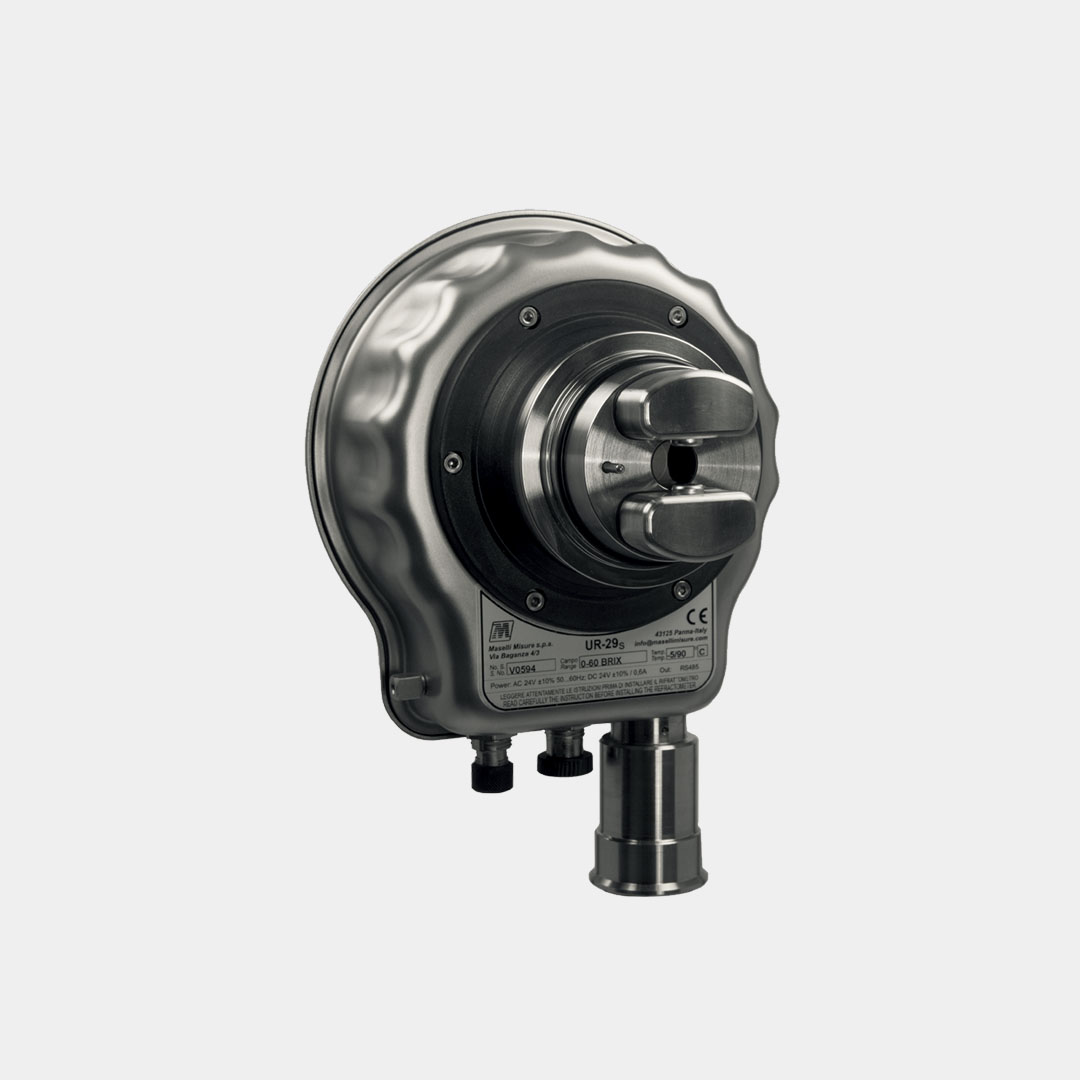
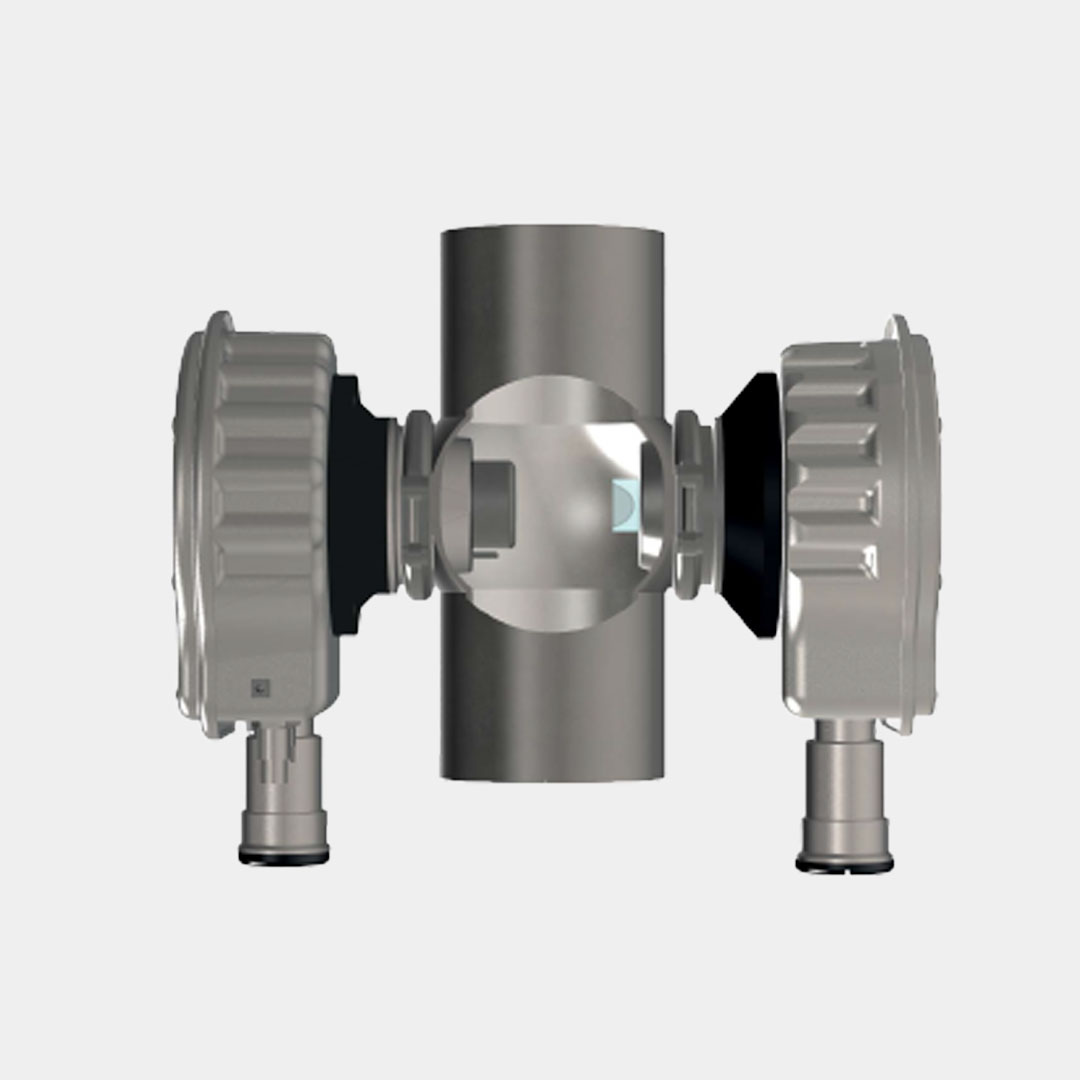
Maselli IB Series – In Line Beverage Analysers
Maselli have been manufacturing liquid concentration analysers since 1948. The Maselli range on In line beverage analysers covers a wide range of analysis giving rapid response to beverage process changes.
The Maselli range has analysers for all types of beverage from Carbonated Soft Drink, Juices, Dairy, Kombucha and Plant based beverages, Diet beverages with artificial sweeteners through to beverages with Alcohol.
In today’s rapidly changing market consumer trends are driving beverages towards health and wellness based products. The beverage analysers from Maselli are able to adapt to these changes with a modular range of analysers suited to every type of process liquid. With 70 years of experience we have developed a range of solid stature analysers capable of adapting to the bottlers analysis needs.
Beverage manufacturers require analysis of many parameters during the beverage making process. From the measurement of the Syrup to the Final Beverage there are many applications for the Maselli Inline beverage analyser. With its unique modular construction the Beverage analyser can be designed with the required analysis modules to build a system meeting each specific application’s needs. We provide modules for the analysis of Refractive Index, Brix, % Diet, Oxygen, Carbon Dioxide, PH and Conductivity.
The Maselli Beverage Analyser range consists of a number of unique analytical modules, these can be purchased separately or as a system.
Our core refractive index technology comes in various packages dependent on the application requirements for accuracy and process conditions. We have our U62 series of basic refractometers, UR32 series of standard units for general application and the the UR24 and 29 series of ultimate refractometers where the high levels of precision is the main focus. At the tope of our range us the UR71, Maselli are the only company to offer a specific refractometer for Diet beverages with artificial sweeteners. Our UR71 is a highly accurate refractometer is the diamond standard in precision measuring in the milli brix range and is the only approved in line refractometer for Diet beverages by some of the worlds largest bottling companies
Our IB07 is the only 100% inline system for continuous analysis of Soft Drink. Because the system was designed to be installed directly into the process line with Tri-Clamp fittings, there is no bypass loops or pumps. This design guarantees the best sanitary conditions eliminating any risk of contamination and this also reduces installation cost.
The IB08 version of the beverage analyser can be located and connected directly to the line or the buffer tank. With this installation the analyser can be used at the beginning of production when the line is being primed. This saves time at start up and also allowing for the “pump and run” concept where the line can be started automatically. Time is money in beverage production so the Maselli range helps the discerning bottler get a fast return on investment.
The sensors connect directly to our user-friendly controllers that display results locally for the operator and can be connected to the plant control system via various output protocols including, Ethernet, Profibus and Devicenet for process control. The system is fully networkable and can be connected to a PC running our Multilab software for data collection with data also able to be sent to the cloud for industry 4.0 requirements.
The Maselli systems are a true inline beverage analyser providing rapid and reliable analysis results for process and quality control. The analysers are all solid state with no moving parts making them robust and practically maintenance free.

Typical beverage analyser questions answered by our experts
How does a beverage analyser work?
A beverage analyser will consist of different technologies depending upon the parameters to be measured. For Brix and Diet analysis a refractometer is used this technology utalises light to measure liquid concentration. An LED sends the light into a sapphire or balf prism. The prism is in contact with the liquid and the light from the LED is reflected back from the liquid surface like a mirror. The angle of the reflected light will change depending upon the liquid concentration. This reflected angle is called the angle of refraction. A refractometer uses a CCD to capture the returned light from the liquid. A shadow will be cast on the CCD and this shadow will move based on the angle of refraction. A refractometer uses the output from the CCD to precisely calculate the liquid concentration based upon the CCD image.
If the beverage analyser is also measuring the CO2 in the liquid there are 2 technologies that can be used, an optical CO2 unit which uses Infrared light absorption to measure the CO2 and there is also a pressure and temperature CO2 unit that will capture a sample of beverage agitate it to get equilibrium and then measure the pressure and temperature and using Henry’s law calculate the dissolved CO2.
Other technologies can also be added to a beverage analyser which will provide measurements such as dissolved Oxygen, PH and Conductivity.
How do I connect the beverage analyser to the line?
The beverage analyser uses a sanitary connection called a tri-clamp fitting. These are certified sanitary connections for the food and beverage industry. Normally a tri clamp connection fitting is welded into the process line and then the beverage analyser fits into this using a tri clamp connection. The maselli beverage analysers are purely in-line and are not mounted in by-pass like some competitive systems. In the beer industry we also use a sanitary fitting called a Varivent connection.
How do I get the data from the beverage analyser?
The beverage analyser can communicate using analogue and digital signals. These outputs can be connected in a variety of ways to get data collection. Maselli provides a software package called MultiLab and this would connect to the beverage analyzer digitally via Ethernet or RS485. The data from the analyser is captured in the software and stored for historical purposes. We can also connect the units to the plant PLC or systems for closed loop control and data collection using analogue and digital signals such as Profibus or Devicenet for example.
What is an inline beverage process?
The term inline beverage process is used when a measurement of a product is required to be done during the manufacturing process. This liquid concentration is analysed during the manufacturing process. This becomes especially important if the manufacturer wants to improve quality or increase yield from the liquid.